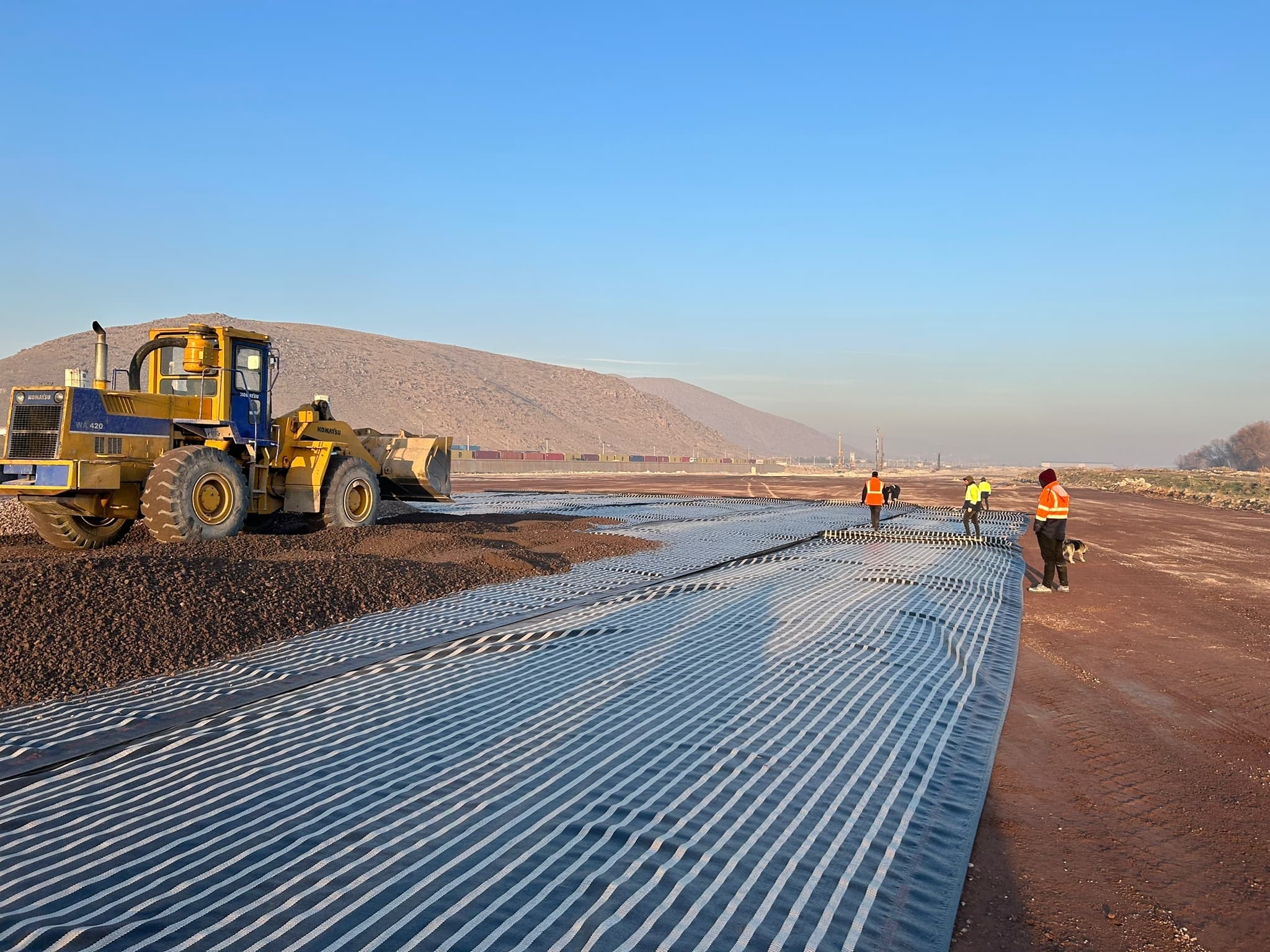
Subgrade stabilization of a railway with MIRAFI HMi
Overview
In late 2022, a civil engineering project commenced at Kayseri Boğazköprü, Turkey. This project was strategically designed to stabilize the subgrade beneath a railway line and an adjacent container park. With an expected completion date in 2024, this project is pivotal for enhancing the durability and safety of the railway infrastructure, ensuring it withstands the dynamic loads imposed by both train traffic and stationary loads from the container park. The project was spearheaded by an international team of experts, working with local expertise. Solmax played a crucial role as the specifier and supplier of the geosynthetics used in the project.
Challenge
The project required a solution for the container storage area that would prevent the costly need of deep soil improvement techniques. An alternative construction method was needed to enhance the load-bearing capacity of the soil and the long-term stability of the structure.
The project faced logistical challenges, notably the tight timeline necessitating considerable progress during the Christmas season of 2022, which demanded efficient and timely delivery and installation of materials.
Solution
To address the project's complex needs, Solmax provided 120,000 m² (1,291,669 ft²) of MIRAFI Geolon PET 200/50 and 78,000 m² (839,585 ft²) of MIRAFI HMi These materials were chosen for their superior mechanical properties and their compliance with rigorous national and international standards such as BS 8006 and EBGEO. The selected materials each had specific roles:
MIRAFI Geolon PET 200/50: This uniaxial geosynthetic was installed beneath the railway tracks to provide critical reinforcement function with its high strength. At the same time, it prevents the migration of fine materials from weak underlying soils into the engineered fill and enhances the load distribution across the subgrade and the DSM columns, thereby stabilizing the railway foundation against dynamic loads.
MIRAFI HMi: Used beneath the less load-intensive container park, this material complemented the rock fill by providing necessary stabilization while also ensuring separation and filtration. This helped to improve the bearing capacity of the soil in that area without needing costly foundations techniques, which usually consume much more energy.
The use of these two different geosynthetics allowed for tailored geotechnical solutions based on the specific requirements of each site section. This innovative approach eliminated a part of the need for DSM columns, thereby reducing environmental impact and project costs and highlighted the ability to adapt geotechnical applications to varying load conditions effectively. The materials could handle significant tensile stresses, distributing loads more evenly, and maintaining the structural integrity of the full area.
The Kayseri Boğazköprü project shows how advanced geotechnical solutions can be effectively employed to address complex engineering challenges in infrastructure projects. By selecting appropriate geosynthetic materials, based on performance criteria and environmental impact considerations, proper engineering ensured long-term stability and performance. The project not only serves as a model for similar future endeavors, but also contributes significantly to improving the knowledge in civil engineering, particularly in the practical application of geosynthetics in subgrade stabilization.
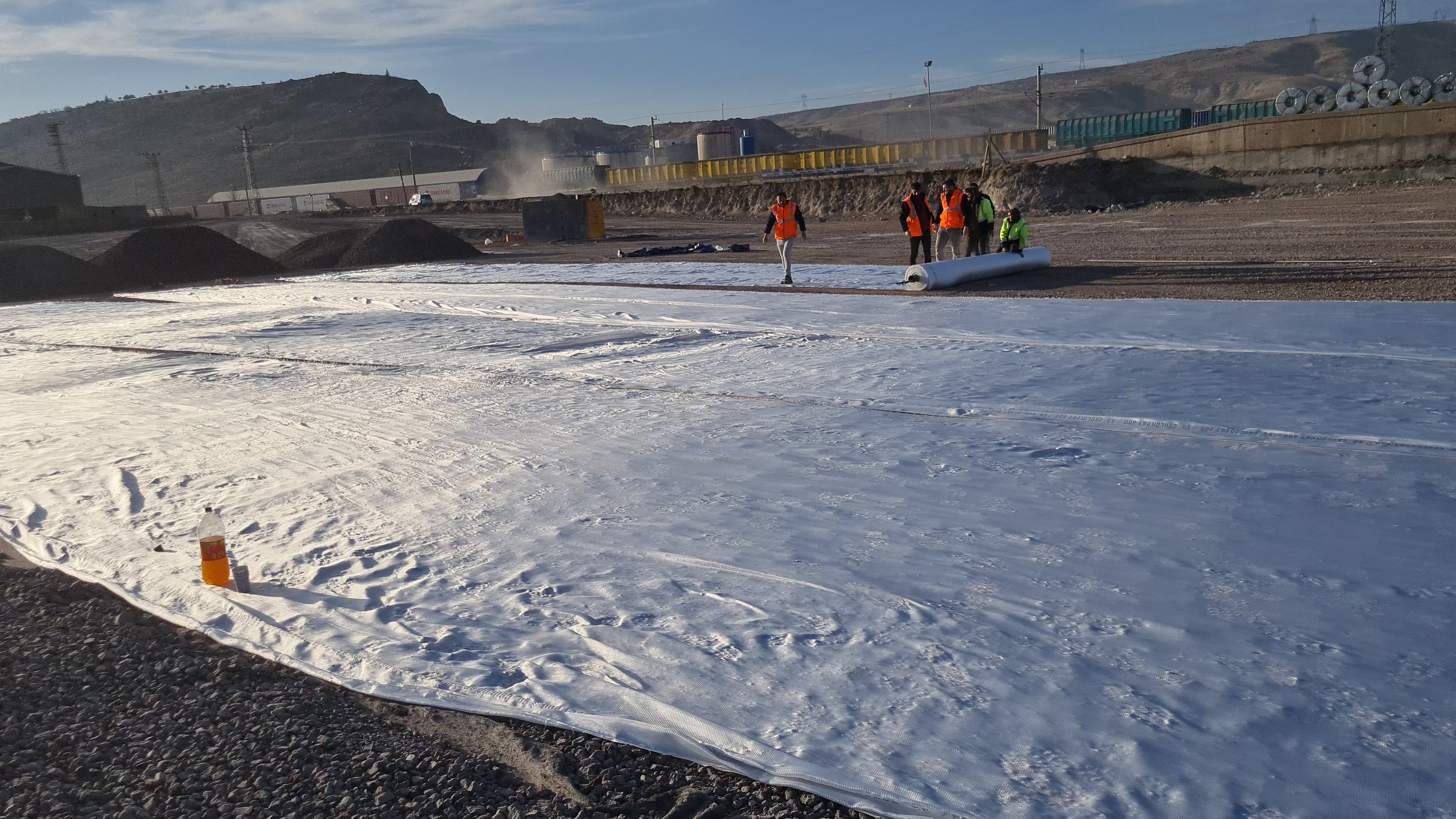
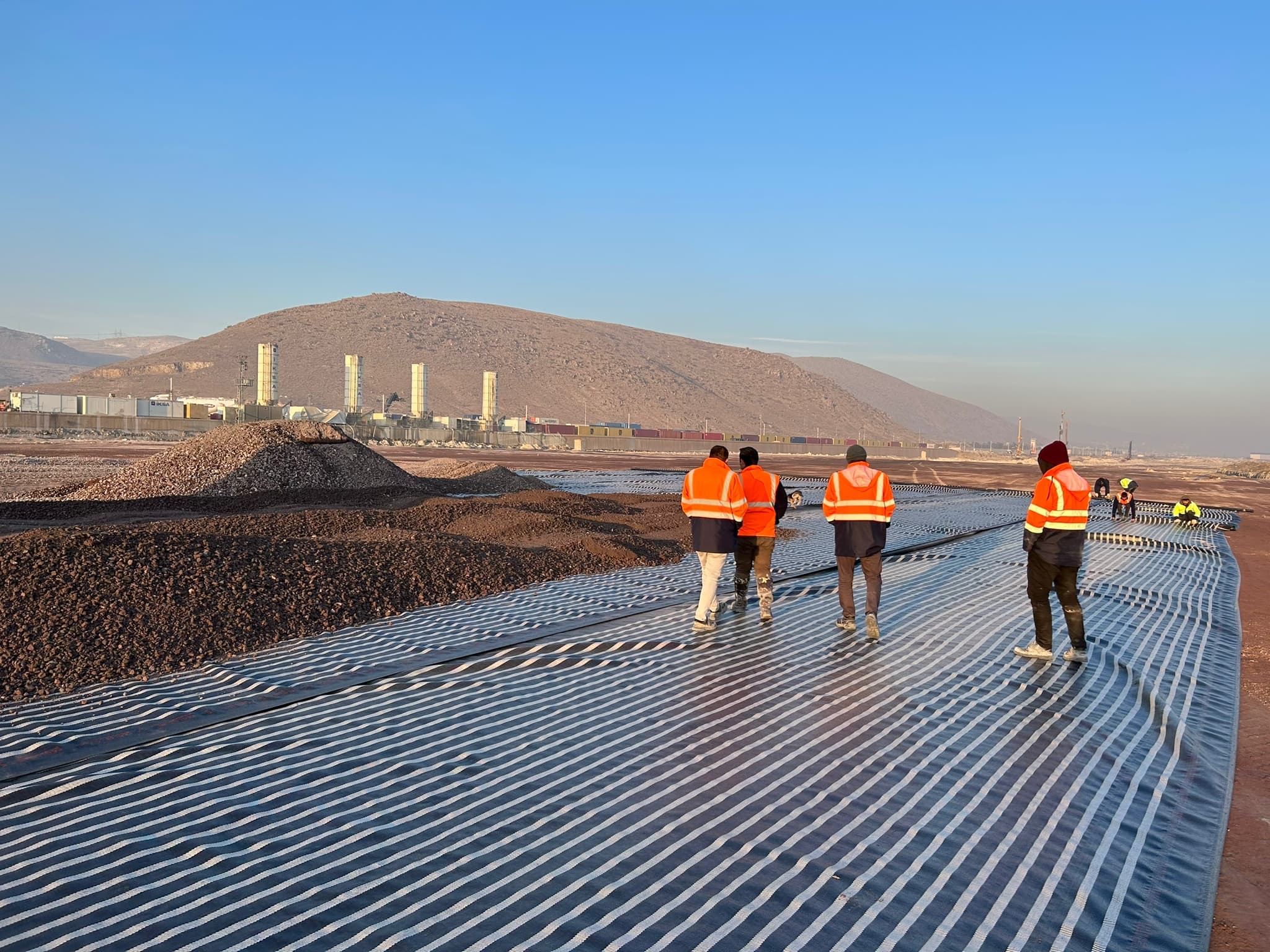
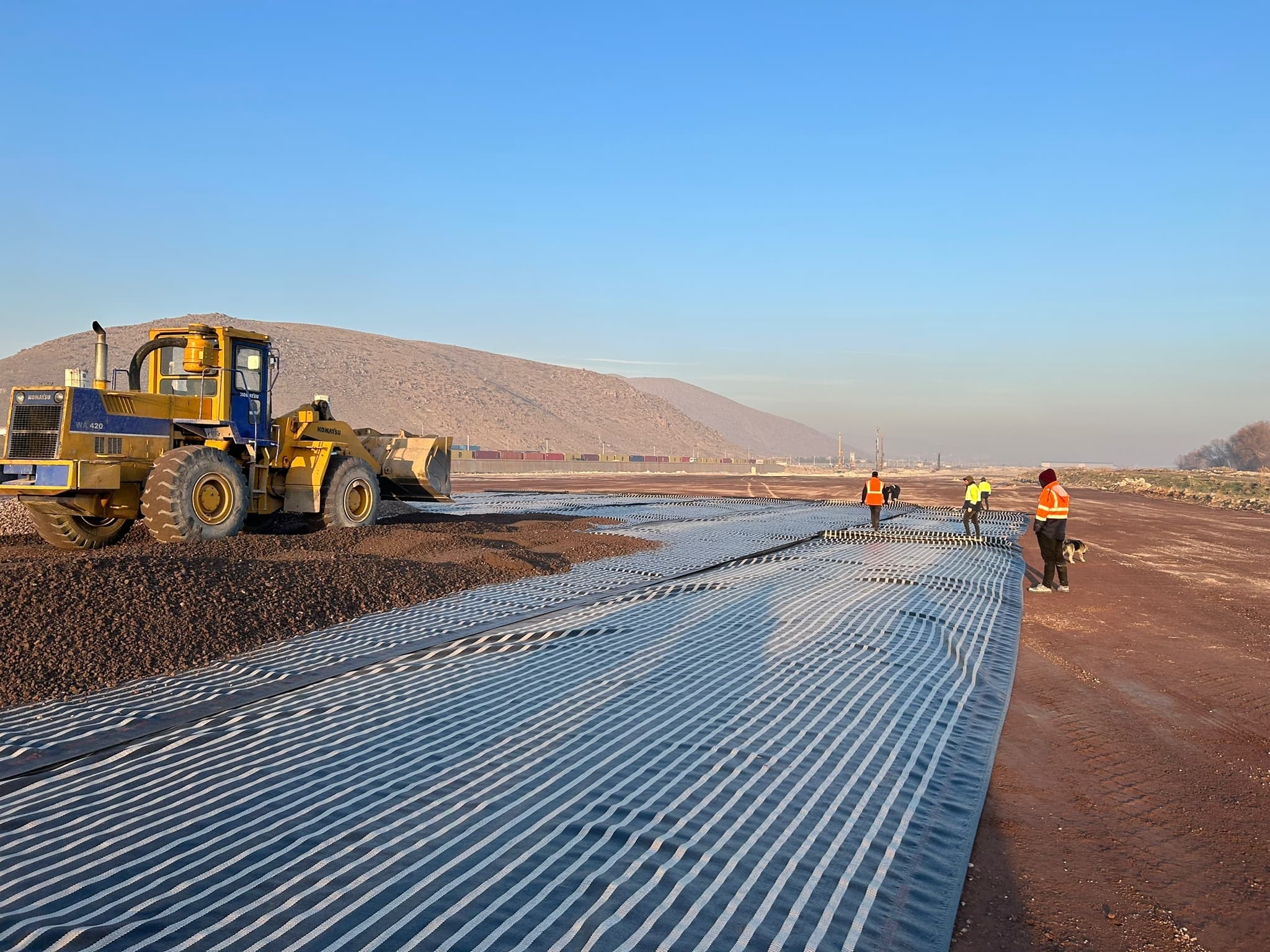
Explore more case studies
View allGEOTUBE Geobags used in coastal erosion control and protection project
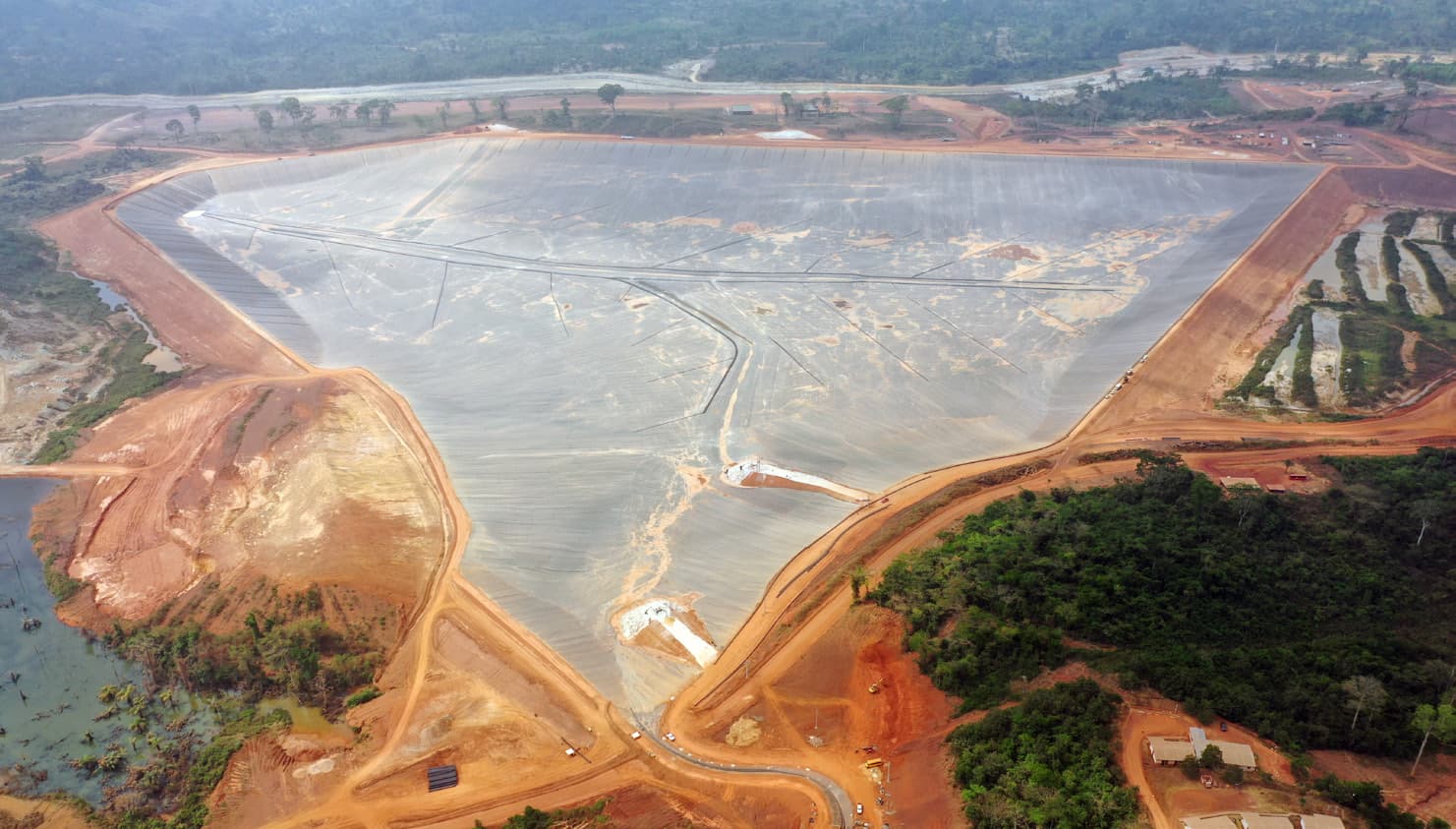
Robust geomembrane lining for ITY Gold Mine tailings storage facility
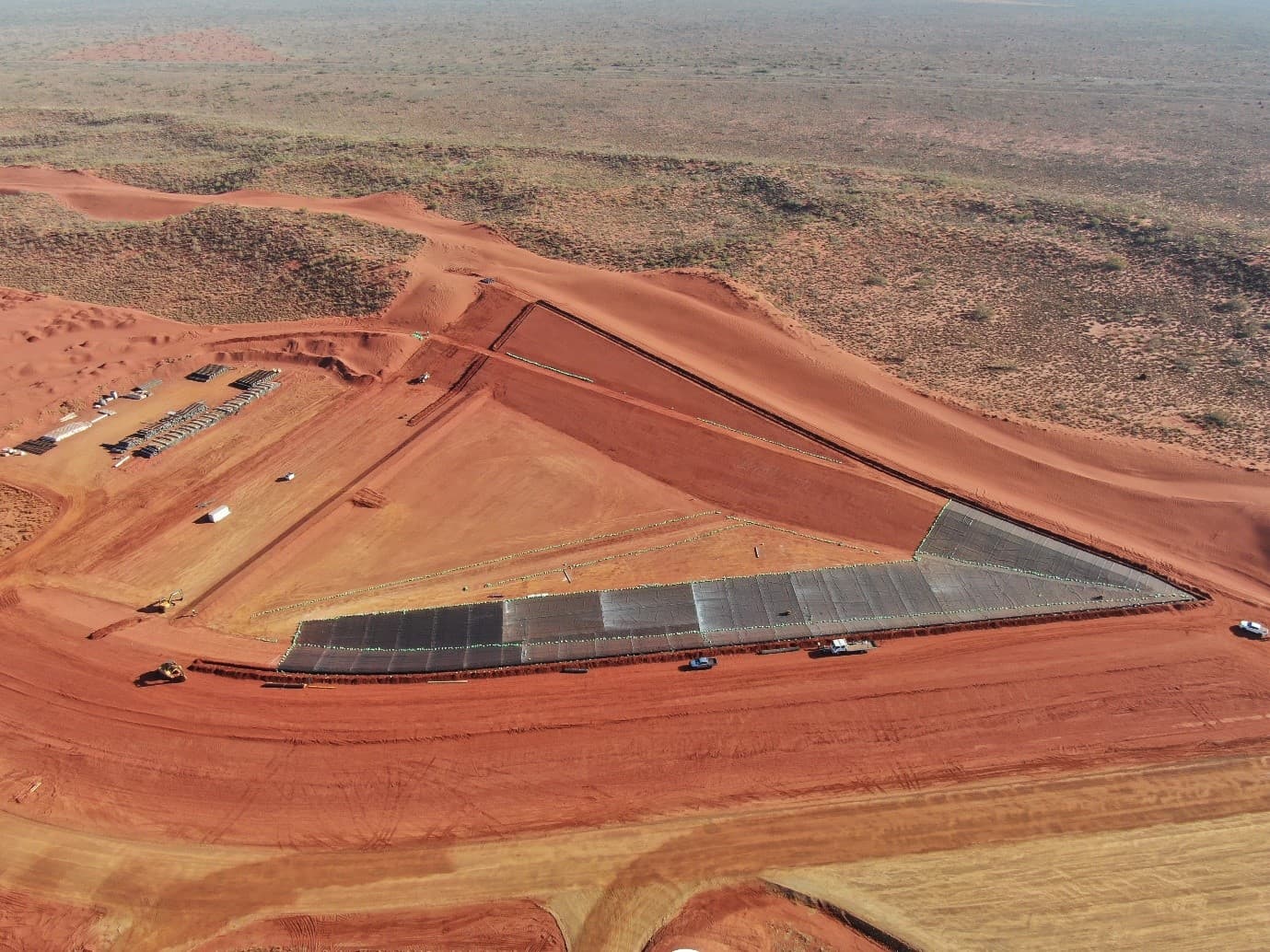
Improving waste management with GSE
To meet the growing needs of a rapidly expanding resources industry, Pilbara Regional Waste Managment used GSE geomembranes at their new waste management facility.