
Products
Industries
Addressing surface cracking on Queen Street, Yeppoon
Overview
Livingstone Shire Council, a key player in the transportation, waste, water, energy, mining, site development, and agriculture sectors, upgraded a section of Queen Street in Yeppoon. They undertook this project to address severe surface cracking caused by a soft and highly saturated subgrade.
After consulting their Pavements Engineer, the Council decided to use the new MIRAFI® H2Rx wicking geotextile. This innovative material provides not only separation, filtration and reinforcement functions, but also provides moisture management. The goal was to enhance the long-term performance of the pavement by efficiently drawing excess moisture and draining capillary water from the pavement structure. The project plan ensured uninterrupted access for local businesses and the nearby college, reflecting the Council's community-focused approach.
Challenge
The compromised Queen Street-subgrade, characterized by high saturation and low strength, caused persistent surface cracking. The installation process needed meticulous planning and execution.
First, the team removed the existing pavement from the site. They then prepared, graded, aligned, and compacted the subgrade to create a stable base. They excavated soft areas and replaced them with basecourse material to enhance structural integrity. Next, they installed roadside drains using Megaflo Flat Panel Pipe for efficient drainage.
The innovative MIRAFI H2Rx was laid on the prepared subgrade, lengthwise down the road, with a "tile" overlap of the rolls for seamless coverage. The side edges of the H2Rx were embedded into the trench for the Megaflo Pipe to create a direct drainage pathway, crucial for managing moisture levels and maintaining pavement stability.
Maintaining access to businesses and the college during construction posed a significant challenge. The team implemented a staged construction process, ensuring sections of the road always remained open, minimizing disruption.
This project marked the first use of the MIRAFI H2Rx in Australia, demonstrating the Council's commitment to adopting advanced solutions for infrastructure improvement. The successful completion of the project highlighted the H2Rx's effectiveness in managing both mechanical and moisture stabilization, ensuring a durable and resilient pavement.
Solution
Solmax provided their MIRAFI H2Rx, which delivered the essential functions of mechanical reinforcement and moisture management. The project used 3,600 m² of MIRAFI H2Rx, significantly enhancing the pavement's performance.
The Council selected MIRAFI H2Rx to trial its moisture management capabilities. The geotextile's wicking properties efficiently removed excess moisture, preventing surface cracking. Additionally, it provided essential separation and reinforcement functions, contributing to the pavement's stability and longevity.
The project highlighted the critical role of moisture management in pavement performance. The MIRAFI H2Rx improved trafficability and managed moisture levels, preventing subgrade saturation issues. This case study emphasizes the importance of selecting materials that address both mechanical and environmental challenges in road construction.
The implementation of MIRAFI H2Rx on Queen Street serves as an educational example for engineers and infrastructure planners. It underscores the need for innovative solutions that provide comprehensive benefits, ensuring long-term performance and sustainability of infrastructure projects. The local community, including the college and businesses, benefitted from improved road conditions, enhanced safety, and reduced maintenance requirements, illustrating the broader impact of adopting advanced geotextile solutions in civil engineering projects.
Building on our recent success, MIRAFI H2Rx has been upgraded to deliver superior moisture management performance for similar applications. This advanced enhancement includes added wicking loops with enhanced two-way wicking capabilities, ensuring optimal functionality and reliability.

The construction process was staged to ensure continuous access for businesses and the local college during the upgrade

Roadside drains were installed using Megaflo Flat Panel Pipe for effective drainage

Queen Street-s compromised subgrade, characterized by high saturation and softness, caused persistent surface cracking
Explore more case studies
View allMIRAFI geotextiles prevent subgrade failure and reduce track downtime
Canadian Pacific Railway (CP) identified track settlement issues and partnered with Solmax and Clifton Associates to implement a geosynthetic solution, reducing ballast use by 43% and completing repairs on a 72 ft section in under seven hours.
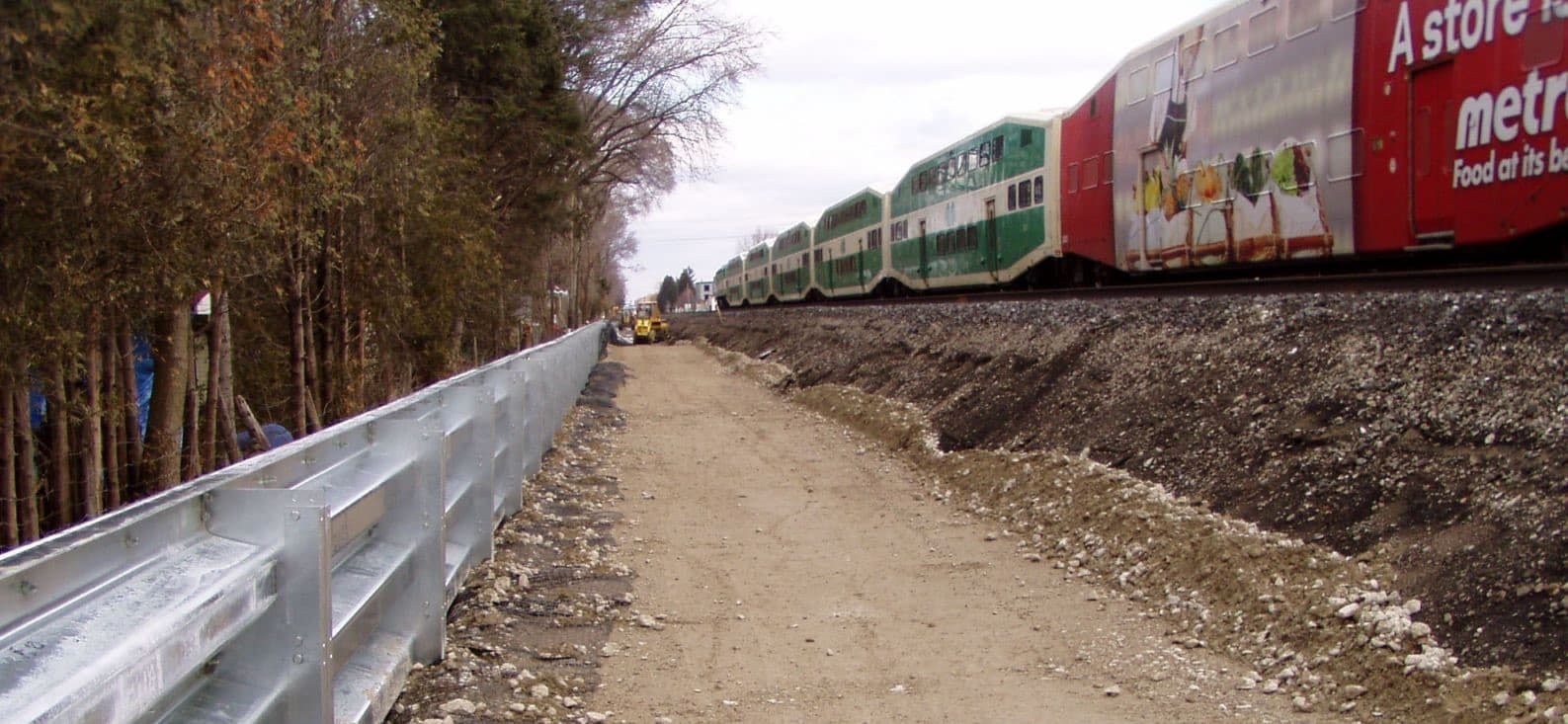
MSE walls with MIRAGRID XT for rail expansion
GO Transit used hybrid MSE walls with MIRAGRID XT geogrids to stabilize embankments on Lakeshore West Line, ensuring stability under space and load constraints.
Stabilizing soft clay soils and shallow utilities during the reconstruction of Main Street
Main Street in Palisade, CO, was reconstructed using geosynthetics to address soft soils and shallow utilities, reducing excavation and aggregate use.