Products
Industries
Advancements in sand island reclamation with GEOTUBE Marine technology
OVERVIEW
The Seri Tanjung Pinang Phase 2B (STP2B) project represents a major advancement in coastal reclamation technology and engineering. The primary objective, as defined by the client's needs, was the construction of an effective perimeter dyke around STP2B to significantly mitigate the occurrence of sediment plumes and prevent the loss of infilling sand material. This was pivotal not only for the structural integrity of the reclamation but also for the environmental sustainability of the surrounding marine areas.
CHALLENGE
One of the critical components in the execution of the STP2B project was the innovative use of GEOTUBE containers, essential for the construction of the perimeter dyke. The process entailed intricate and precise steps beginning with securing 50 m (54 ft) long GEOTUBE containers with triangular shaped end spreaders on a flat-bottom barge. These spreaders were carefully lowered onto the water surface using cranes, a crucial step requiring high precision to ensure the correct placement and orientation. Divers then connected slurry filling hoses to the GEOTUBE container inlet ports. The containers were subsequently lowered underwater to their designated locations, marking the beginning of the infilling process. This process was continuously monitored until the containers reached their designated height of 2.3 m (7.5 ft), after which the infilling was terminated, the slurry filling hose retrieved, and the inlet ports sealed by divers.
The project faced numerous challenges that tested the limits of traditional engineering solutions:
1. Environmental and temporal limitations: Given the sensitive nature of the marine environment, the project had limited windows each day to perform installations, dictated by variable weather conditions, tidal fluctuations, and strong underwater currents.
2. Precision requirements: The necessity for high accuracy in the placement of GEOTUBE containers was critical due to the need for stacking three layers of these containers accurately, a task compounded by the challenging underwater conditions.
To address these challenges, the project team ensured that all preparations were meticulously planned and executed. The use of advanced GPS technology facilitated precise positioning and tracking of GEOTUBE container placements, ensuring each was deployed accurately according to the project's stringent specifications.
The STP2B project demonstrated significant innovation in the GEOTUBE container installation method, which notably minimized required labor and enhanced overall construction safety. This systematic approach alleviated the uncertainties associated with deep-water GEOTUBE container filling and positioning, thus significantly lowering the barriers to their installation under challenging conditions. Moreover, the method boosted construction efficiency and safety, displaying a significant improvement over traditional method.
SOLUTION
The primary material used in the construction was the GEOTUBE Marine units. This product was selected for its exceptional properties, including high tensile strength and low elongation, which enabled the GEOTUBE Marine units to withstand the substantial forces exerted during the infilling process. These properties were crucial for reaching the required height of 2.3 m (7.5 ft) with a minimal area footprint while maintaining structural integrity under significant water depth pressures.
The GEOTUBE Marine units were selected due to their specially engineered woven fabric, which provided necessary strength and durability under the strenuous conditions of this project. The design of the GEOTUBE Marine units allowed for a reduced area footprint and effective containment of sediment, crucial for minimizing environmental impact and enhancing the efficiency of the reclamation process.
Alternative solutions were considered, but the GEOTUBE Marine units were chosen for its ability to meet stringent technical requirements and tight project timelines without compromising on quality or environmental safety.
This project highlighted several important lessons regarding the use of GEOTUBE Marine technology in coastal engineering:
Feasibility: Deep water GEOTUBE Marine technologycontainer construction was shown to be practical with careful design and execution planning, a critical insight for similar future projects.
Environmental impact: Monitoring data indicated a rapid reduction in total suspended solid levels post-infilling, confirming the GEOTUBE Marineunits’ effectiveness in environmental protection and compliance with sustainability goals*.
By integrating advanced GEOTUBE Marine technology with meticulous project planning and execution, the initiative successfully addressed the complex challenges posed by environmental conditions and logistical constraints. The strategic application of this technology not only preserved the ecological balance of the surrounding marine areas but also enhanced the structural integrity and longevity of the reclamation site, providing significant cost efficiencies and environmental benefits. This project serves as an example for engineers and project managers worldwide, illustrating the effectiveness of embracing advanced technologies in modern engineering projects.
* Chew, S. H., Soh, J. M., Lim, L. K., Tan, J. Y., Siew, K. H., & Ang, C. P. (2023). Installation of geotextile tubes as perimeter bund in mega-reclamation project at Penang, Malaysia. Presented at the Geosynthetics Conference 2023, Advanced Textiles Association, 433
Explore more case studies
View allMIRAFI geotextiles prevent subgrade failure and reduce track downtime
Canadian Pacific Railway (CP) identified track settlement issues and partnered with Solmax and Clifton Associates to implement a geosynthetic solution, reducing ballast use by 43% and completing repairs on a 72 ft section in under seven hours.
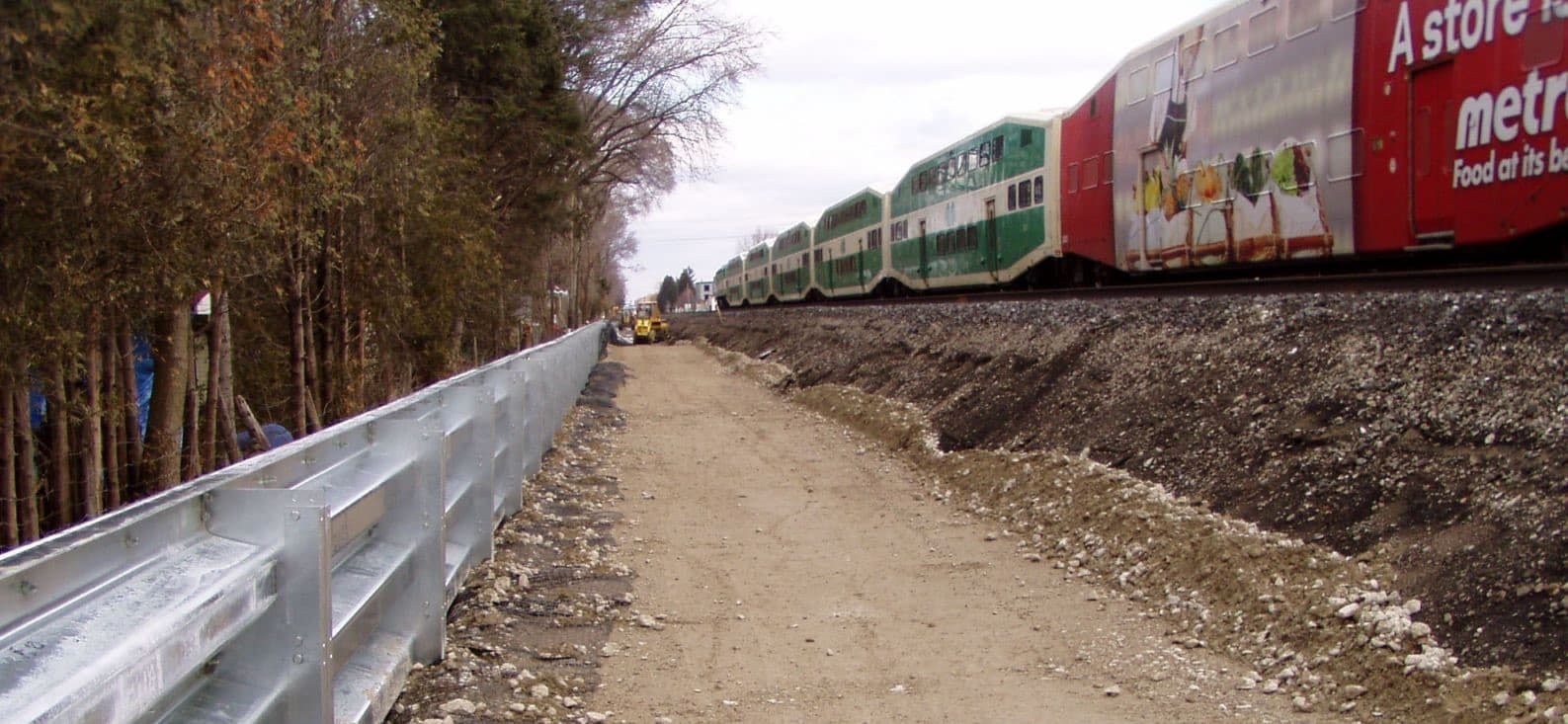
MSE walls with MIRAGRID XT for rail expansion
GO Transit used hybrid MSE walls with MIRAGRID XT geogrids to stabilize embankments on Lakeshore West Line, ensuring stability under space and load constraints.
Stabilizing soft clay soils and shallow utilities during the reconstruction of Main Street
Main Street in Palisade, CO, was reconstructed using geosynthetics to address soft soils and shallow utilities, reducing excavation and aggregate use.