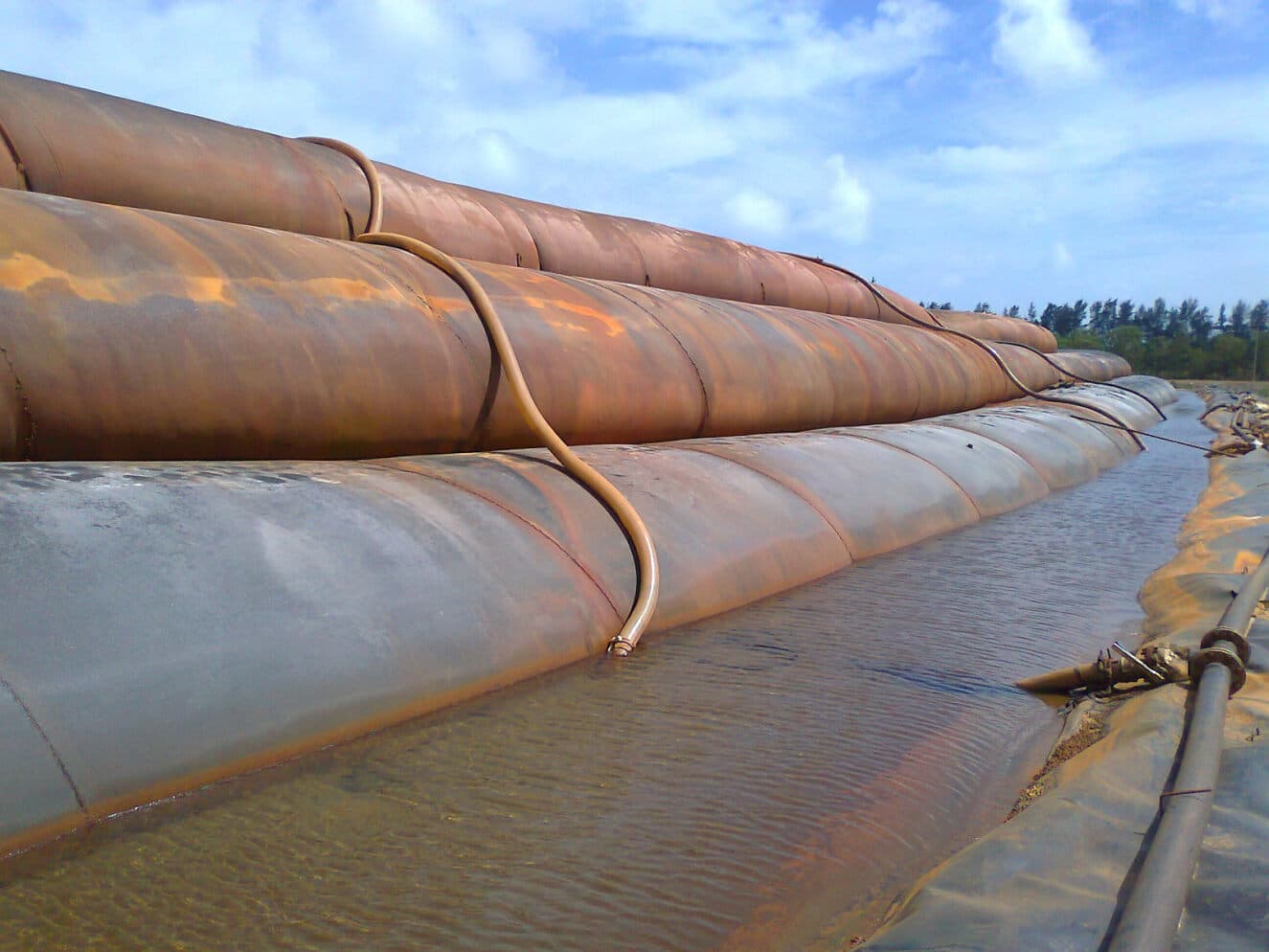
Products
Industries
GEOTUBE dewatering and containment of gypsum wastes at a titanium dioxide plant
Overview
Industrial waste, often in slurry form and containing contaminants, needs to be managed and disposed of properly to protect the environment. This case study focuses on the dewatering of gypsum waste slurry at a titanium pigment plant in Malaysia using geotextile tubes. The plant produces titanium pigments through a process that involves treating ilmenite with sulfuric acid, resulting in the discharge of red gypsum waste in slurry form with a solid concentration of approximately 16%. Initially, the waste was treated using filter presses.
Challenge
The plant faced capacity and storage issues as the filter presses were operating at maximum capacity, and the sludge lagoons were full. The high cost of adding more filter presses and the low return on investment led the plant to seek more affordable dewatering alternatives.
Solution
To address the problem, the client explored the option of installing GEOTUBE® dewatering units suggested by specialist engineers from Solmax as part of an integrated plant processing solution.
A Rapid Dewatering Test (RDT) or Jar Test was conducted to determine the appropriate polymer type and dosage needed to flocculate the sludge. The results confirmed the correct dosage and the effectiveness of GEOTUBE GT500D fabrics in containing and dewatering the red gypsum slurry. The discharge produced visually clear and high-quality effluent. The results were further validated through a GEOTUBE Dewatering Test or Pillow Bag test. Additionally, a full-scale pilot tube was utilized, employing GEOTUBE GT500D fabric with dimensions of 8.8 m (29 ft) circumference and 27.5 m (90 ft) length. This pilot confirmed a 39% dewatered solids concentration and identified operational implications and actual solid volumes within the tube.
Over the course of a year, more than 100 units of GEOTUBE dewatering tubes, with dimensions of 36.6 m (120 ft)1 circumference and lengths ranging from 57 m (187 ft) to 43.8 m (143 ft), were installed as part of an integrated plant waste capture program. These tubes captured a total of 180,000 m³ (235,710 yd³) of dry solids. The use of GEOTUBE dewatering tubes resulted in cost savings in terms of capital expenditure and reduced overall maintenance and operational costs.
Before deployment, the positions of the GEOTUBE units were marked on the geomembrane liner. Each unit, weighing approximately 1.3 tons (2,866 pounds), was lifted and positioned using a mobile crane. The units were then manually unrolled and unfolded by operators or with the assistance of a mechanical winch attached to a 4WD vehicle. A 100 mm (3.9 in) diameter flexible hose was used to connect the slurry main pipe to the GEOTUBE dewatering units. The filling ports of each unit were connected with flexible hoses, and the slurry inflow for each port was regulated by a gate valve installed between the main slurry pipe and the flexible hose.
Result
GEOTUBE dewatering technology increased the plant's dewatering capacity by approximately 25%, allowing it to meet the sudden surge in demand for titanium dioxide. Furthermore, the plant was able to conduct a complete maintenance overhaul of their aging mechanical dewatering equipment without disrupting production.
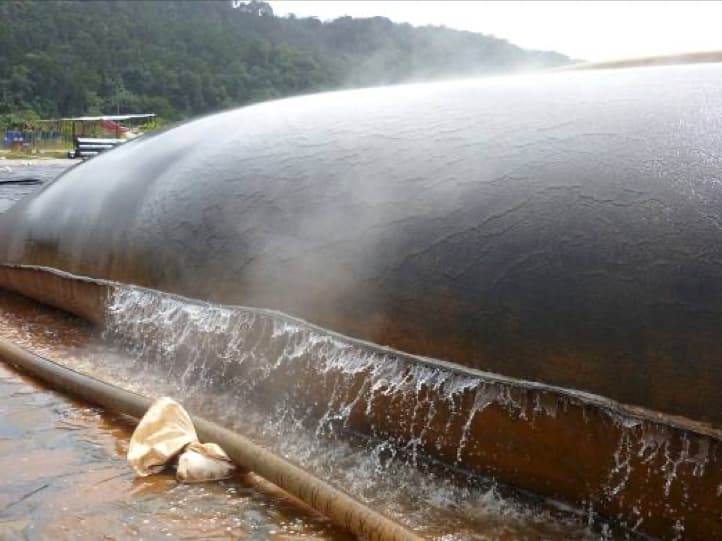
Titanium Dioxide Plant Terengganu Waste management GEOTUBE
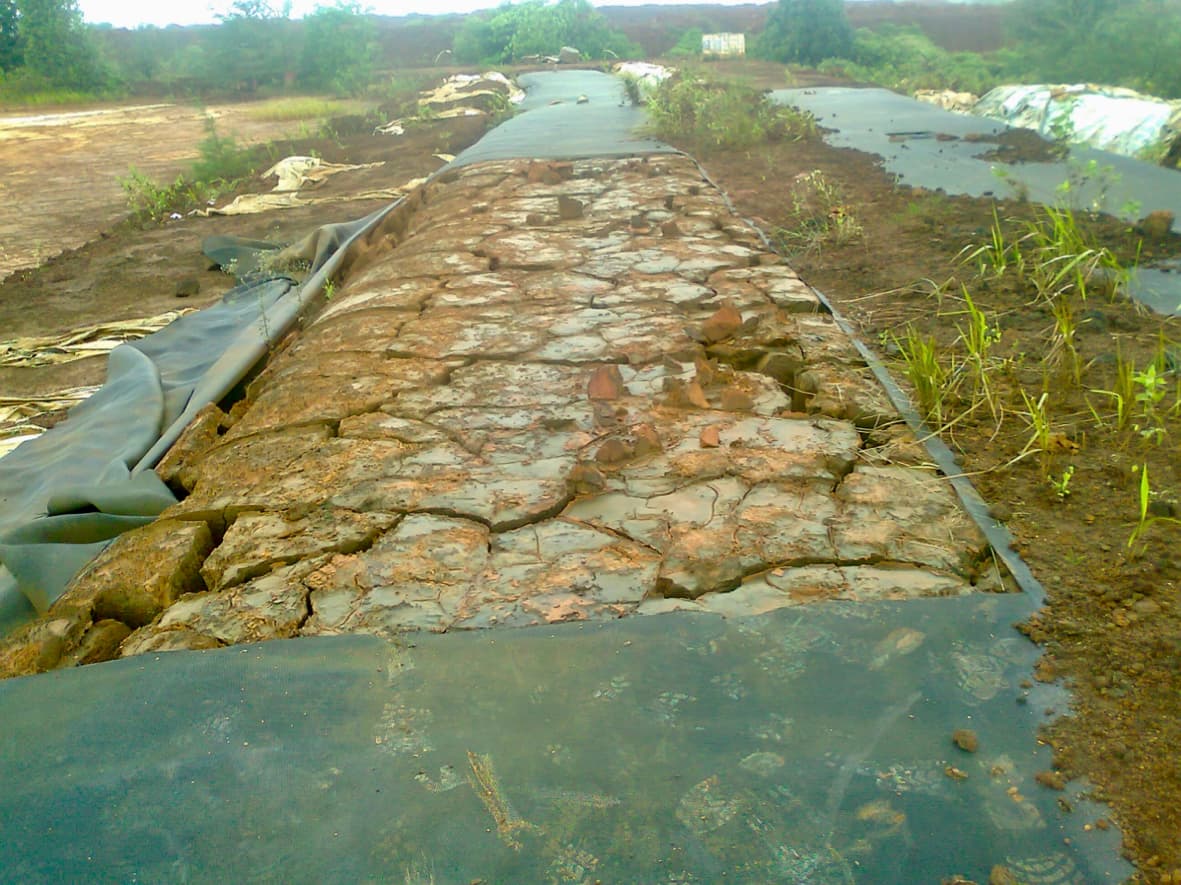
Titanium Dioxide Plant Terengganu Waste management GEOTUBE
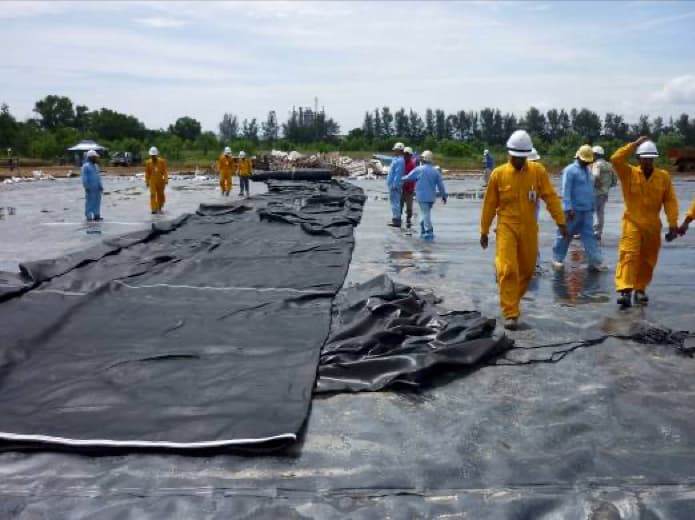
Titanium Dioxide Plant Terengganu Waste management GEOTUBE

Titanium Dioxide Plant Terengganu Waste management GEOTUBE
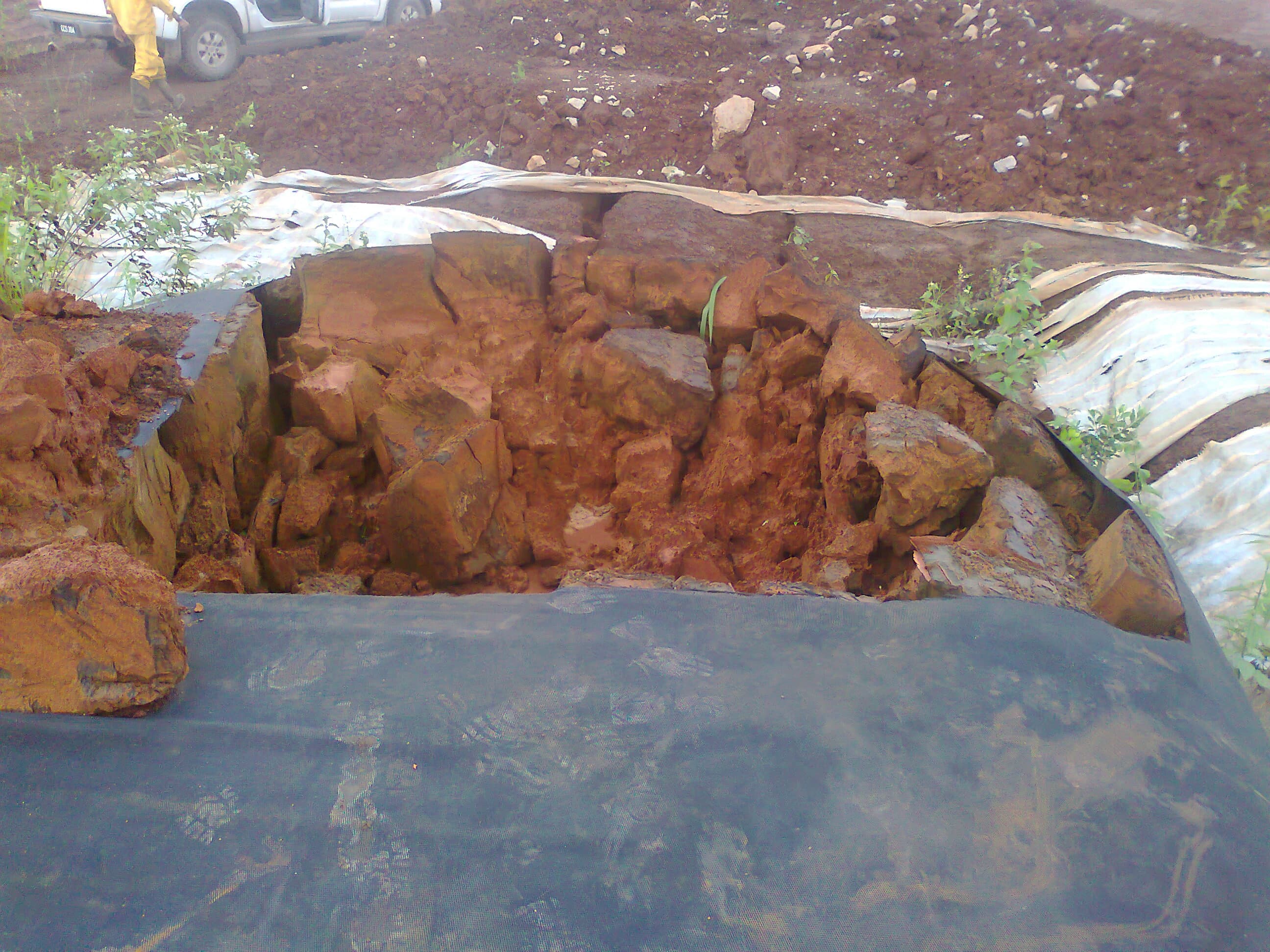
Titanium Dioxide Plant Terengganu Waste management GEOTUBE
Explore more case studies
View allMIRAFI geotextiles prevent subgrade failure and reduce track downtime
Canadian Pacific Railway (CP) identified track settlement issues and partnered with Solmax and Clifton Associates to implement a geosynthetic solution, reducing ballast use by 43% and completing repairs on a 72 ft section in under seven hours.
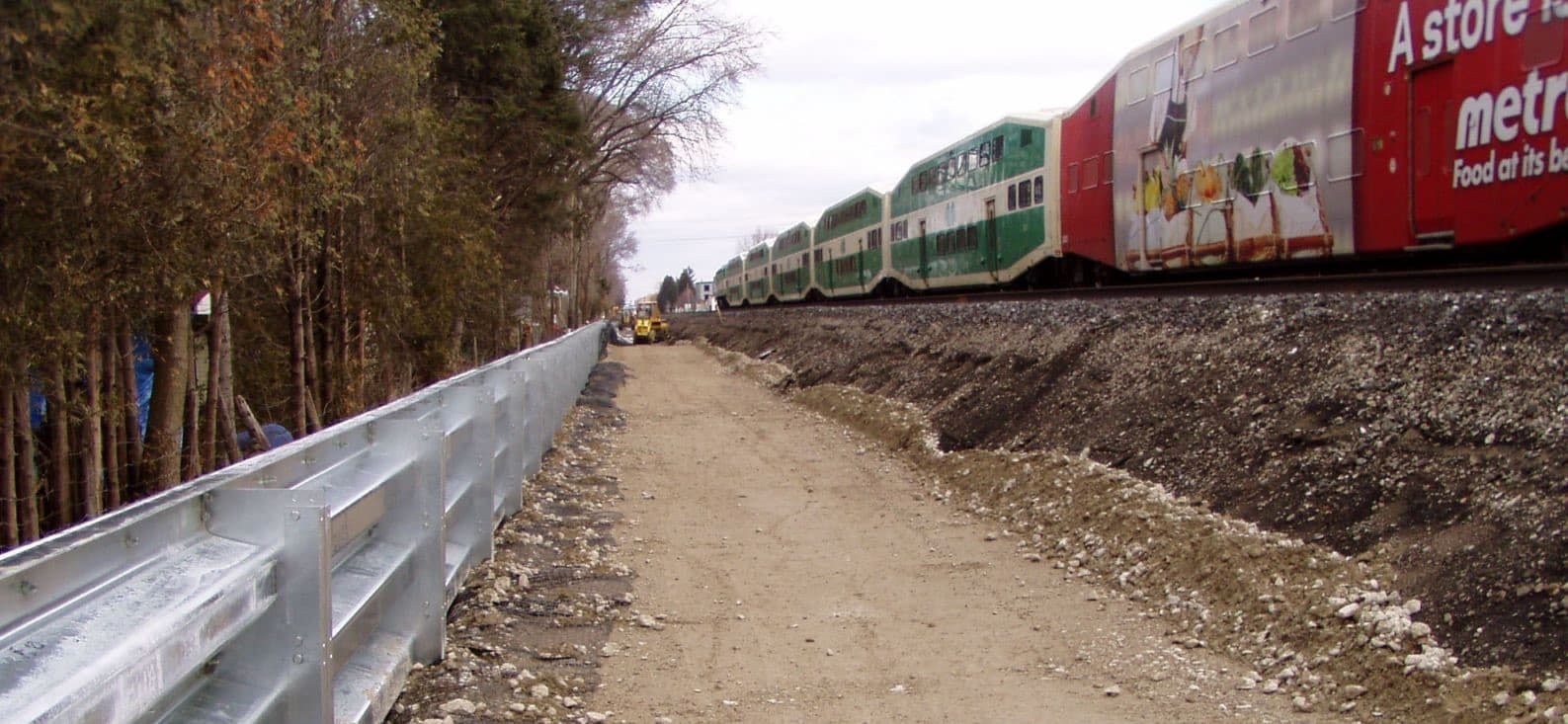
MSE walls with MIRAGRID XT for rail expansion
GO Transit used hybrid MSE walls with MIRAGRID XT geogrids to stabilize embankments on Lakeshore West Line, ensuring stability under space and load constraints.
Stabilizing soft clay soils and shallow utilities during the reconstruction of Main Street
Main Street in Palisade, CO, was reconstructed using geosynthetics to address soft soils and shallow utilities, reducing excavation and aggregate use.