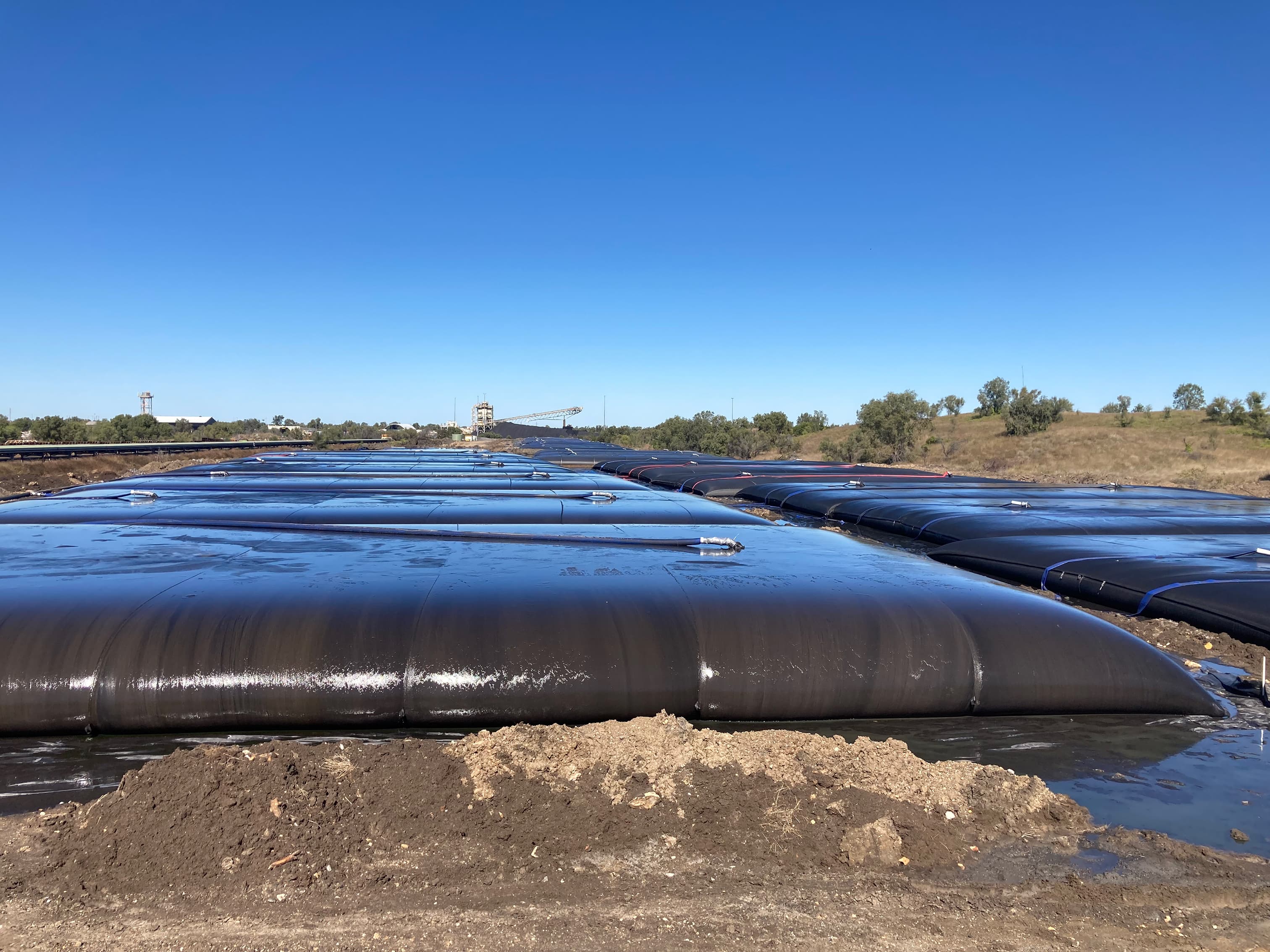
Products
Industries
Silt trap dewatering for Kestrel Coal Mine
Overview
Kestrel Coal Resources, an underground coking coal mine located in Emerald, Queensland, is one of Australia's most significant coal producers. The mine produces high-quality coking coal for steelmaking, contributing to both the Australian and global economies.
In 2022, the mine faced a major operational challenge: two HDPE-lined silt traps, positioned upstream of a holding pond, had reached full capacity with silt. This excess sediment, primarily coal fines, risked spilling into the holding pond, disrupting operations and reducing water treatment capacity.
To resolve this issue, Kestrel Coal Resources sought a solution that would effectively clean the silt traps while ensuring minimal environmental impact while also preserving the recovered coal fines for potential sale.
Maxitool, a well-established and respected north Queensland based dewatering and dredging solutions company was tasked with undertaking the project. Collaborating closely with Solmax, a viable and functional GEOTUBE® solution was developed and executed.
Challenge
The primary challenge of this project involved the removal and dewatering of approximately 40,000 m³ of silt from two HDPE-lined silt traps. The silt, primarily comprising coal fines washed off an adjacent stockpile. The client needed a solution that would not only restore the silt traps' capacity but also prevent the sediment from reaching the holding pond, where further contamination could occur.
The project had several complicating factors. Both silt traps were completely full and contained no water making dredging more difficult and the long, narrow aspect ratio of the ponds further complicated the dredging process.
Another technical challenge was a variation in particle size of the entrapped fines throughout the length of the silt traps with settlement at the inflow head of the ponds comprising larger sized particles and the lower end finer more densely compacted material. This variation in fines composition required the use of flocculants to enhance the dewatering performance.
Solution
Maxitool and Solmax collaborated to design a custom solution that facilitated the sophisticated Maxitool dredger to operate at optimum capacity to capture and dewater the slurry pumped into the GEOTUBE units.
To capture the slurry required to be dewatered a total of 41 GEOTUBE units, comprising 39 GEOTUBE GT500 366/306 units and two GEOTUBE GT500 366/174 units were deployed across the site.
The first step in the installation process involved preparing the ground with dozers and graders to ensure a stable subgrade. Wheel rolling was used to compact the subgrade, and builder’s plastic was placed around the perimeter of the area to catch runoff. The runoff was then directed into a dirty water drain that led back to the holding pond, ensuring a closed-loop water reticulation system that ensured no water released from the tubes contaminated the environment.
Once the subgrade was prepared, the tubes were laid out in sections, with valves and manifolds installed to manage the flow between the GEOTUBE units. The dredging operation was initiated using a 1,000 m pipeline with a booster pump to feed the material into the GEOTUBE units.
Pumping of the tubes was phased with three tubes online, three on standby, and three being prepared for the next section. This use of multiple tubes facilitated a continuous dredging operation, minimizing downtime and ensuring that the project remained on schedule.
The dewatering process initially progressed smoothly, as the coarse material at the beginning of the silt trap dewatered effectively without the use of flocculants. However, as the dredged particle size became finer it was necessary to inject polymer flocculant into the feed lines prior to slurry entering the tubes to enhance dewatering efficiency. This adaptability allowed the project to continue without significant delays.
As on any mine site, safety was a top priority throughout the project, especially given the hot weather conditions. The team implemented strict heat stress controls to protect workers, including frequent breaks, hydration stations, and rotating shifts to prevent exhaustion during the labor-intensive process of laying out the geotextile tubes.
Results
Over the course of the 22-week project, a total of 41 GEOTUBE units were successfully completed, restoring over 95% of the silt traps’ capacity. The dredging operation efficiently removed the silt without damage to the pond lining system. The recovered and dewatered coal fines retained within the tubes were subsequently removed, re-washed and blended into a saleable product allowing the mine to recover the cost of dewatering the ponds without any impact on mine operations.
Several lessons were learned throughout the course of this project. First, the use of larger, customized GEOTUBE units improved efficiency by reducing the labor required and time required to lay out multiple tubes. Additionally, the team recognized that working night shifts could mitigate some of the challenges posed by the hot weather, particularly during the most labor-intensive stages of the project.
Another key takeaway was the importance of flexibility in material selection. The project initially progressed well without the use of flocculants, but as the particle size became finer, flocculants were necessary to maintain dewatering efficiency. This adaptability helped the team overcome the varying conditions within the silt traps.
The successful execution of the work resulted in a follow-up dredging project at an adjoining mine, which extended the collaboration between Maxitool, Solmax, and Kestrel Coal Resources for an additional thirteen months.
Conclusion
The successful completion of this project demonstrated the value of collaboration between material supplier and dredging and dewatering specialists to resolve numerous technical and operational challenges that dewatering mine and mineral slurries present.
In mine and mineral dewatering works delivery of GEOTUBE units with the structure and properties capable of dewatering the slurry composition is important. It is also important that the GEOTUBE units can safely capture the flow volumes delivered by the dredge or pumps operating at maximum capacity.
By restoring the capacity of the silt traps and recovering valuable coal fines, Kestrel Coal Resources was able to improve the operational efficiency of their mine and avoid environmental contamination.
This project serves as a model for future silt trap dewatering efforts in the mining industry, showcasing the importance of tailored solutions, adaptability, and careful planning in achieving successful outcomes.

The primary challenge of this project involved the removal and dewatering of approximately 40,000 m³ of silt from two HDPE-lined silt traps

GEOTUBE units were filled and placed strategically to restore 95% of the silt trap’s capacity, preventing sediment overflow into the holding pond.
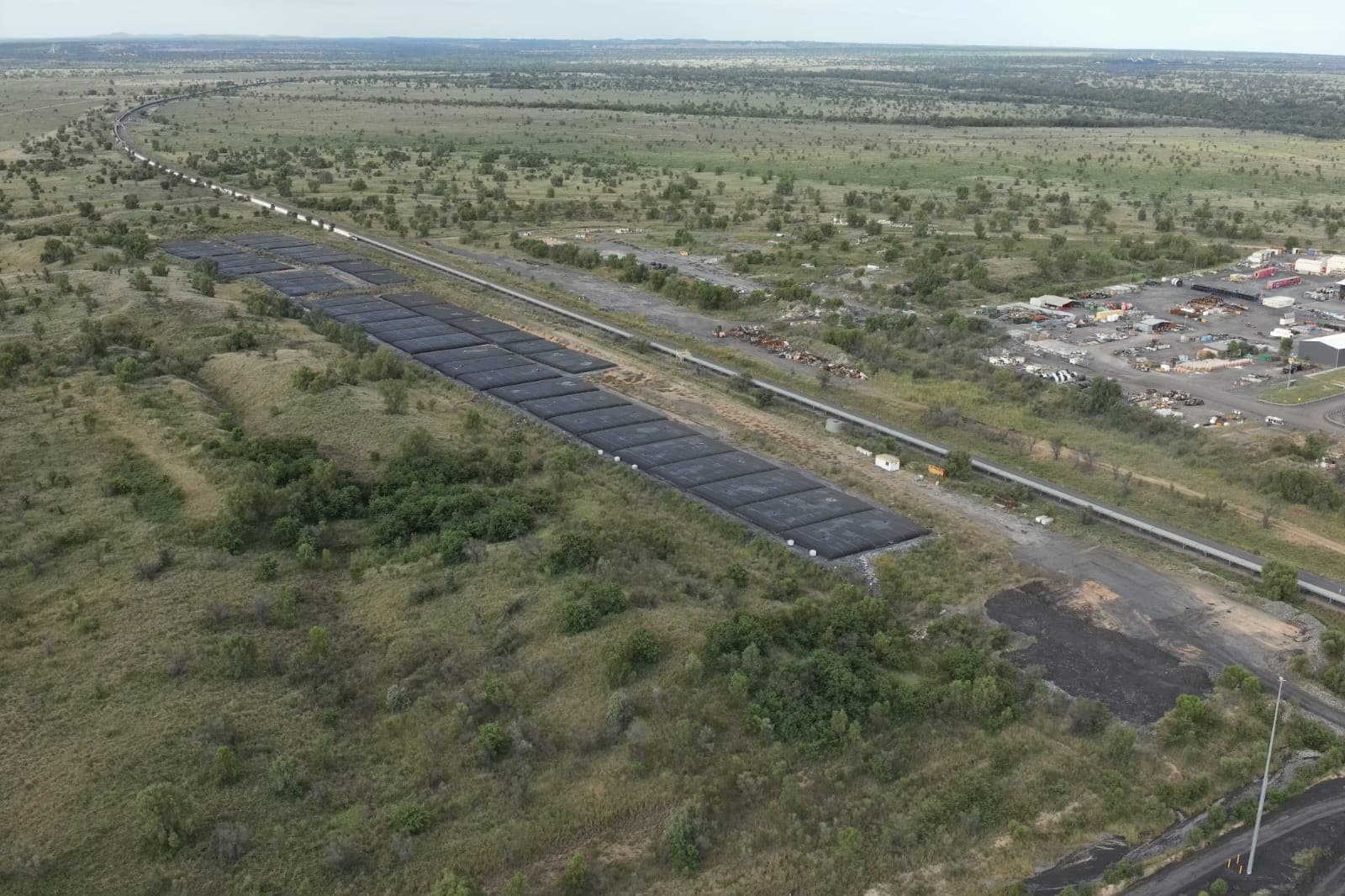
A 1,000 m pipeline with a booster pump fed dredged material into GEOTUBE units, enabling effective dewatering of coal fines from the silt traps

The dredging operation was initiated using a 1,000 m pipeline with a booster pump to feed the material into the GEOTUBE units.
Explore more case studies
View allMIRAFI geotextiles prevent subgrade failure and reduce track downtime
Canadian Pacific Railway (CP) identified track settlement issues and partnered with Solmax and Clifton Associates to implement a geosynthetic solution, reducing ballast use by 43% and completing repairs on a 72 ft section in under seven hours.
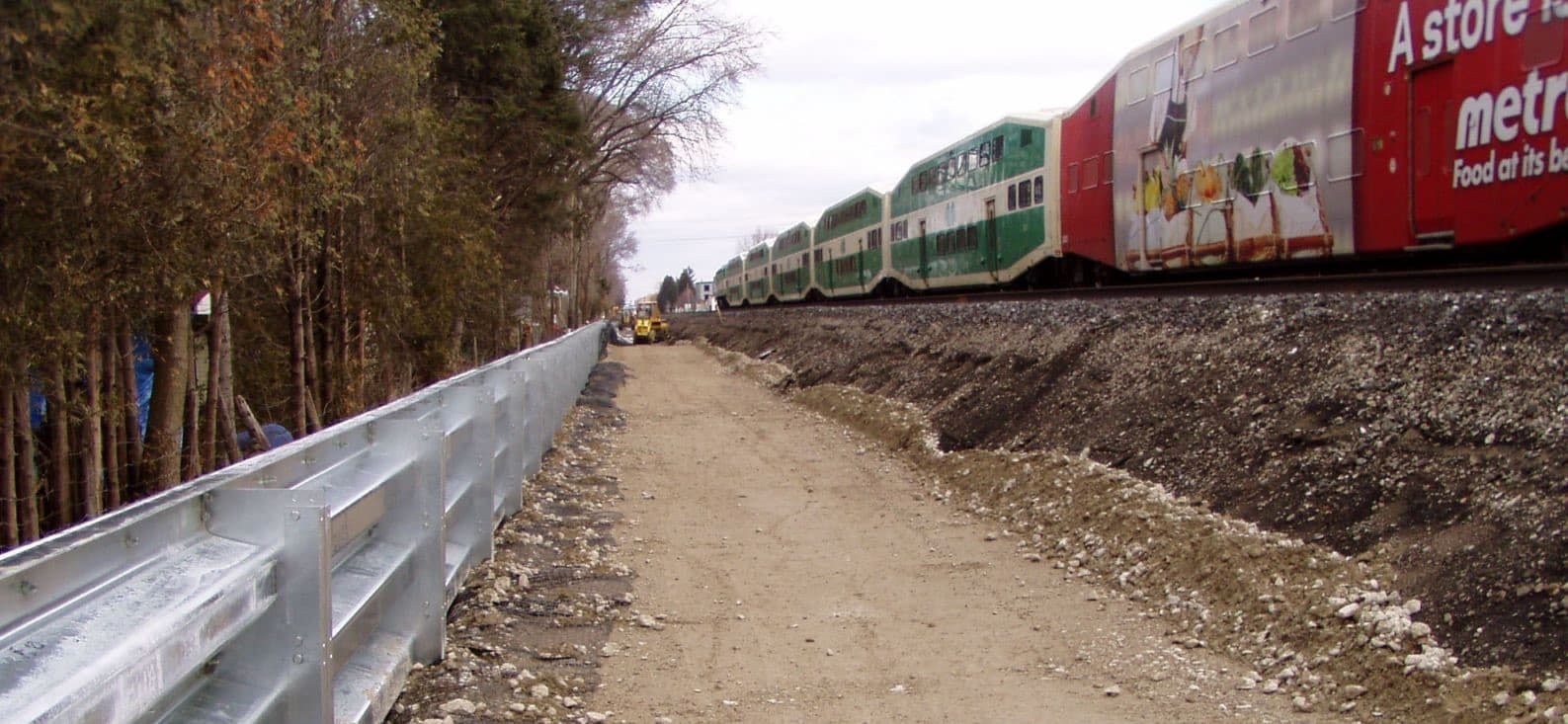
MSE walls with MIRAGRID XT for rail expansion
GO Transit used hybrid MSE walls with MIRAGRID XT geogrids to stabilize embankments on Lakeshore West Line, ensuring stability under space and load constraints.
Stabilizing soft clay soils and shallow utilities during the reconstruction of Main Street
Main Street in Palisade, CO, was reconstructed using geosynthetics to address soft soils and shallow utilities, reducing excavation and aggregate use.