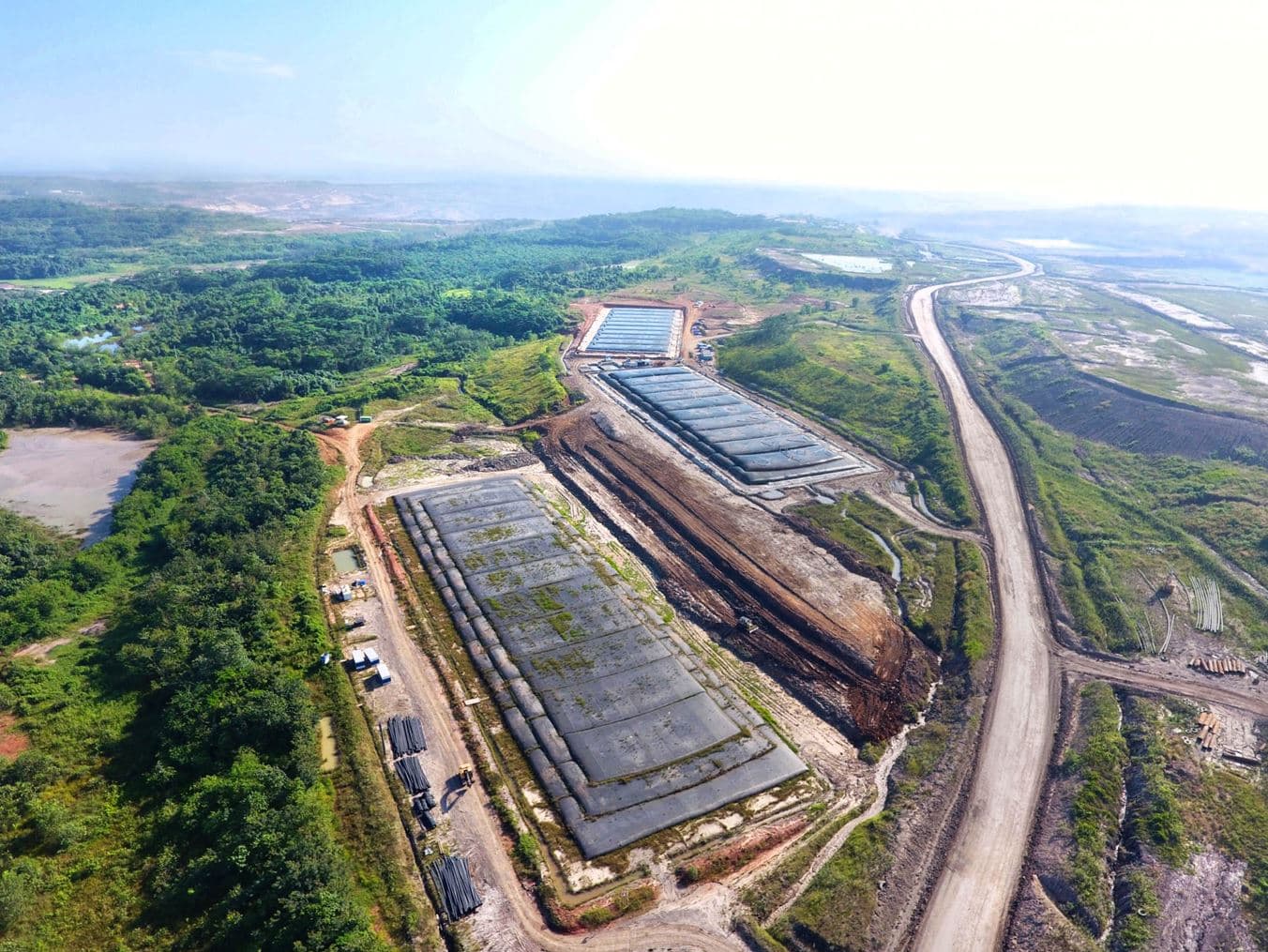
GEOTUBE systems come of age for mining and mineral process waste
In recent years, the adoption of GEOTUBE® systems for dewatering mineral waste and mine water management has surged. What's driving this rise, and how effective are these systems with complex slurries? We'll delve into four primary reasons:
#1. High volume capacity
Past perception
Traditionally, GEOTUBE systems were seen as suitable for dewatering smaller waste volumes, as the costs of conventional dewatering methods for such volumes were high. This gave rise to the perception that they weren’t fit for large-scale operations.
Market dynamics
This restricted use was influenced by local market dynamics. Local specialists often sought low-cost geotextile tubes without assessing other factors that could increase productivity and cut costs.
Efficiency for larger projects
While suitable for smaller projects, this approach doesn't work for large-scale dewatering, which requires bigger tubes with more solids retention. now produces GEOTUBE units that exceed 3,000m³ capacity. By assessing each project individually, provides tailored solutions for higher slurry flows with a reduced footprint.
Benefits of high capacity tubes
Large capacity tubes offer innovative methods like reprocessing mineral-rich tailings. Efficiently dewatered GEOTUBE systems can reduce the need for new storage facilities, simplify closure processes, and offer financial benefits, especially during low ore prices.
#2. Application versatility
Unparalleled flexibility
GEOTUBE systems range from small units holding one m³ of solids to massive containers holding over 3,000m³. This adaptability comes from investments in fabric design, catering to a wide variety of slurry types.
Innovative designs
Their versatility has led to designs that better manage tailings slurry flow or act as internal barriers for tailings flow. GEOTUBE systems are also used as filters to manage water contaminants and in conjunction with traditional equipment to maintain production during unexpected surges or maintenance.
#3. Cost effectiveness
Cost analysis
Mining companies typically compare dewatering options based on cost per m³ retained solids. Every project, being unique, requires a distinct assessment.
GEOTUBE vs. Mechanical plants
While mechanical plants are costly, GEOTUBE units are cost-effective but need skillful handling. Comparing geotextile tubes from different suppliers can be challenging, but GEOTUBE units are recognized for their superior dry cake volume capacity.
Polymer costs
Beyond tube costs and manpower, polymer dosing is a factor. Flocculants or coagulants may be necessary, depending on the slurry type. GEOTUBE systems generally require a polymer dose of 1-3 kg per metric tons dried solids (MTDS).
Economic fluctuations
Over the past few years, GEOTUBE dewatering units have offered solutions regardless of ore price fluctuations. They supplement output during high demand and serve as low-cost alternatives when ore prices dip.