Conquering extreme conditions with a high-temperature liner solution
Overview
The southern part of the Canadian province of Saskatchewan experienced a significant boost to its local economy with the construction of the first new potash mine in the region in over 40 years. This mine holds great importance for both the economic development of the region and the global business strategy of its owner.
As part of the solution mining process, the site was equipped with a series of brine ponds and oil separation ponds to serve as the primary containment for heated liquids. Given the chemical constituents present in the mining solutions, it was crucial that the liner could withstand degradation from brine, used oil, diesel, distillate, and ultraviolet exposure. Additionally, during the 25-year service life of the ponds, fluid temperatures were expected to fluctuate between extreme highs and lows, reaching up to 83 C (181 F) in storage facilities and dropping to -20 C (-4 F) or below in the typical Canadian plains climate. Environmental stewardship was a critical success factor from the owner's perspective, and any liner unable to maintain its integrity against both the chemicals and elevated temperatures of stored liquids would be deemed unacceptable.
Solmax collaborated with the project design team to find a pond liner that would meet all these criteria. Everyone agreed that HDPE geomembrane would protect well against the chemical components of the brine; however, concerns arose about the ability of industry-standard liners to withstand elevated temperatures. Solmax recommended GSE® HDH, a high-density polyethylene geomembrane specially formulated to maintain its properties in sustained elevated temperatures of up to 100 C (212 F).
The construction schedule was extremely tight, with installation commencing in September 2014 and concluding before winter's end. Solmax managed to supply GSE HDH with just one month's notice. Unforeseen site conditions, such as a high groundwater table and slow progress due to frozen ground, led to delays and required Solmax to deliver the liner to the site within a very specific construction window. To keep the installation crew on schedule, Solmax provided truckload shipments and began production for the remaining ponds as the GSE HDH liner was being deployed and welded. Like all high-density polyethylene geomembranes, GSE HDH was successfully welded even in cold weather, a challenging task with alternative high-temperature grade geomembrane materials.
Challenge
The challenges faced in this project were:
Extreme temperature variations: Fluid temperatures within the ponds could range from soaring highs of up to 83 C (181 F) in storage facilities to plummeting lows of -20 C (-4 F) or below in the harsh Canadian plains climate.
Chemical exposure: The liner needed to withstand degradation caused by exposure to brine, used oil, diesel, distillate, and ultraviolet radiation.
Environmental stewardship: The project owner prioritized environmental responsibility, demanding a liner that could maintain its integrity against both chemical exposure and elevated temperatures.
Solution
Solmax provided an effective solution to address the challenges faced during the construction of the potash mine's solution ponds:
GSE HDH: Solmax recommended the use of GSE HDH, a specially formulated high-density polyethylene geomembrane capable of maintaining its properties in sustained elevated temperatures of up to 100 C (212 F).
Timely supply: Despite a tight construction schedule, Solmax managed to supply the GSE HDH liner with only one month's notice, ensuring the project remained on track.
Adaptation to site conditions: Unforeseen site conditions, such as a high groundwater table and frozen ground, were successfully managed by Solmax, allowing for the liner's deployment and welding to proceed as planned.
Successful welding in cold weather: GSE HDH demonstrated its versatility by being effectively welded in cold weather, a task that can be challenging with alternative high-temperature grade geomembrane materials.
In total, eight solution ponds were constructed and lined with nearly 65,000 m² (700,000 ft²) of 80 mil (2.032 mm) thick geomembrane. The GSE HDH liner was installed over a 340.2 g (12 oz) nonwoven geotextile cushion to create a reliable liner system.
Two of the well pads have been in service and receiving hot brine liquid above 70 C (158 F). Both the construction manager and geomembrane installer noted how easily the GSE HDH was installed, even during the harsh Canadian winter.
Explore more case studies
View all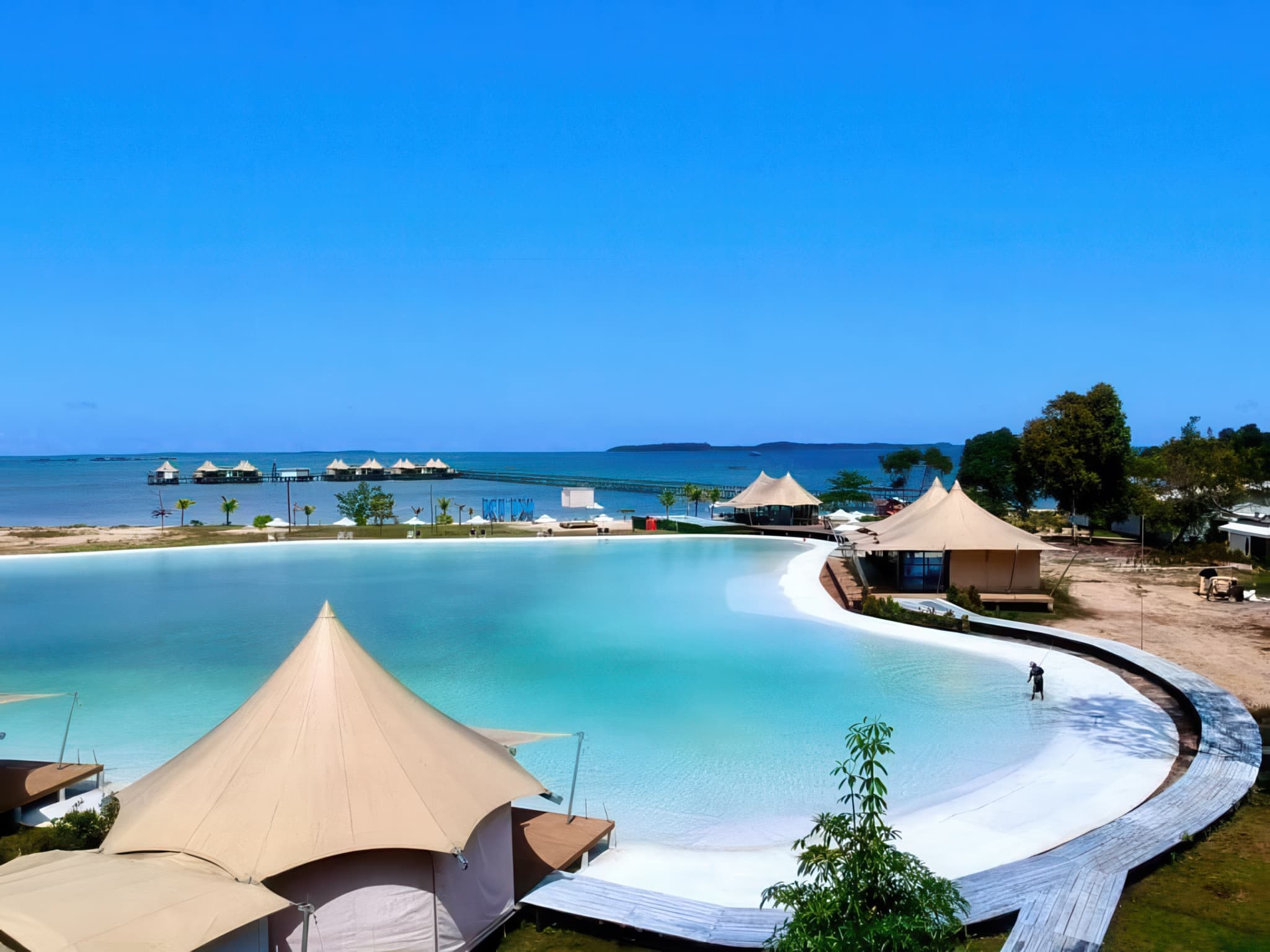
Creating a recreational pond with GSE geomembrane at Kiki Beach Resort
Kiki Beach Resort on Batam Island installed GSE HD 1.50 mm White Smooth for a recreational pond to enhance visual appeal and durability. The solution included custom roll sizes and a GSE Polylock anchoring system to meet design and site challenges.
Restoration of submerged stormwater pipeline
Desilting Solutions restored a submerged stormwater pipeline in Milton, Queensland, to 97% capacity using GEOTUBE technology and remote dredging within a confined site.
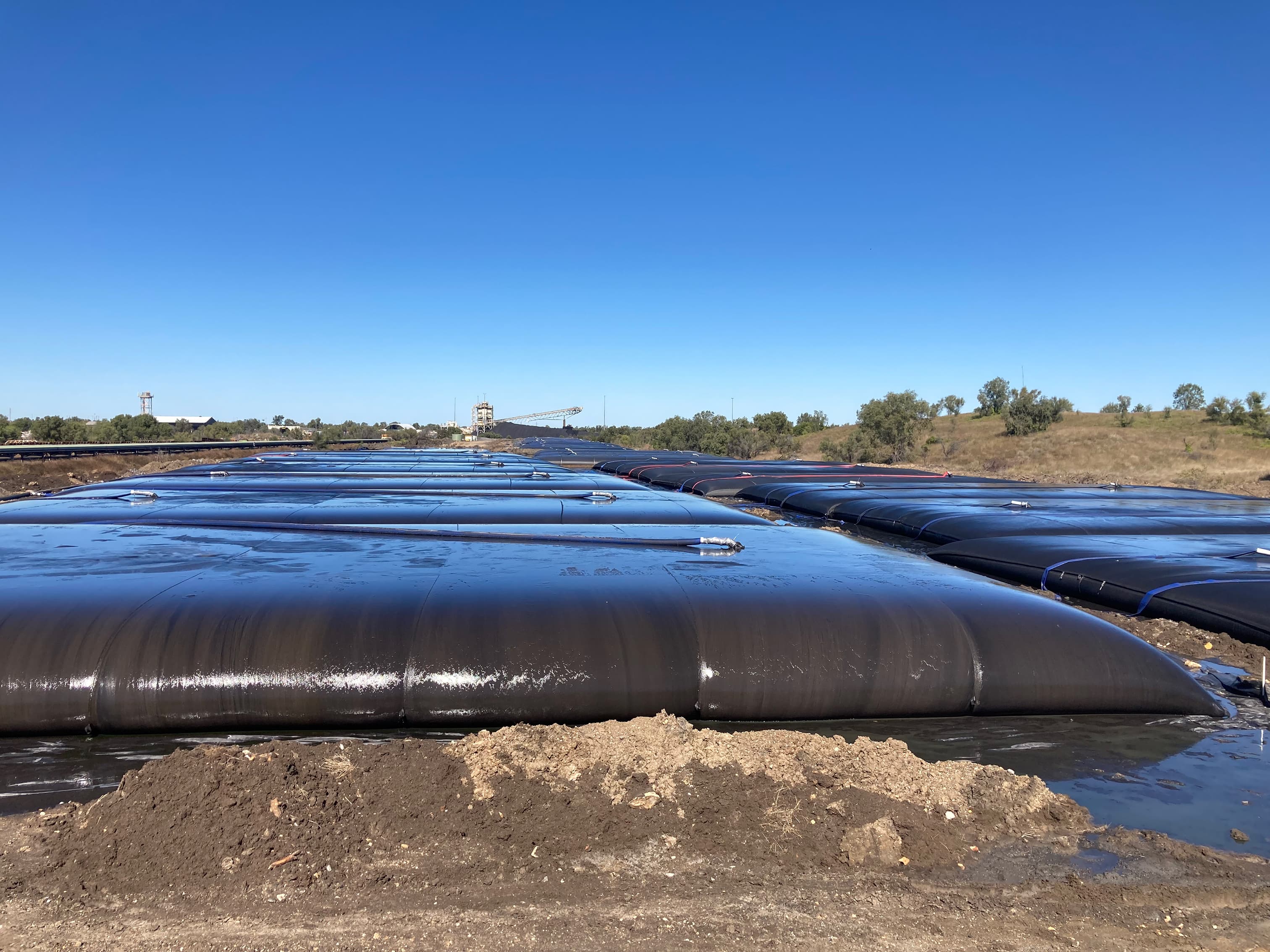
Silt trap dewatering for Kestrel Coal Mine
Kestrel Coal Resources restored silt trap capacity by dredging and dewatering 40,000m³ of silt using GEOTUBE units. The project preserved coal fines for sale.