>

Innovative application of new GEOTUBE technology incorporating moisture draining yarns for enhanced dewatering performance of gold tailings slurry
Overview
A gold mining operation in Victoria, Australia faced the challenge of managing increased mine slurry waste resulting from a surge in production. With the existing tailings storage facility (TSF) already at full capacity, the mine required an immediate and cost-effective solution to handle the waste without constructing a new TSF.
After evaluating various options, Solmax's GEOTUBE® dewatering technology was selected and implemented as the most cost-effective immediate solution.
The GEOTUBE units installed included a mix of standard GEOTUBE GT 500D materials and newly developed GEOTUBE GTL 500D wicking units. These wicking units incorporate innovative yarns capable of absorbing and draining moisture, accelerating slurry dewatering and increasing solid concentrations within the tube units.
Challenge
Faced with the challenge of handling an increased output of tailings slurry while the mine TSF was nearing capacity, the mine management sought a solution to securely dewater and store the excess tailings.
After an extensive evaluation of options, they decided to concentrate and reduce slurry volume by dewatering and containing the slurry using Solmax GEOTUBE units within the existing TSF area. This solution avoided the time and cost implications of expanding the TSF within an already constrained land area.
The GEOTUBE units needed to efficiently dewater a high volume of slurry with a high degree of final solids dryness while managing effluent water discharged from the tubes, all within tight capital and operating cost constraints.
The slurry also presented specific dewatering challenges due to its high solids concentration and the need to ensure that the resulting dewatered material could be safely stored or transported for further processing.
Solution
Following a thorough evaluation of the GEOTUBE system by a highly reputable mine tailings consulting engineering firm, the Solmax GEOTUBE dewatering option was chosen as a flexible, scalable, and cost-effective solution. The GEOTUBE units were sized to fit within the existing TSF, and tests and trials were conducted to confirm that the required dewatering efficiencies could be achieved.
Dewatering system design and testing
To ensure the requirements were met, the mine tailings consultants conducted a series of tests to determine the optimal dewatering parameters for the slurry.
The first test, known as the Rapid Dewatering Test (RDT), assessed the dewatering behavior of the sludge and determined the appropriate type and dosage of flocculants to optimize solids concentration and effluent water discharge. This simple test uses a fifteen to twenty-liter sample of slurry treated with selected flocculants to determine the optimal polymer type, charge, and dosage for the best performance. The test also allows the cost of polymer dosing to be calculated accurately.
The next step was a small-scale pilot trial using a GEOTUBE unit made of GT 500D fabric. This trial confirmed that the parameters from the RDT tests could be replicated on a larger scale, providing an accurate assessment of final solids concentrations and other operational implications.
This pilot trial demonstrated that the GEOTUBE units could achieve over 75% solids concentration after several filling and dewatering cycles, giving an accurate determination of actual project costs.
Full-scale implementation
The installation involved deploying multiple GT500D GEOTUBE units laid over plastic-lined pads. The incoming slurry, with solids concentrations varying between 50% and 60%, was pumped into the GEOTUBE units, with polymer flocculant injected into the feed lines to improve solids capture. The effluent water from the dewatering process was collected in sumps and recycled to adjacent wastewater ponds for reuse.
To ensure correct positioning and deployment of the GEOTUBE units, Solmax installers followed structured guidelines for handling, deploying, and connecting feed pipes to the fill ports on each tube. The guidelines also covered specific design requirements for the pad base and methods to prevent tubes from distorting or being overfilled.
Filling of each GEOTUBE unit was conducted in cycles. Each cycle involved pumping a tube to its maximum designed fill height, then diverting flow to an adjacent tube to allow dewatering and solids retention. This process continued until the tube achieved an optimized concentration of solids.
Wicking-enhanced dewatering performance
In addition to using conventional GEOTUBE units, the mine also installed newly developed wicking-enhanced GEOTUBE GTL 500D units. These innovative materials incorporate yarns that facilitate moisture removal through capillary action, enabling faster and more effective dewatering than non-wicking units.
The wicking GEOTUBE units offered several advantages, including faster formation of the filtration cake and more consistent dryness in the final solids. The wicking fabric also mitigated variations in polymer dosage when pumped slurry solids contents varied, resulting in more reliable performance in less-than-ideal conditions.
Using GEOTUBE units with wicking-capable fabrics enhances dewatering of complex slurries and optimizes the amount of polymer required compared to standard tubes. These benefits will be further quantified over time as dewatering efficiencies of various slurry types are evaluated.
Conclusion
Using GEOTUBE dewatering technology at the Victoria, Australia mine site proved to be a scalable, cost-effective, and efficient solution to tailings waste challenges.
By combining conventional and wicking-enhanced GEOTUBE units, the mine effectively managed increased sludge volumes while minimizing capital expenditure and operational disruptions. This case demonstrates how innovative geosynthetic solutions help mining operations meet waste management goals in a cost-efficient and environmentally responsible manner.
The system's success confirms the versatility and effectiveness of GEOTUBE technology in mining applications, providing a reliable method for dewatering and solids management.
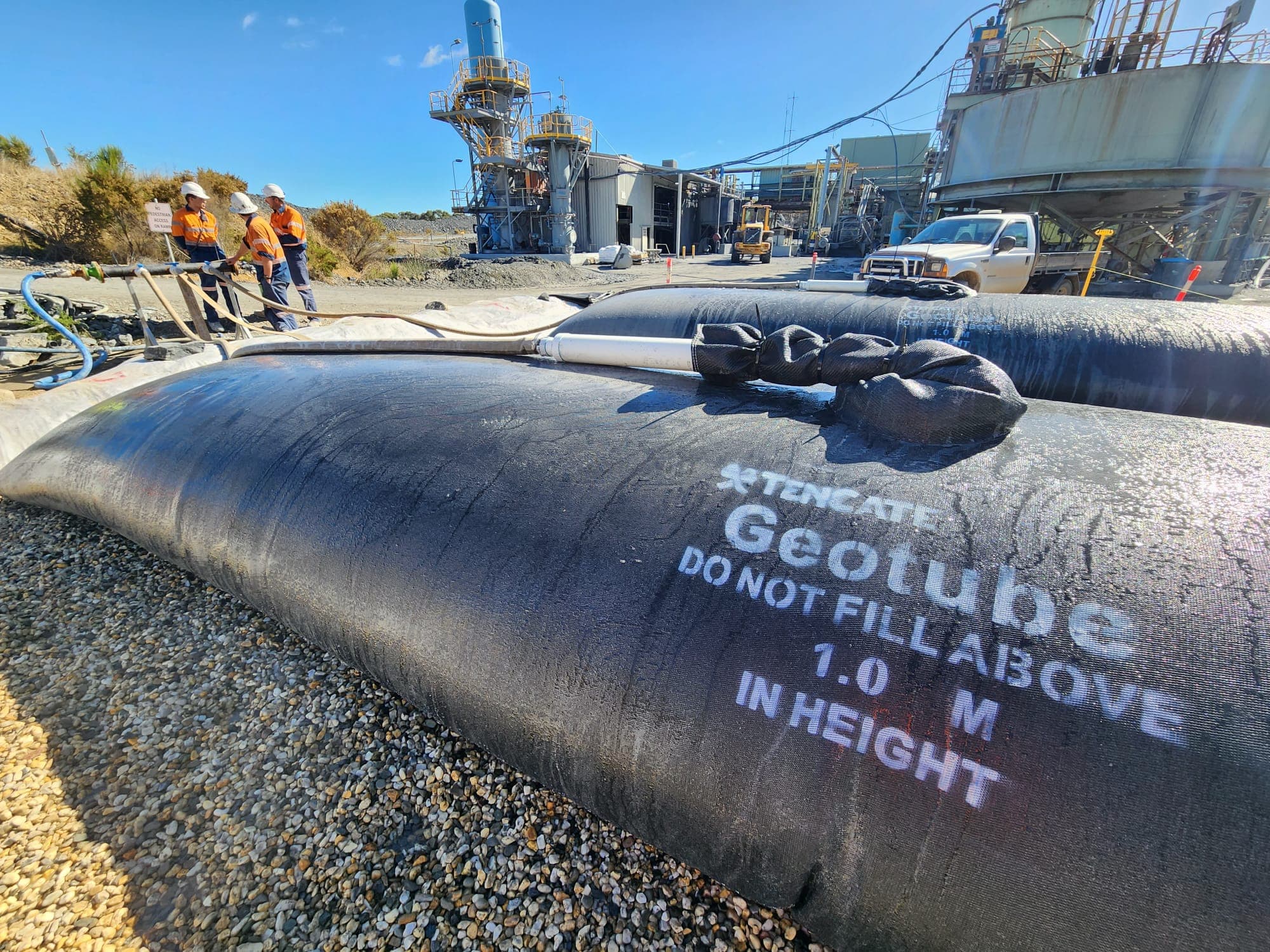
Workers preparing and filling GEOTUBE® units with sludge waste for dewatering at the gold mine, using GT 500D and GTL 500D wicking technology.
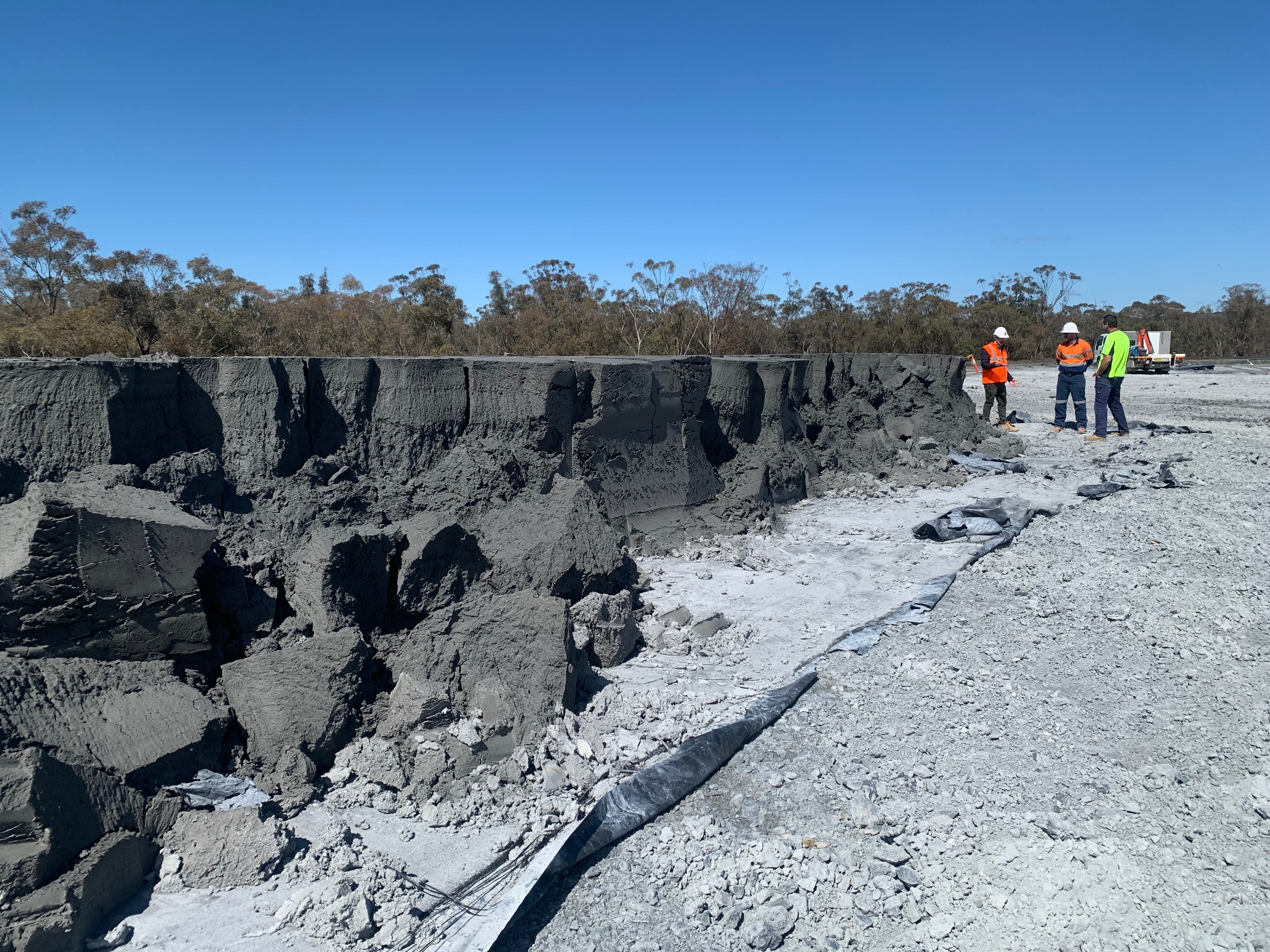
The dewatering system in operation at the gold mine, where GEOTUBE® units effectively separate solids and recover water from sludge waste.
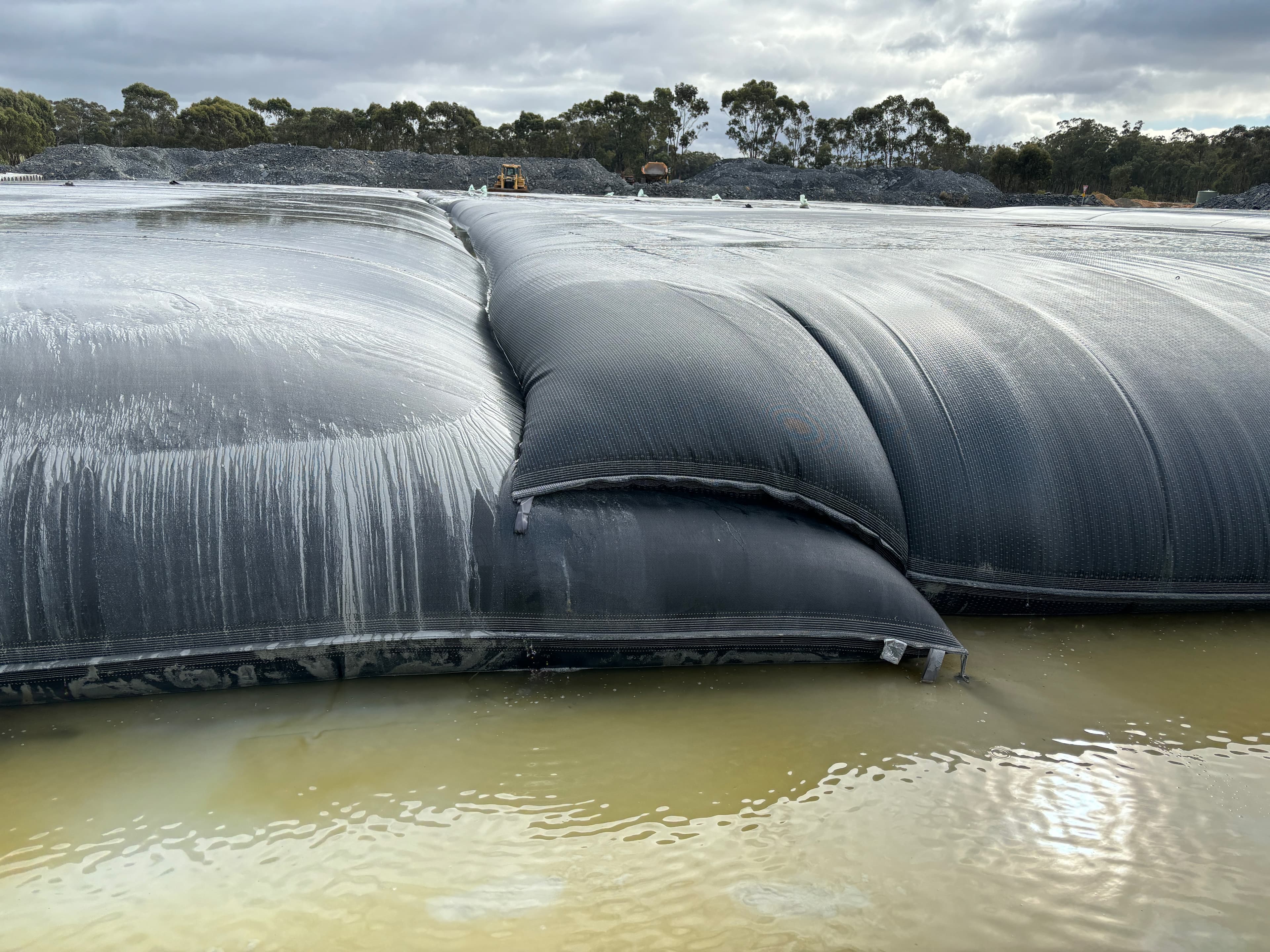
Effluent water being collected in sumps for reuse, demonstrating the sustainable water management approach of the GEOTUBE® system
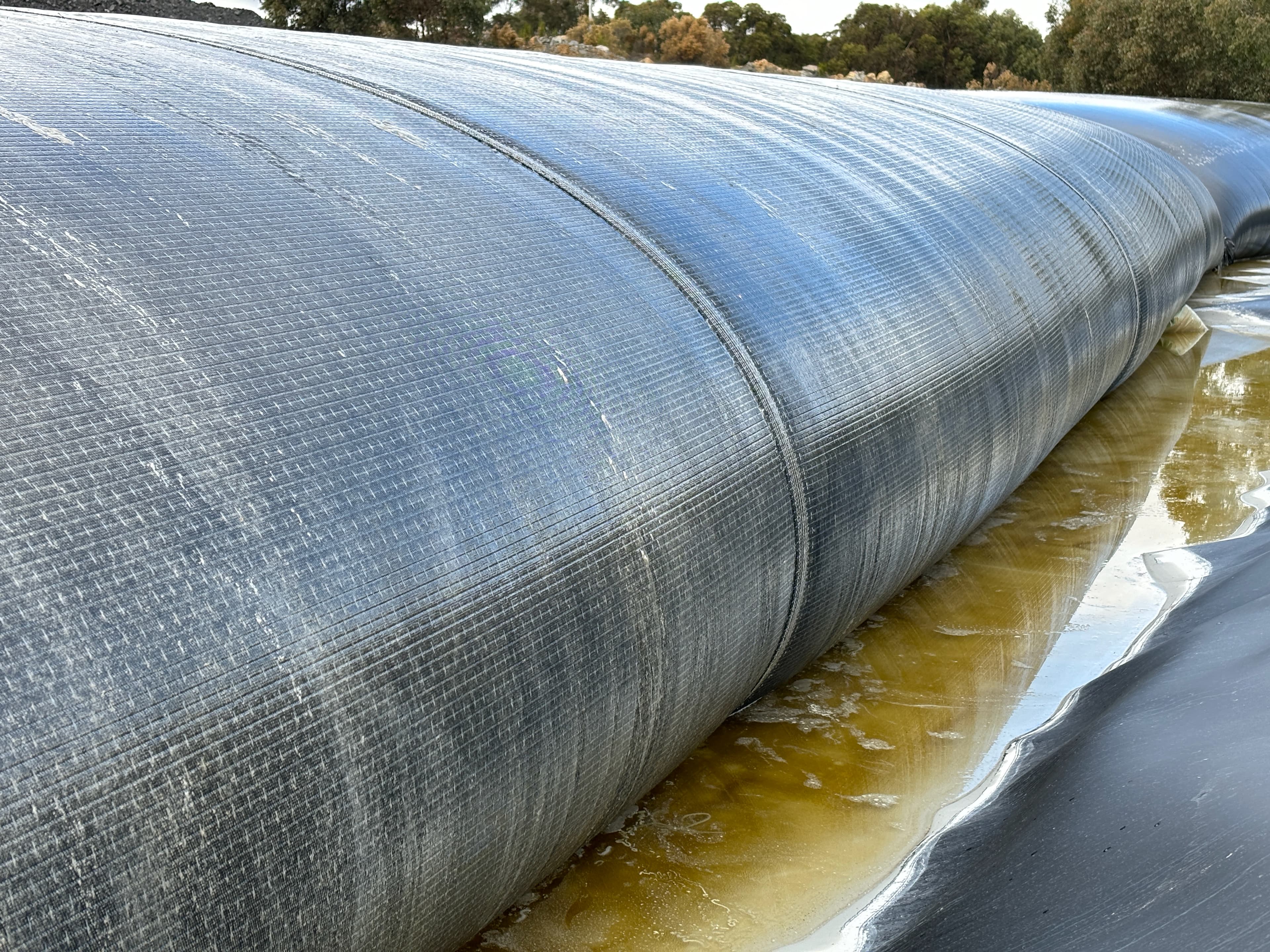
Close-up view of the wicking-capable GEOTUBE® GTL 500D units, showing the specialized yarns that facilitate enhanced dewatering performance
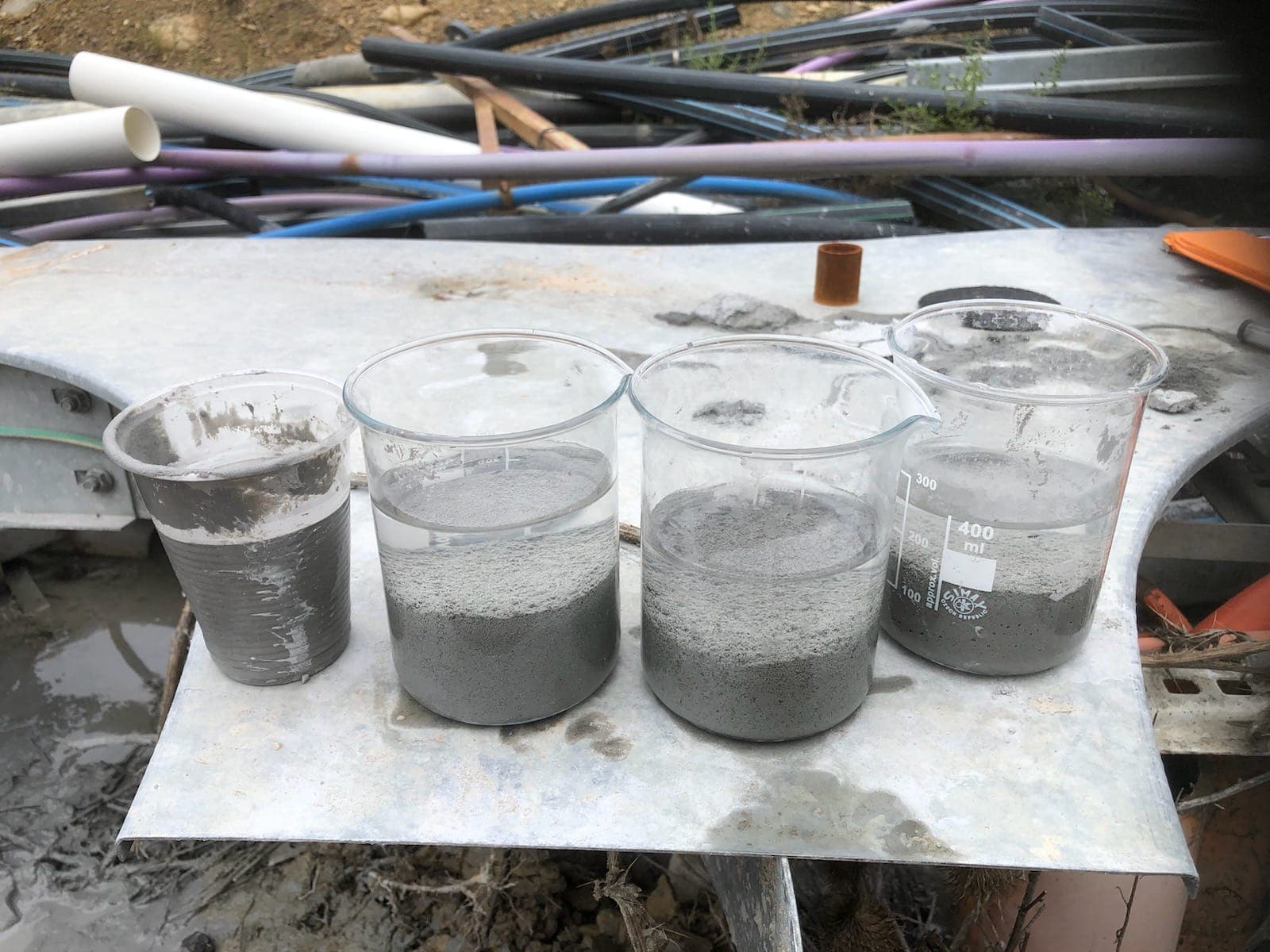
Monitoring GEOTUBE® dewatering progress to ensure optimal solids retention and water recovery at the mine site.

Gold Mine Slurry Waste Dewatering, Victoria, Australia
Explore more case studies
View all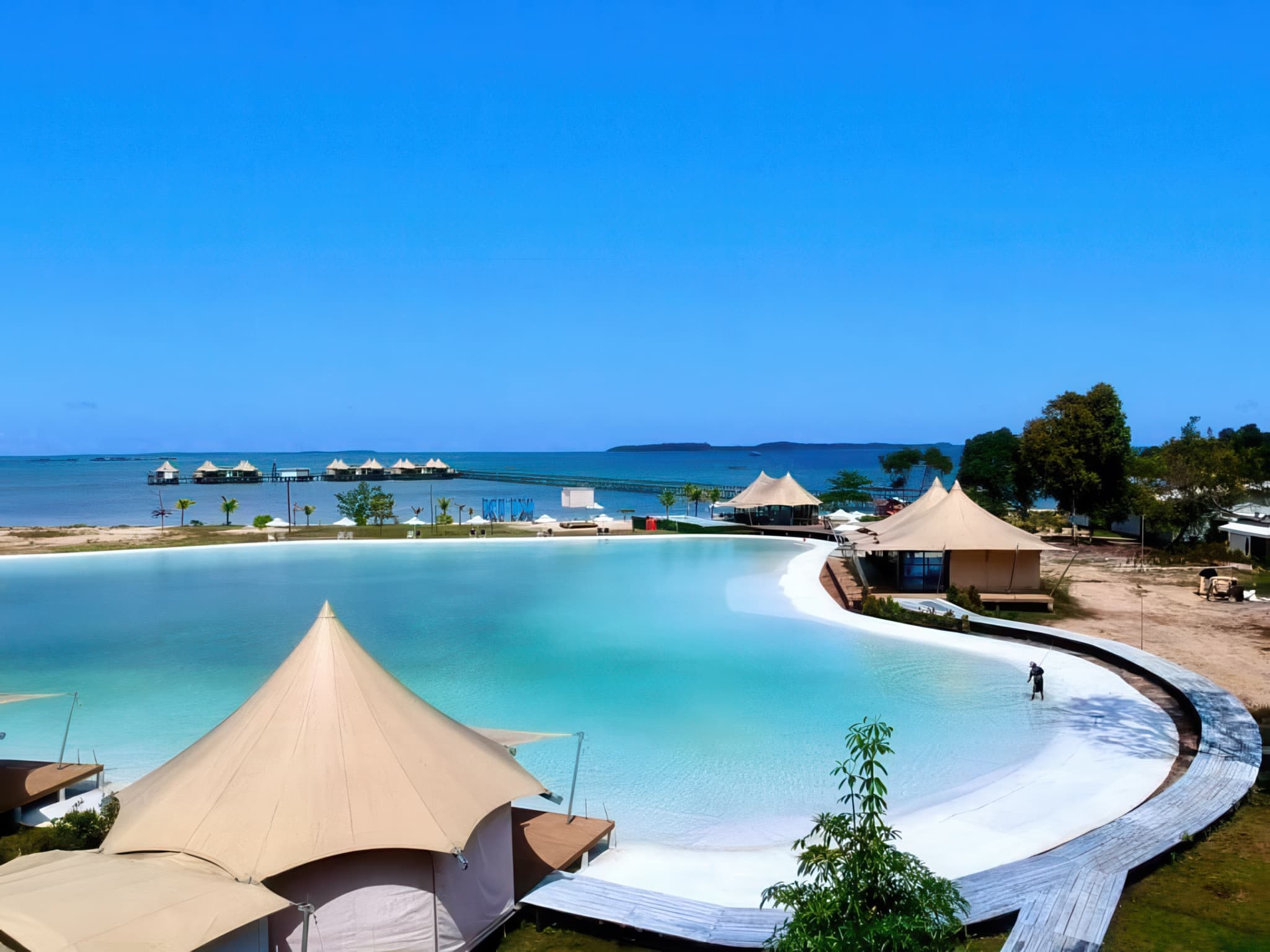
Creating a recreational pond with GSE geomembrane at Kiki Beach Resort
Kiki Beach Resort on Batam Island installed GSE HD 1.50 mm White Smooth for a recreational pond to enhance visual appeal and durability. The solution included custom roll sizes and a GSE Polylock anchoring system to meet design and site challenges.
Restoration of submerged stormwater pipeline
Desilting Solutions restored a submerged stormwater pipeline in Milton, Queensland, to 97% capacity using GEOTUBE technology and remote dredging within a confined site.
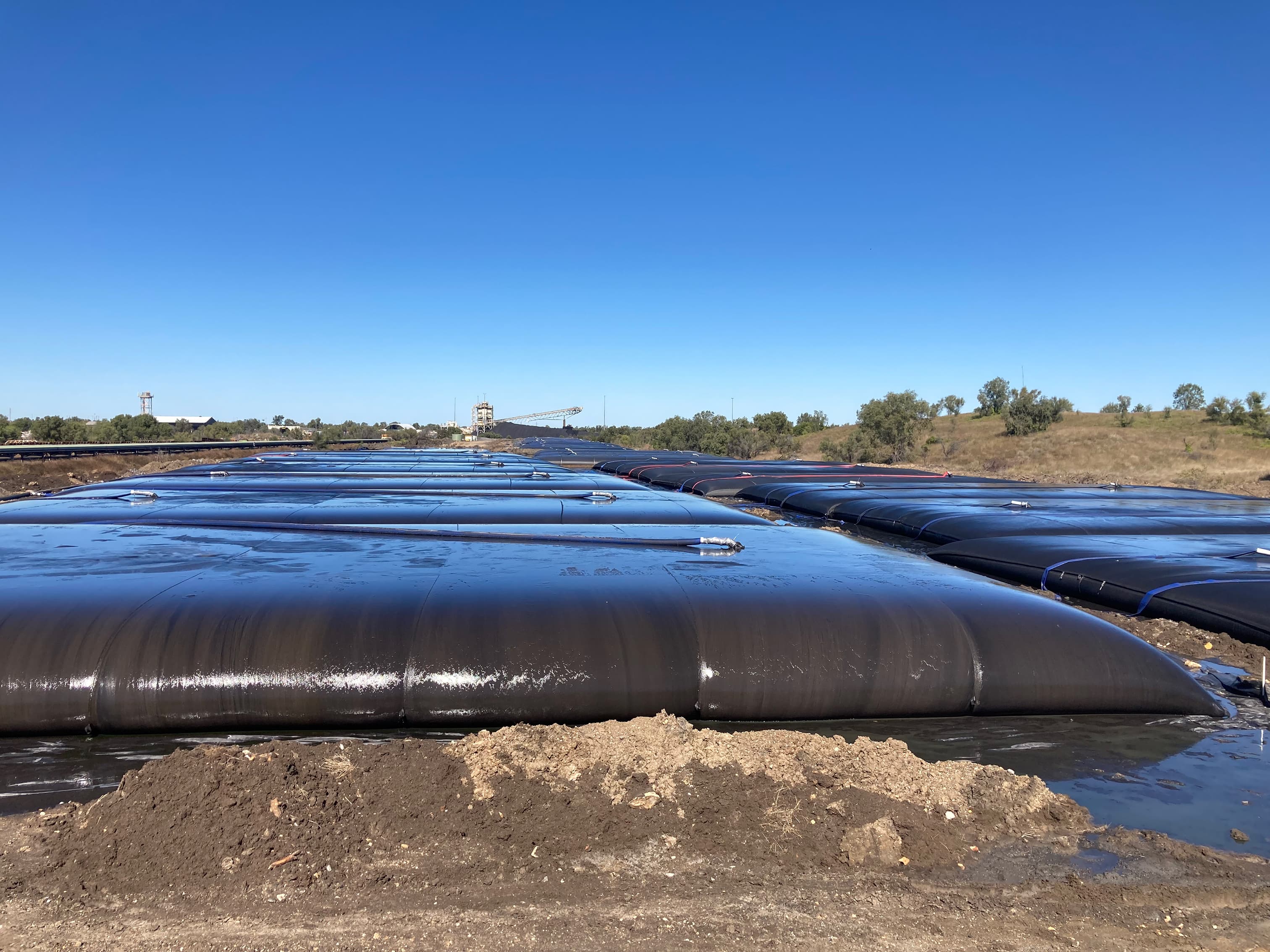
Silt trap dewatering for Kestrel Coal Mine
Kestrel Coal Resources restored silt trap capacity by dredging and dewatering 40,000m³ of silt using GEOTUBE units. The project preserved coal fines for sale.