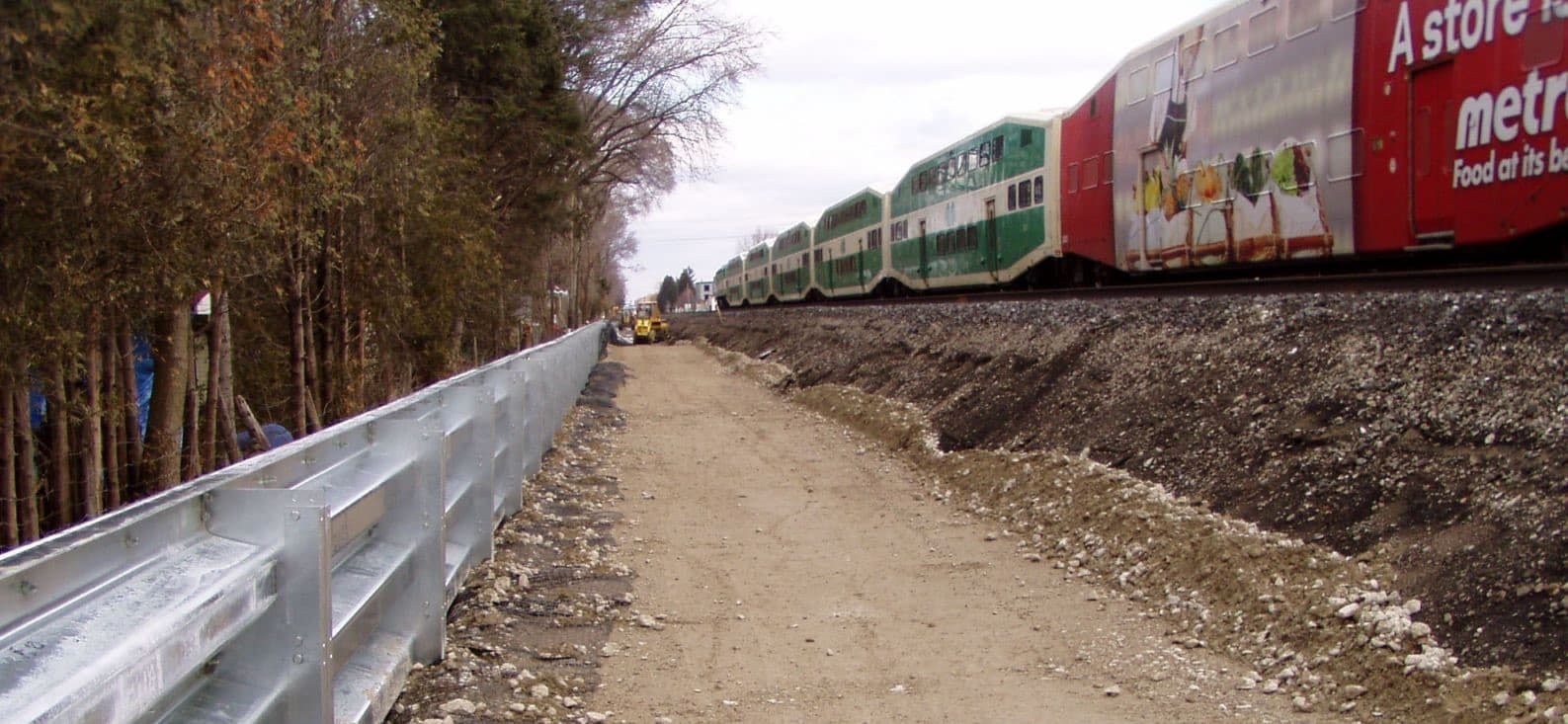
MSE walls with MIRAGRID XT for rail expansion
GO Transit used hybrid MSE walls with MIRAGRID XT geogrids to stabilize embankments on Lakeshore West Line, ensuring stability under space and load constraints.
Canadian Pacific Railway (CP) is an industry leader in rail safety. Its investment in improvements to rail infrastructure has helped the company achieve the safest Class I railroad in North America for more than a decade. When CP’s rail maintenance and safety program identified a section of track that was experiencing settlement and cross-level variations, CP implemented a 10-mile-per-hour slow order on the section of track and scheduled it for immediate repair.
Clifton Associates, a geotechnical engineering firm with expertise in railway infrastructure, was brought on board by CP to investigate potential causes and prescribe a repair. Field investigations showed that a significant amount of moisture was present in the subgrade and surrounding area. Signs of mud-pumping, the movement of subgrade material into the coarse ballast, were apparent along the track’s surface. This indicated that the wet conditions were accelerating subgrade attrition, and the sub-ballast was no longer performing adequately.
To address these challenges, the solution needed to:
Reduce stresses on the subgrade
Protect the subgrade from freezing
Act as a separator between the ballast and sub-ballast
Prevent the upward migration of subgrade fines
Prevent subgrade attrition
Shed water from above
Drain water from below
CP and Clifton Associates had previously used a combination of nonwoven geotextile, triangular geogrid, and cellular confinement products to rehabilitate similar sections of rail. For this project, CP sought a solution that would reduce ballast/sub-ballast requirements, protect the ballast from long-term fouling, and mitigate issues related to frost heave and high moisture content in the subgrade. CP was familiar with the performance of MIRAFI® RS580i and contacted Solmax for a proposal.
Solmax performed an AREMA analysis using the Talbot equation for various subgrade conditions and provided two options.
The first option included a single layer of geosynthetic material between the sub-ballast and subgrade.
The second option included two layers of geosynthetic material: one at the sub-ballast/subgrade interface and another at the sub-ballast/ballast interface.
CP selected the second solution because it addressed the worst-case subgrade condition. This solution combined MIRAFI H₂Ri, a moisture management and reinforcing geosynthetic, at the subgrade, and MIRAFI RS580i, a reinforcing geosynthetic at the sub-ballast/ballast interface.
Another key factor in selecting this solution was reduced track downtime. The robust combination of MIRAFI products resulted in a 43% reduction in the amount of ballast and sub-ballast required. This provided significant time savings related to placement, spreading, and compaction.
Repair of the first 72 ft section was completed in just under seven hours. The removal of the track panel and excavation/removal of the existing rail embankment was completed in approximately one hour.
MSE walls with MIRAGRID XT for rail expansion
GO Transit used hybrid MSE walls with MIRAGRID XT geogrids to stabilize embankments on Lakeshore West Line, ensuring stability under space and load constraints.
Stabilizing soft clay soils and shallow utilities during the reconstruction of Main Street
Main Street in Palisade, CO, was reconstructed using geosynthetics to address soft soils and shallow utilities, reducing excavation and aggregate use.
MIRAFI geotextiles optimize stability and reduce costs at Cargill’s Regina facility
Cargill's Regina facility used MIRAFI H2Ri to stabilize expansive, frost-susceptible soils, reducing sub-ballast thickness by 55% and road construction costs by 20%.