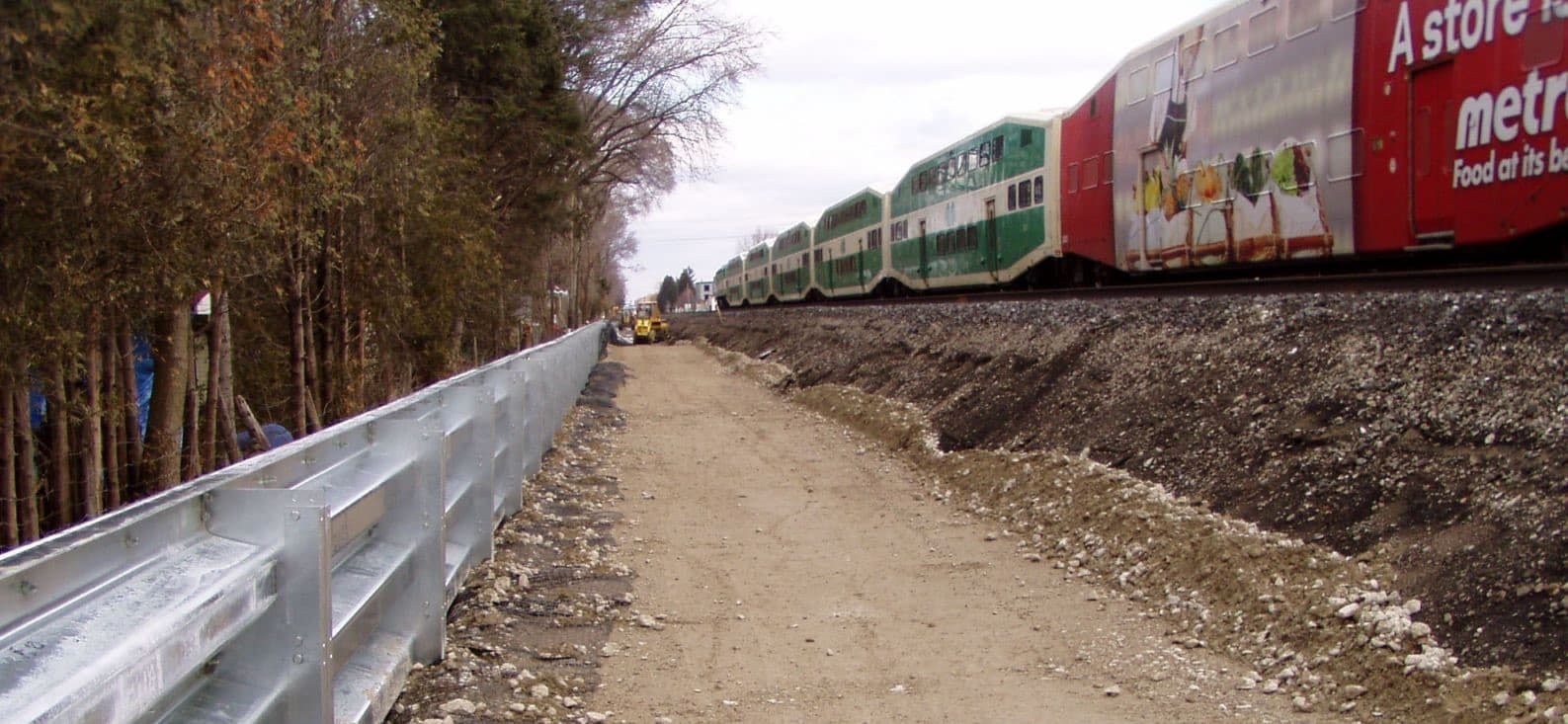
MSE walls with MIRAGRID XT for rail expansion
GO Transit used hybrid MSE walls with MIRAGRID XT geogrids to stabilize embankments on Lakeshore West Line, ensuring stability under space and load constraints.
This project was part of the City of Akron's Main Outfall Sewer Improvements initiative. Solmax role involved collaborating with E.L. Robinson Engineering and Summit Testing & Inspection Services, Inc. Their client, Kenmore Construction Company, which had been appointed to build an administrative control room, screen building, load-out building, and four grit tanks. The design specified that the structures be supported by auger-cast piles. Due to extremely weak subgrade conditions, Kenmore required a working platform to operate the crawler cranes and concrete trucks during the installation of the auger-cast piles.
The construction process involved the use of heavy machinery, such as bulldozers and track hoes, to prepare the site and lay down layers of aggregate for a sturdy pad. To reinforce this pad and prevent any subgrade material from compromising its integrity, MIRAFI® RS580i high-performance geotextile was utilized. The first layer of MIRAFI RS580i was carefully placed over the exposed subgrade and folded up along the sides of the excavation to create a barrier against harmful material seepage. Subsequently, 24 in (61 cm) of aggregate were spread over this layer, followed by another layer of MIRAFI RS580i. Finally, an additional 12 in (30 cm) of aggregate were added, completing the construction of a resilient and robust aggregate pad that was ready to support heavy loads and withstand harsh conditions for extended periods.
In the analysis of working platforms, the focus was typically on the loadings from the crane or drill rig operating on the platform. However, in this scenario involving the installation of auger-cast piles, it was crucial to also consider the loading imposed by concrete trucks. Despite the significant weight of the crawler crane, which exceeded 200,000 lbs (90,718 kg), assessments revealed that the loading from the concrete trucks was more critical. This was because the narrow tires of the concrete trucks exerted greater pressure on the working platform. Therefore, the emphasis shifted toward accommodating the loadings from the concrete trucks to ensure the stability and integrity of the working platform during the pile installation process.
Part 1: Supporting a 200,700 lbs (91,035 kg) Crawler Crane using Westergaard Analysis
Westergaard Analysis
The Naval Facilities Engineering Command (the US Navy version of the US Army Corps of Engineers), Design Manual 7.01 – Soil Mechanics (NAVFAC DM 7.01- utilized by geotechnical engineers all over the world) provides direct guidance (using Westergaard Analysis) on how reinforcing geosynthetics can be used to reduce the pressure imposed on subgrade soils beneath platforms subject to loads from wheel-mounted or track-mounted cranes or drilling rigs.
Calculating load distribution to determine how the weight of the crane spreads out across the platform.
Determining reinforced platform thickness by using load distribution information, subgrade engineering parameters, and geosynthetic-specific engineering parameters.
Checking guidelines to ensure the calculated reinforced platform thickness fits with the guidelines outlined in NAVFAC DM 7.01, NAVFAC DM 7.02, and USACOE ETL 1110-10189.
Part 2: Supporting Concrete Trucks using Giroud-Han (2004) Methodology
Giroud-Han Methodology: This method determines how to support the weight of concrete trucks on an aggregate pad by:
Calculating load distribution using equations from Giroud-Han to estimate vertical pressure on the subgrade resulting from a wheel load at the surface.
Determining reinforcement aggregate section needed based on load information and factors like the strength of the reinforcement material. This determines appropriate geosynthetic reinforcement and aggregate thickness required to provide a stable platform to support the concrete trucks.
Checking guidelines to confirm that our calculations and the type of reinforcement we're using meet the standards in the Giroud-Han method and any other relevant guidelines.
Following these steps helps ensure the right support was provided for both the crawler crane and the concrete trucks, thus supporting the stability and safety of the job site.
MSE walls with MIRAGRID XT for rail expansion
GO Transit used hybrid MSE walls with MIRAGRID XT geogrids to stabilize embankments on Lakeshore West Line, ensuring stability under space and load constraints.
MIRAFI geotextiles prevent subgrade failure and reduce track downtime
Canadian Pacific Railway (CP) identified track settlement issues and partnered with Solmax and Clifton Associates to implement a geosynthetic solution, reducing ballast use by 43% and completing repairs on a 72 ft section in under seven hours.
MIRAFI geotextiles optimize stability and reduce costs at Cargill’s Regina facility
Cargill's Regina facility used MIRAFI H2Ri to stabilize expansive, frost-susceptible soils, reducing sub-ballast thickness by 55% and road construction costs by 20%.