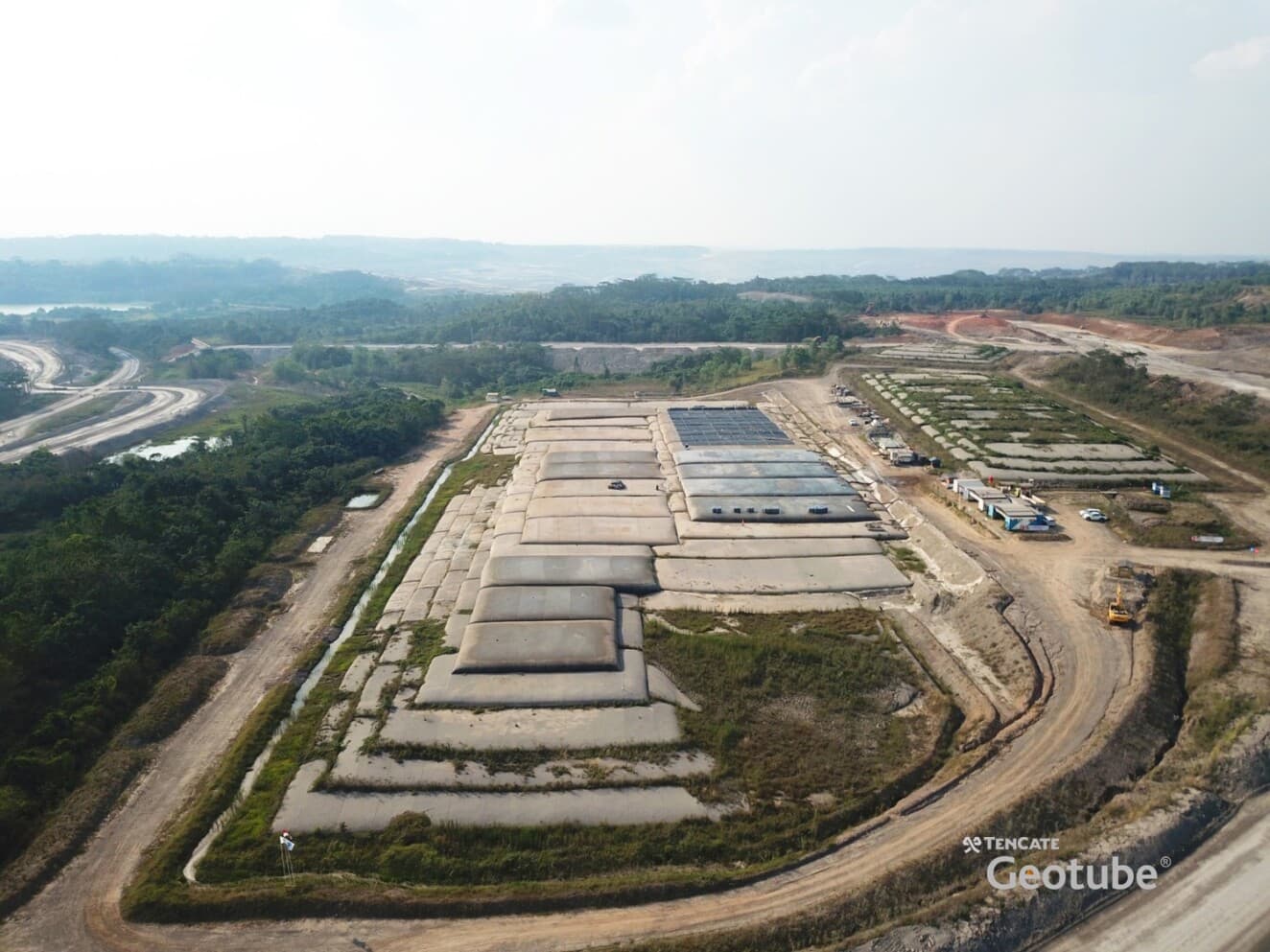
Products
Industries
Transforming coal mine settling ponds with GEOTUBE dewatering
Overview
A large Indonesian mining corporation faced a challenge in dewatering silt sediments from their settling ponds in South Kalimantan, Indonesia. The ponds had reached their capacity, and the company had limited available land space. The cleaning process involved a continuous cycle of silt dredging and truck relocation to prevent runoff with high levels of suspended solids from polluting nearby river channels. However, this approach became too costly.
Challenge
To address the issue, the company implemented a GEOTUBE® dewatering facility as part of their cleanout efforts. Over 300 GEOTUBE units were utilized to dewater more than 1,000,000 m³ (1,307,950 yd³) of sediments annually, containing 170,000 m³ (222,411 yd³) of dry solids. The GEOTUBE dewatering tubes were stacked up to seven layers high, using standardized units with a circumference of 36.6 meters (120 feet) and lengths up to 61.4 meters (201 feet), to create large solid landfill structures and optimize land space.
This project stands as one of the largest GEOTUBE dewatering projects ever undertaken worldwide, providing valuable insights into the economics of large-scale GEOTUBE dewatering. It has recently received the 2021 International Achievement Award (IAA) - Award of Excellence.

Coal mine settling ponds South Kalimantan Ponds+Storage GEOTUBE
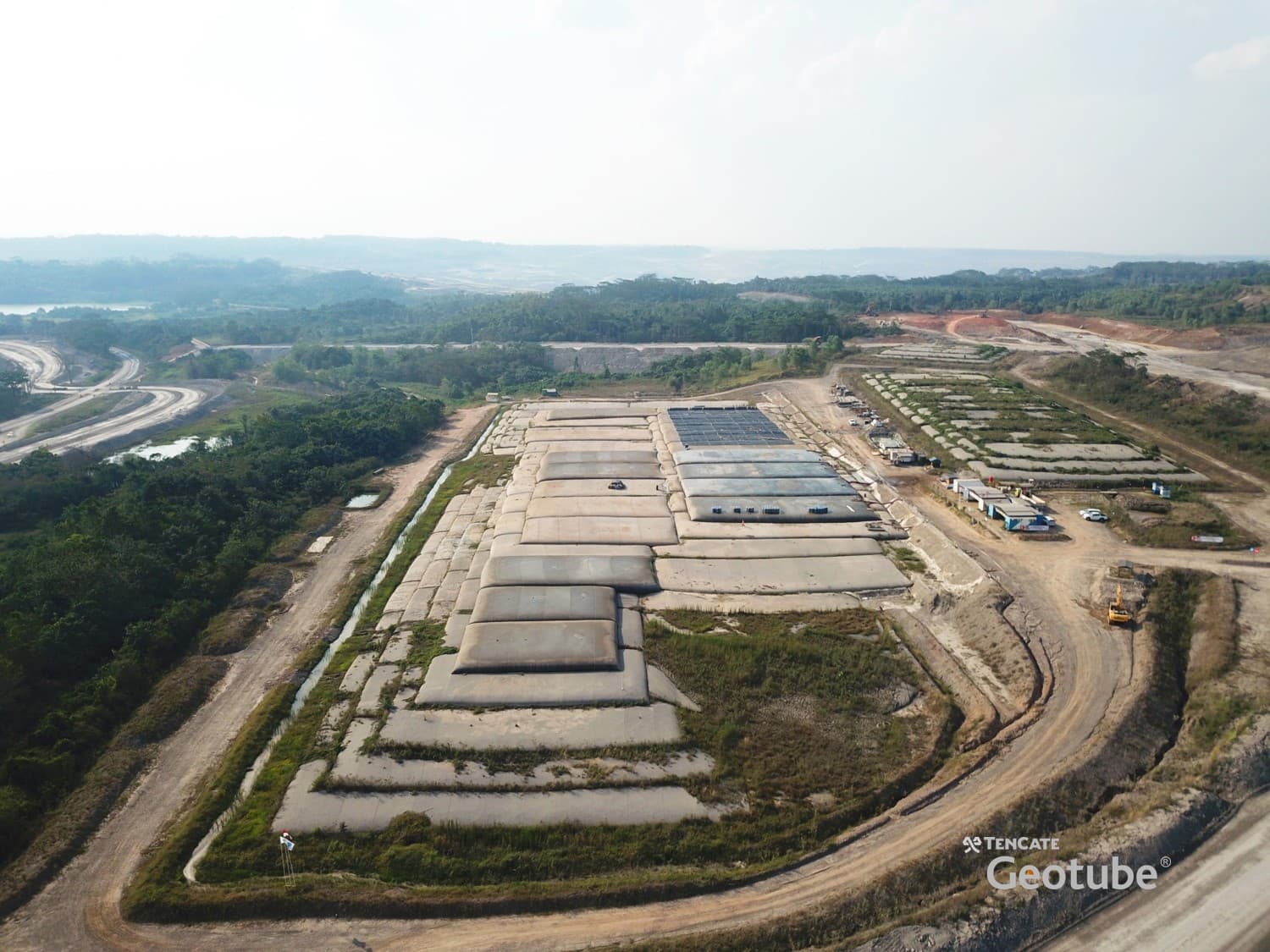
Coal mine settling ponds South Kalimantan Ponds+Storage GEOTUBE

Coal mine settling ponds South Kalimantan Ponds+Storage GEOTUBE
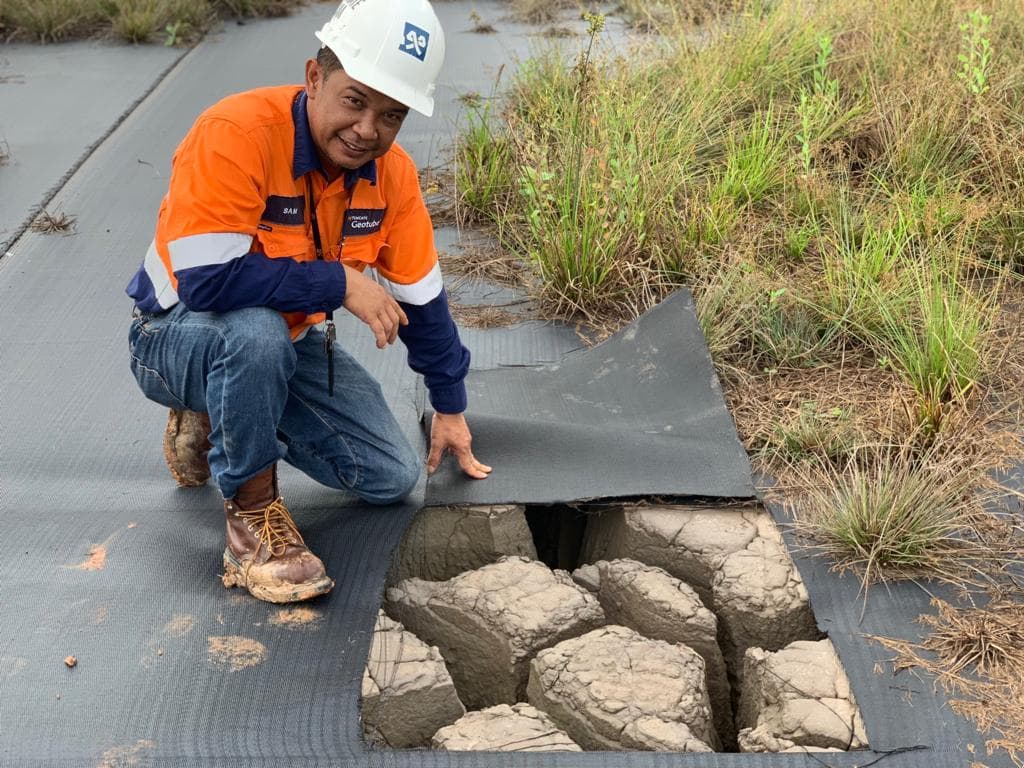
Coal mine settling ponds South Kalimantan Ponds+Storage GEOTUBE
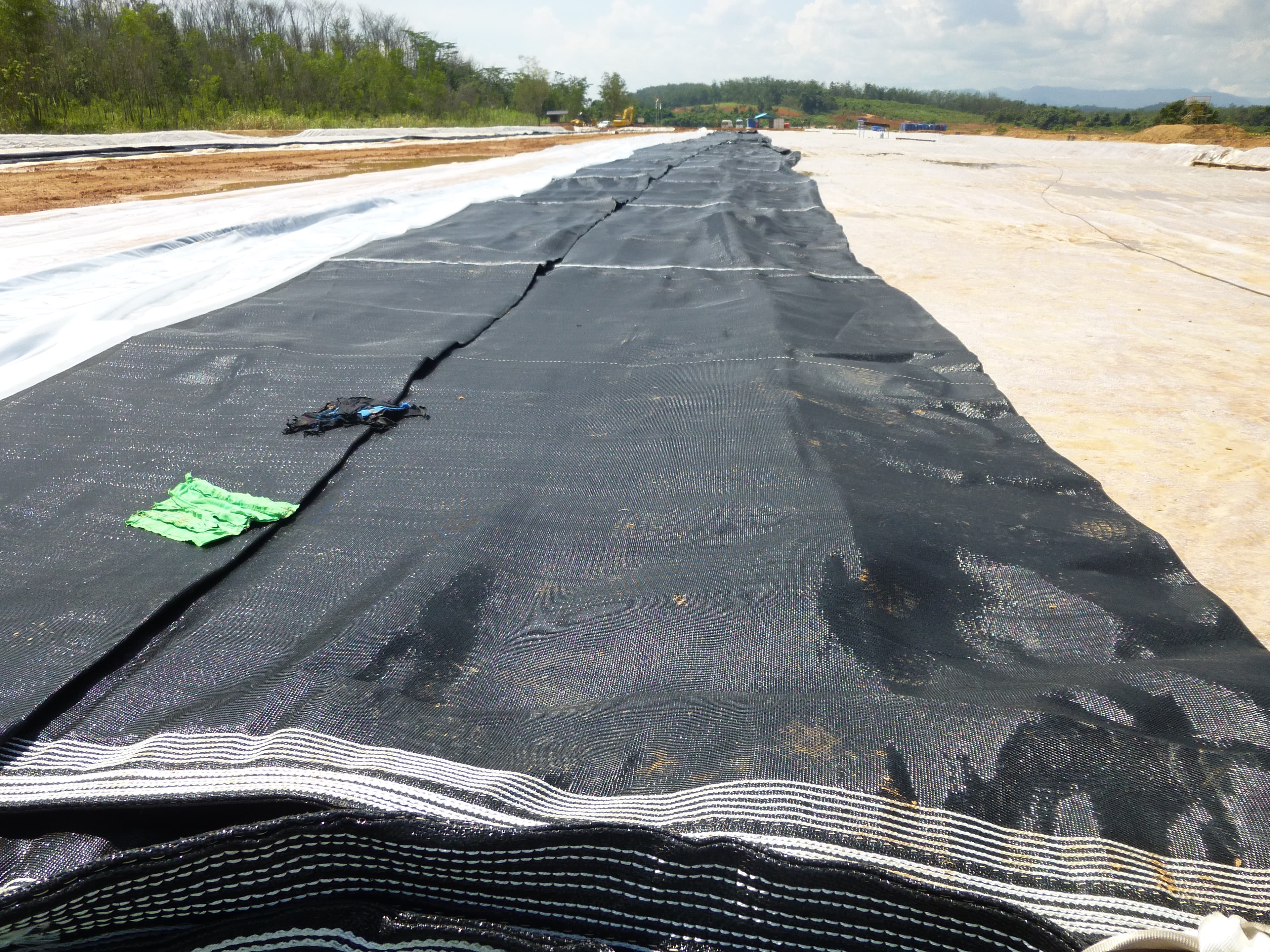
Coal mine settling ponds South Kalimantan Ponds+Storage GEOTUBE
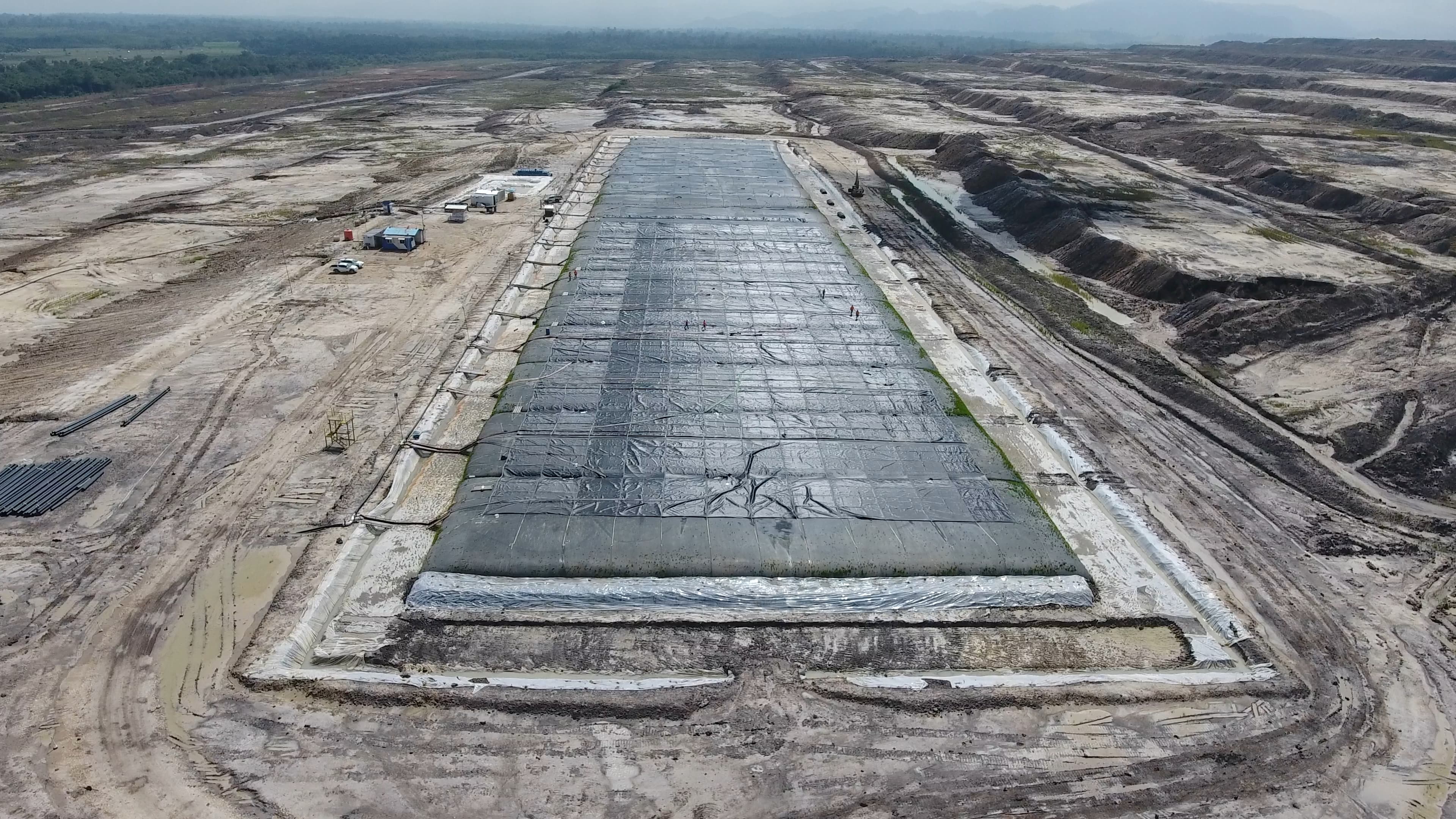
Coal mine settling ponds South Kalimantan Ponds+Storage GEOTUBE
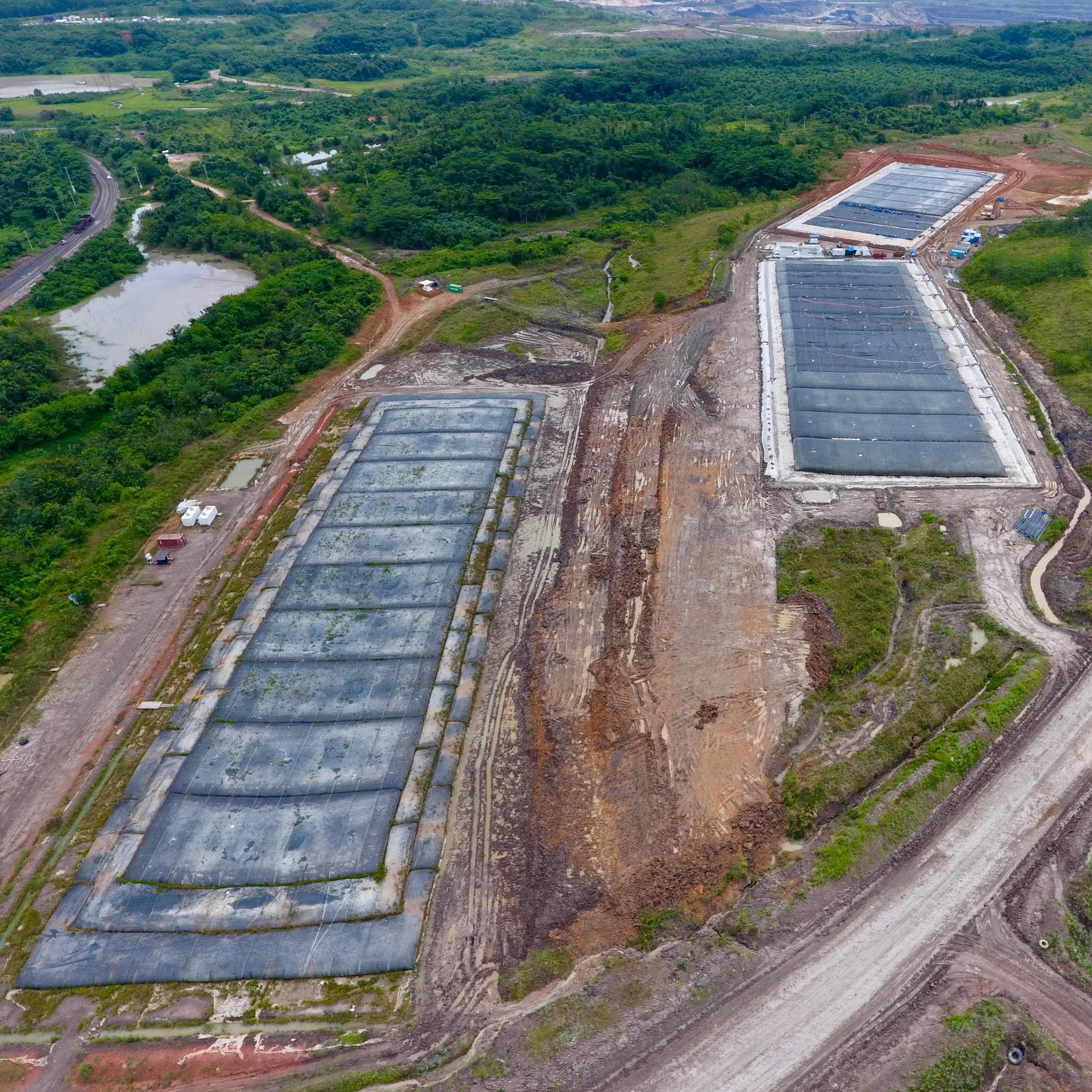
Coal mine settling ponds South Kalimantan Ponds+Storage GEOTUBE

Coal mine settling ponds South Kalimantan Ponds+Storage GEOTUBE
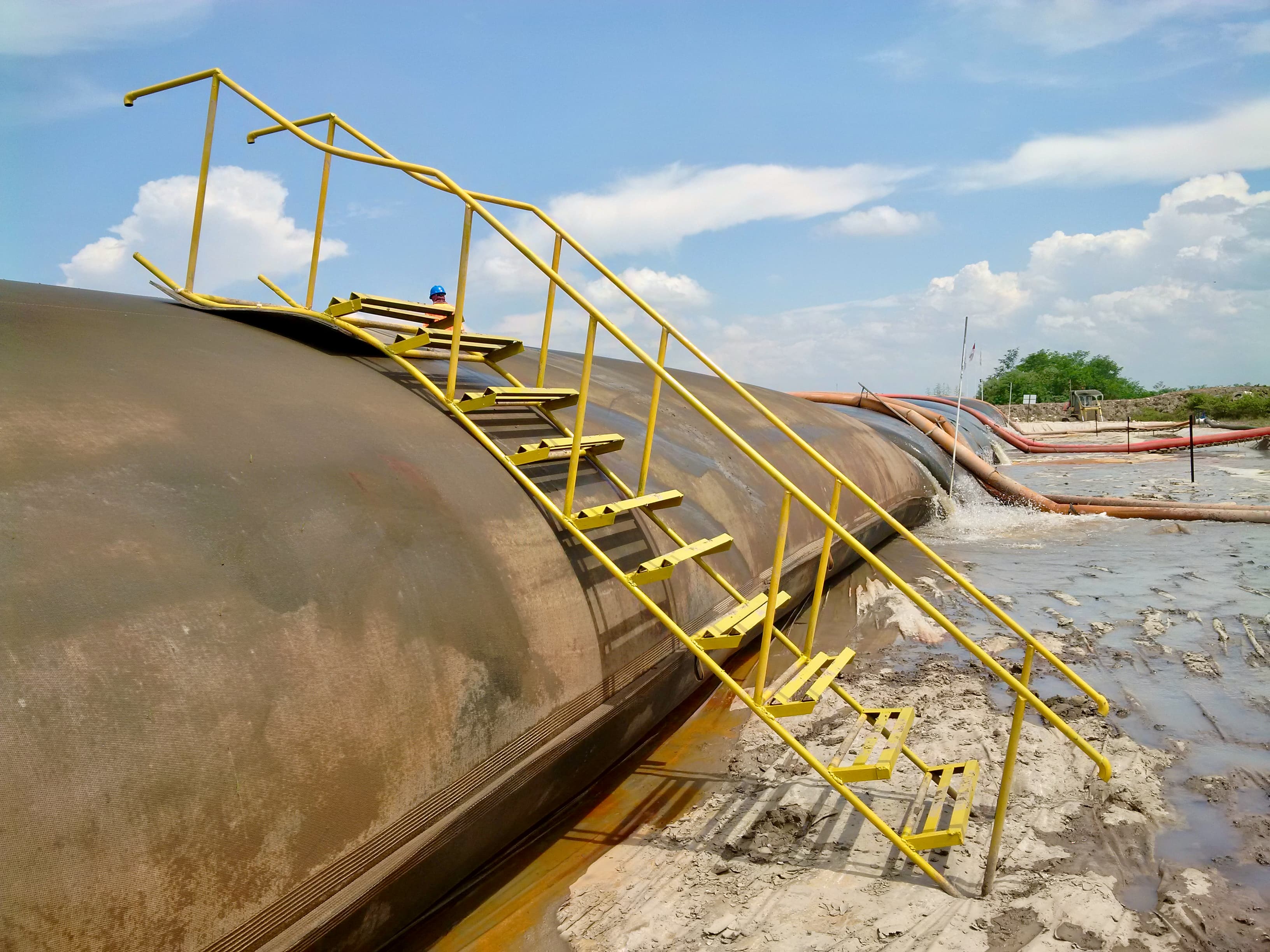
Coal mine settling ponds South Kalimantan Ponds+Storage GEOTUBE
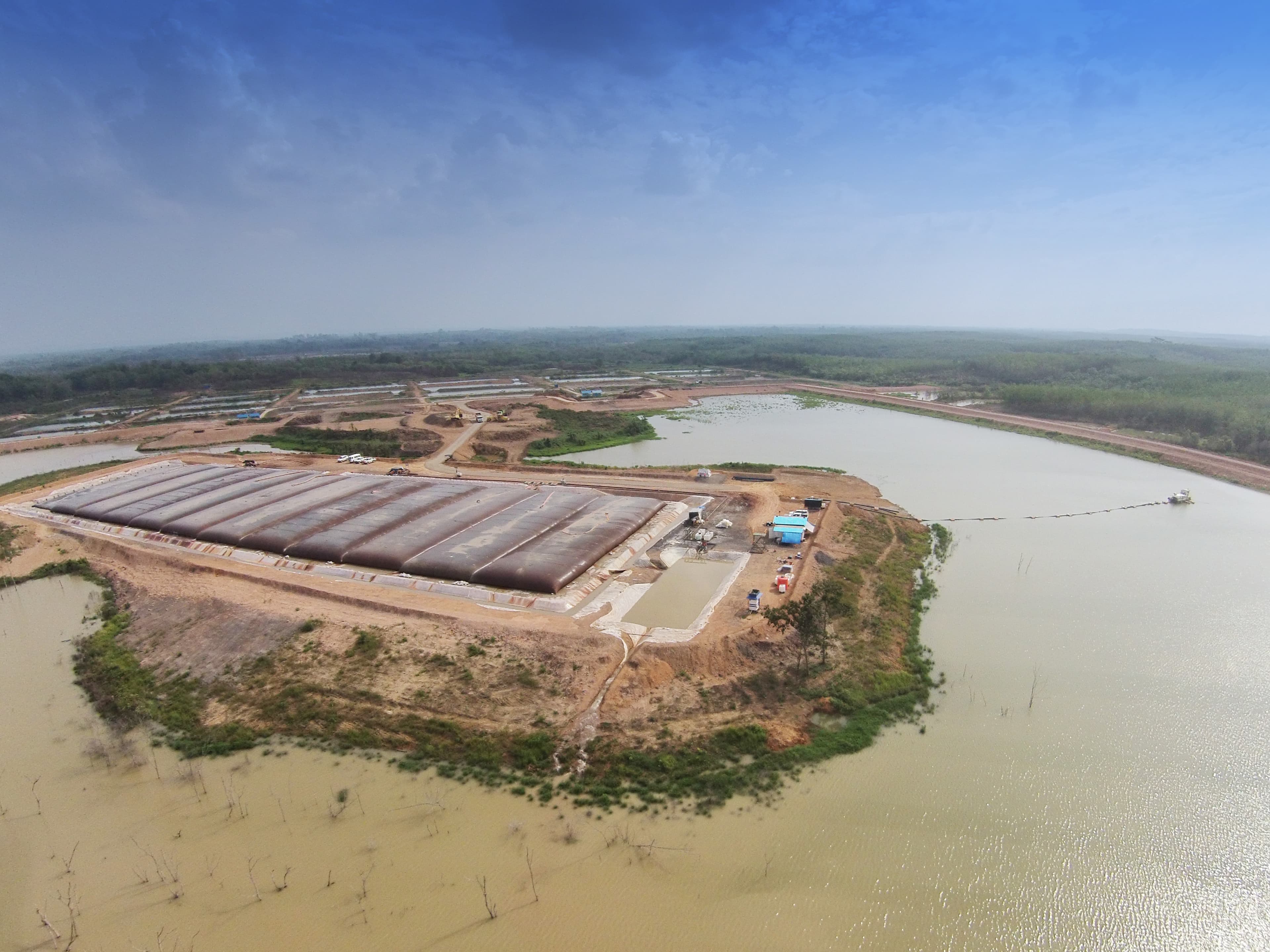
Coal mine settling ponds South Kalimantan Ponds+Storage GEOTUBE
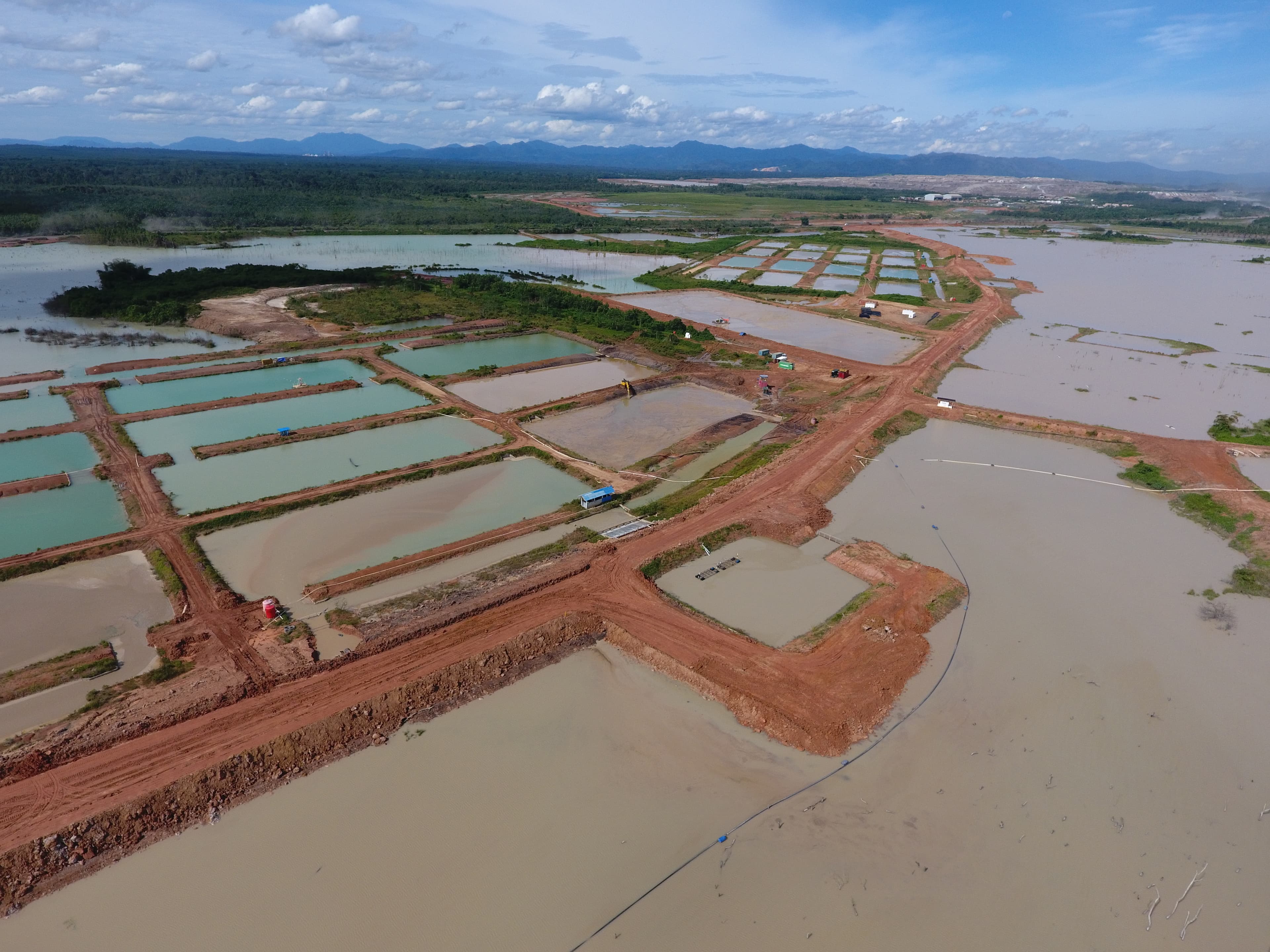
Coal mine settling ponds South Kalimantan Ponds+Storage GEOTUBE
Explore more case studies
View allMIRAFI geotextiles prevent subgrade failure and reduce track downtime
Canadian Pacific Railway (CP) identified track settlement issues and partnered with Solmax and Clifton Associates to implement a geosynthetic solution, reducing ballast use by 43% and completing repairs on a 72 ft section in under seven hours.
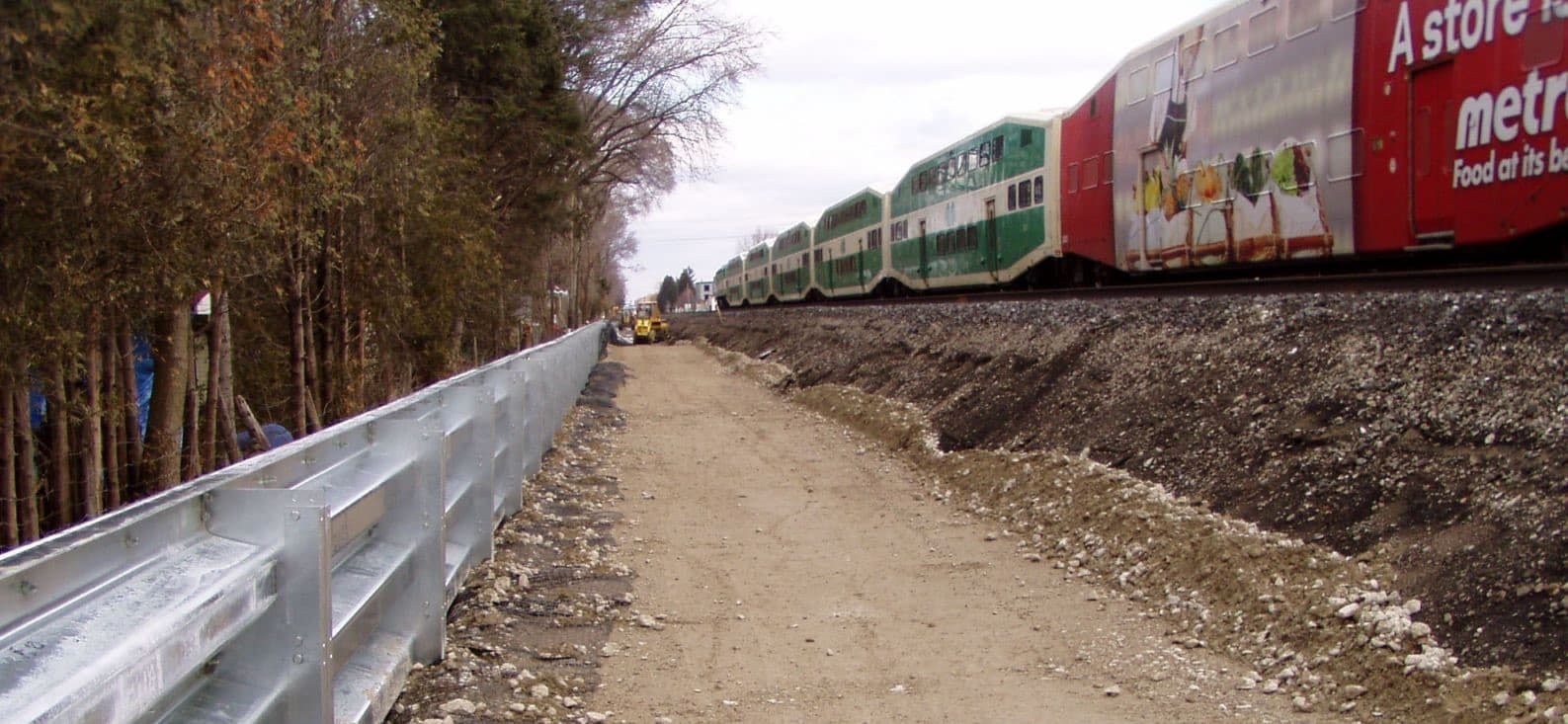
MSE walls with MIRAGRID XT for rail expansion
GO Transit used hybrid MSE walls with MIRAGRID XT geogrids to stabilize embankments on Lakeshore West Line, ensuring stability under space and load constraints.
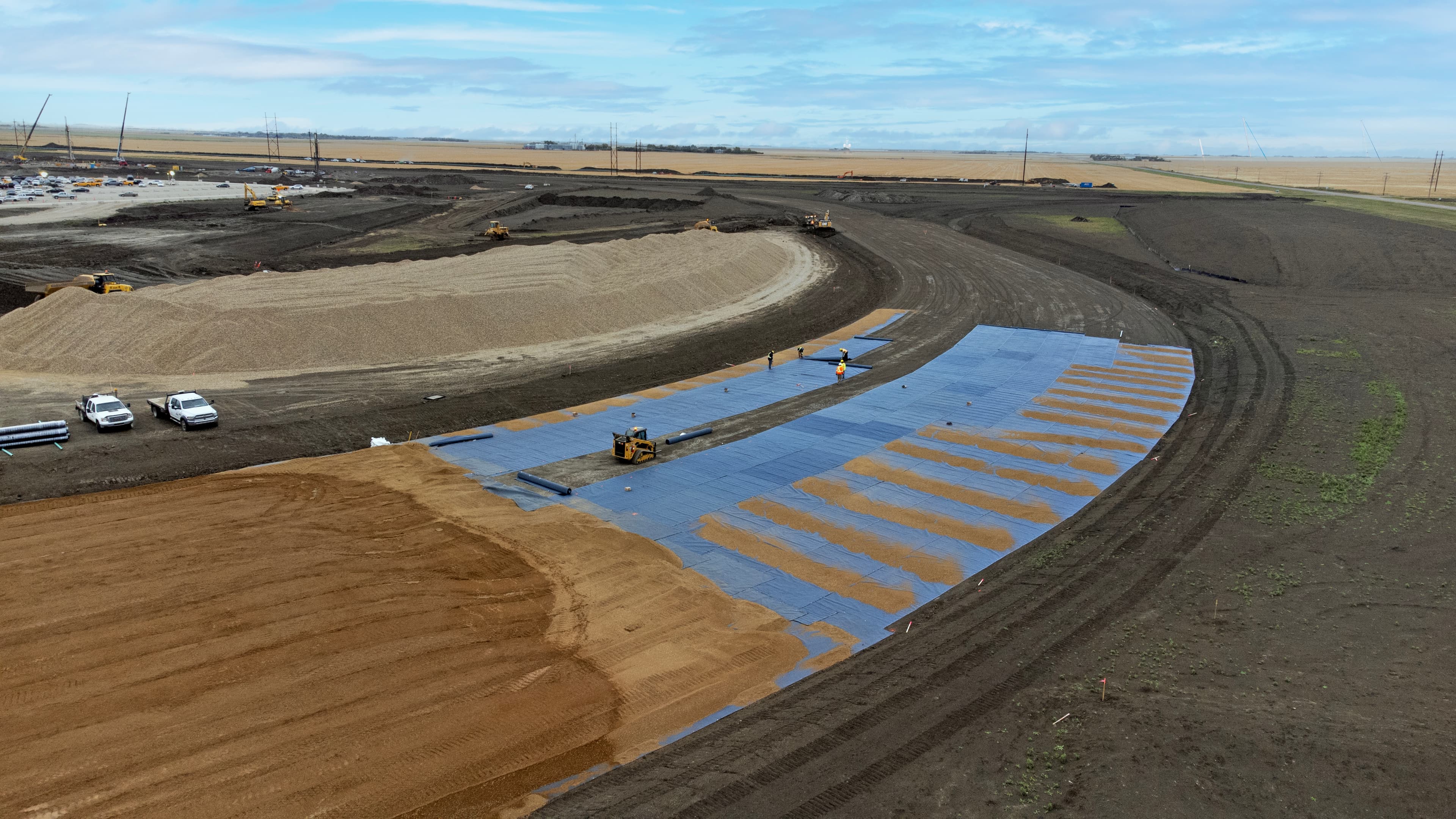
MIRAFI geotextiles optimize stability and reduce costs at Cargill’s Regina facility
Cargill's Regina facility used MIRAFI H2Ri to stabilize expansive, frost-susceptible soils, reducing sub-ballast thickness by 55% and road construction costs by 20%.