Products
Industries
Geotextile solution for seafloor pipeline laying in Jamnagar, Gujarat
Overview
The Jamnagar refinery, located in northwest India, is a crude oil refinery with a production capacity of 661,000 barrels per day. To accommodate the planned expansion of doubling its production capacity to 1.2 million barrels per day, a significant amount of wastewater will be generated during the crude oil extraction process. To prevent environmental contamination, it was decided to dispose of the treated wastewater through pipelines laid on the seafloor. The project involved laying five 1.4m (4.6 ft) diameter pipes over a distance of two and a half kilometers (1.6 miles) in a pre-dredged trench measuring 70.5m (231.3 ft) wide and 3.5m (11.5 ft) deep.
Solution
To ensure separation between the bedding material and the silt, a layer of MIRAFI® Polyfelt® TS009 nonwoven geotextile was placed at the bottom of the trench. This was followed by a 300mm (11.8 in) thick layer of well-graded aggregates. The MIRAFI Polyfelt TS009 geotextile acted as a separator, preventing the loss of aggregate into the soft subgrade of the seafloor and maintaining the structural integrity of the aggregate fill layer. After the pipes were installed, the trench was backfilled with in-situ soils. The decision to lay the pipelines in a trench was made to protect them from potential damage caused by local navigation.
On-site, two sections of MIRAFI Polyfelt geotextiles measuring 4 m (13.1 ft) in width were stitched together longitudinally, forming 7.5 m (24.6 ft) wide geotextile panels. These panels were then accurately deployed at the base of the trench using an 8 m (26.2 ft) wide spreader bar mounted on a crane situated on a floating barge. The 7.5 m (24.6 ft) wide x 2.5 km (1.6 miles) long MIRAFI Polyfelt TS009 geotextile was rolled off into the water with the assistance of counterweights in the form of bags filled with aggregate. Divers were employed to facilitate the installation of the MIRAFI Polyfelt TS009 geotextile. The pipes were placed at a distance of 3.5 m (11.5 ft) center to center within the trench. This careful selection of construction materials and their installation proved to be a significant cost-saving measure.
Jamnagar Refinery Pipelines, India Waste management MIRAFI Polyfelt TS
Jamnagar Refinery Pipelines, India Waste management MIRAFI Polyfelt TS
Jamnagar Refinery Pipelines, India Waste management MIRAFI Polyfelt TS
Jamnagar Refinery Pipelines, India Waste management MIRAFI Polyfelt TS
Explore more case studies
View all
Innovative application of new GEOTUBE technology incorporating moisture draining yarns for enhanced dewatering performance of gold tailings slurry
A gold mine in Victoria, Australia, used Solmax GEOTUBE units with moisture-absorbing wicking yarns to improve water release, efficiently managing increased slurry waste in its limited-capacity tailings storage.
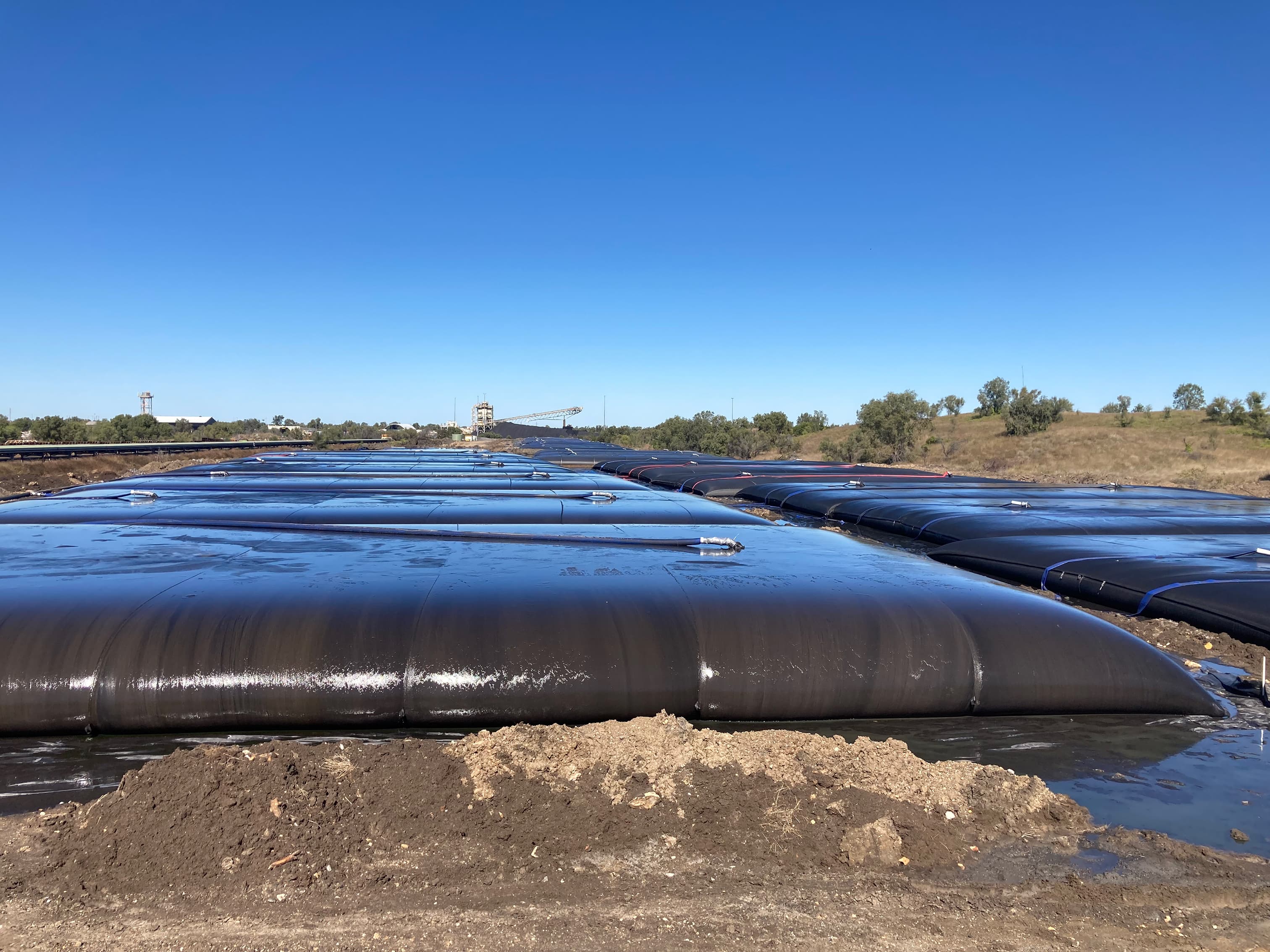
Silt trap dewatering for Kestrel Coal Mine
Kestrel Coal Resources restored silt trap capacity by dredging and dewatering 40,000m³ of silt using GEOTUBE units. The project preserved coal fines for sale.
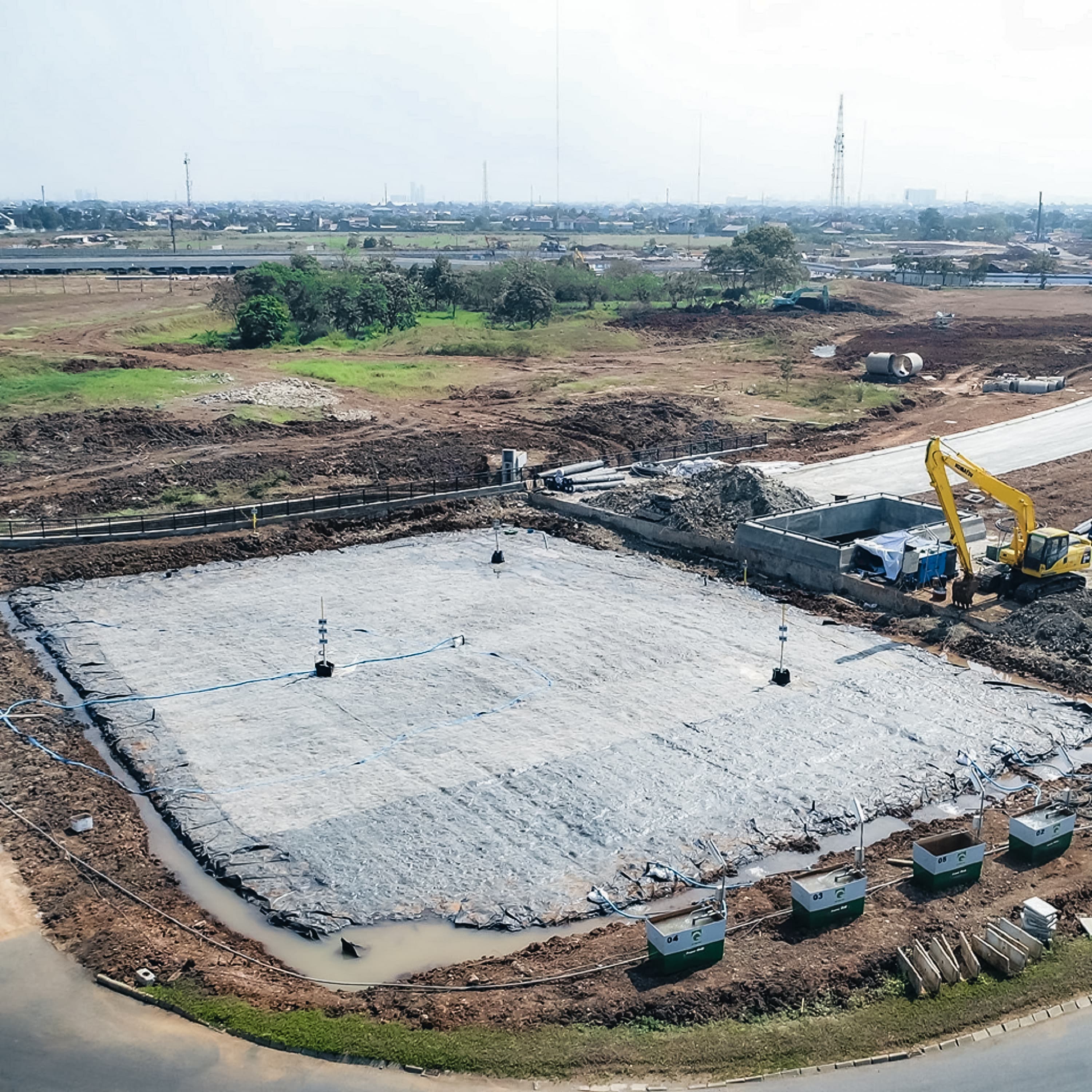
Soft-soil consolidation improvements ensure new housing development launches on time
Solmax provided a custom GSE HD geomembrane solution for the Summarecon Housing Estate in Bandung, enabling full soil consolidation in four months and ensuring the project launched on time.