
Products
Industries
Pengerang Integrated Petroleum Complex: Basal reinforced embankment solution
Overview
The Pengerang Integrated Petroleum Complex (PIPC) is a major project in Pengerang, Johor, Malaysia. Spanning 8,094 hectares (20,000 acres), it is a significant investment and a key contributor to Malaysia's economy, providing numerous job opportunities. With its strategic location at the southeastern tip of Peninsular Malaysia, PIPC offers easy access to international shipping lanes and a well-connected road network to Singapore and other major ports in the region. To establish stable and cost-effective road connections, approximately 22 km (13.7 mi) of access road was constructed using high-strength geotextiles for basal reinforcement.
Challenge
The access road plays a vital role in reducing transportation distance and time. To create the road network, a series of basal reinforced embankments were designed based on the existing ground terrain. The embankment heights ranged from 2.5 m (8.2 ft) to 19.5 m (64 ft), posing a challenge due to the soft soil composition of the Pengerang site, which consists of sand, silt, clay, and peat. Soil investigations revealed that the foundation consisted of 4.0 m (13.1 ft) of soft soil, followed by 11.0 m (36.1 ft) of medium stiff silt, and finally a hard layer. The top layer of soft, highly plastic silt and clay proved incapable of supporting the high embankment.
Solution
To ensure the stability of the embankment on soft ground, a proper design was crucial. Prefabrication Vertical Drain (PVD) was proposed to accelerate the consolidation of soft soil in certain sections of the access road embankment. MIRAFI® Polyfelt® TS50 non-woven geotextile was used as a separator to prevent mixing between backfill soil and existing soft soil. The construction of the basal reinforced embankment relied on MIRAFI PET high-strength geotextile. Different grades and layers of high-strength geotextile were employed based on the embankment's geometry and foundation conditions. Multiple layers of high-strength geotextiles, including MIRAFI PET200-50, MIRAFI PET 400-50, and MIRAFI PET 1000-50, were incorporated to support a 19.5 m (64 ft) high road embankment.
Solution
The installation process involved removing soft layers such as clay or peat and replacing them with engineered fill before laying the geotextiles. Sharp objects that could damage the geotextiles were also removed. A separator geotextile (MIRAFI Polyfelt TS50) was placed on the foundation, followed by backfilling with granular material for drainage purposes. PVD was installed by vibrating a hollow steel mandrel into the soft foundation soil. MIRAFI PET geotextile was laid in layers perpendicular to the alignment of the access road embankment. Bulldozers were used to spread and compact the selected engineered backfilling until the final design platform level was achieved. For embankments with multiple layers of high-strength geotextile, a 0.5 m (1.6 ft) spacing was maintained between each layer, filled with suitable backfill material.
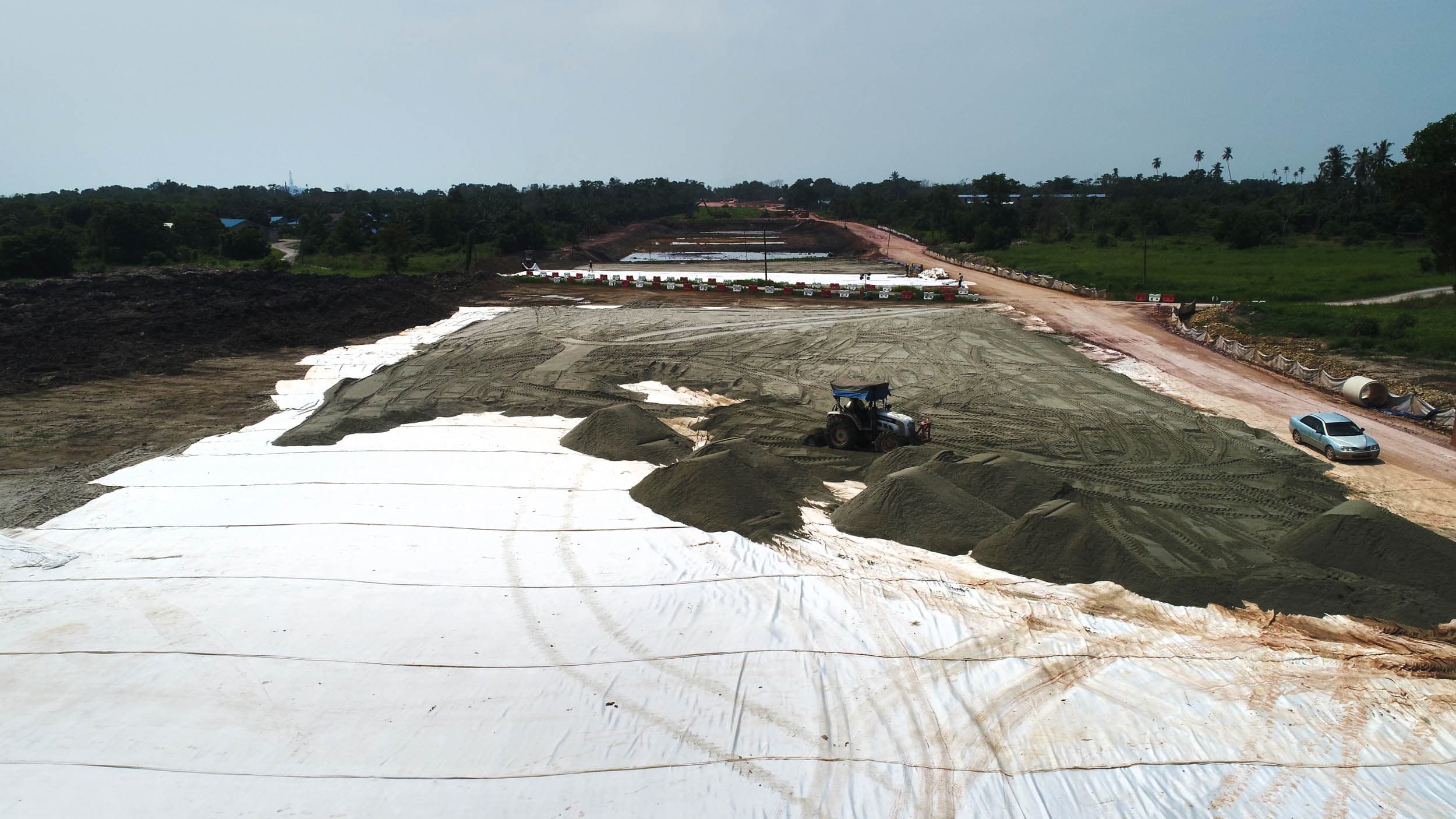
Pengerang Integrated Petroleum Complex: Basal reinforced embankment solution
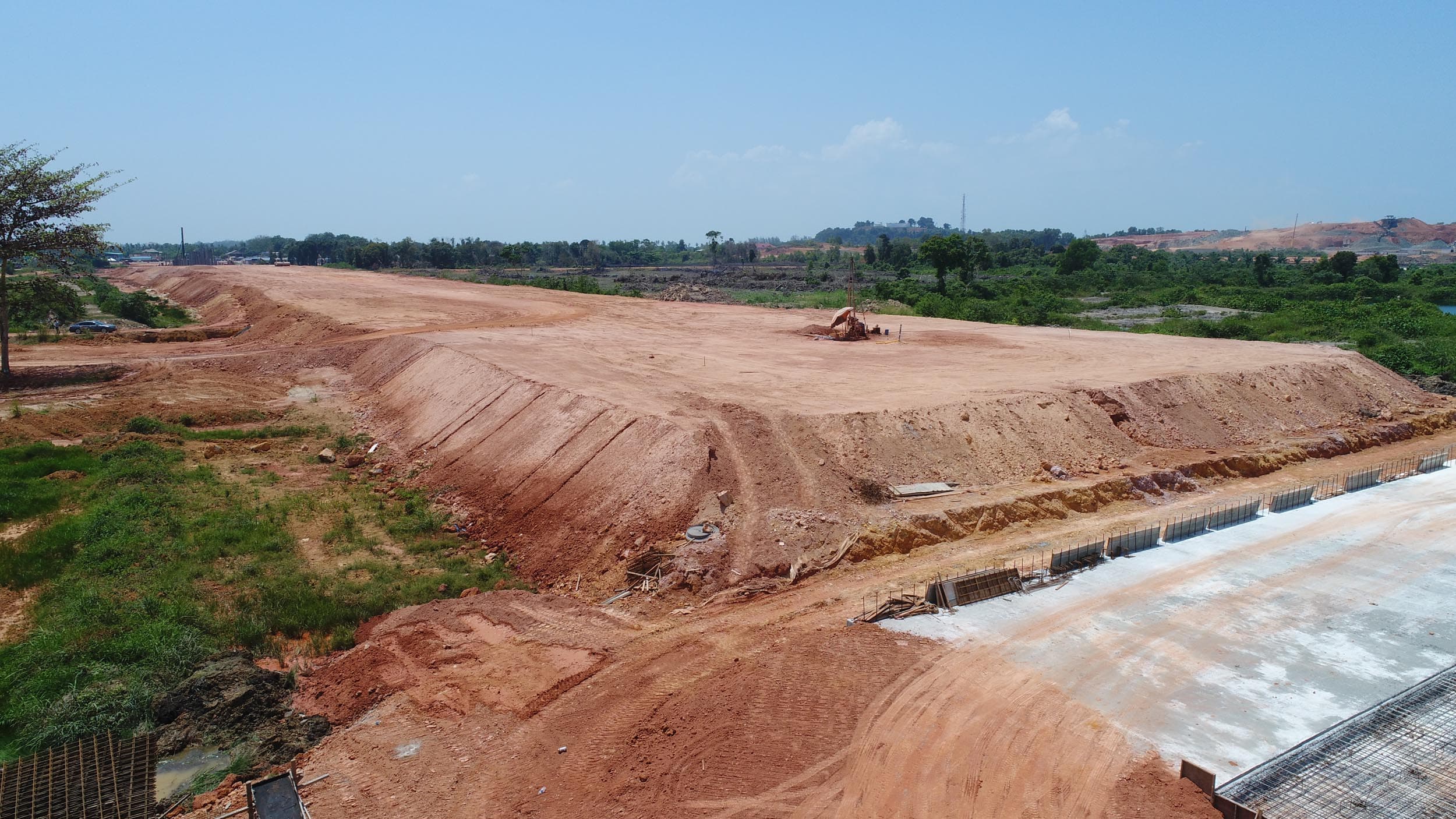
Pengerang Integrated Petroleum Complex: Basal reinforced embankment solution
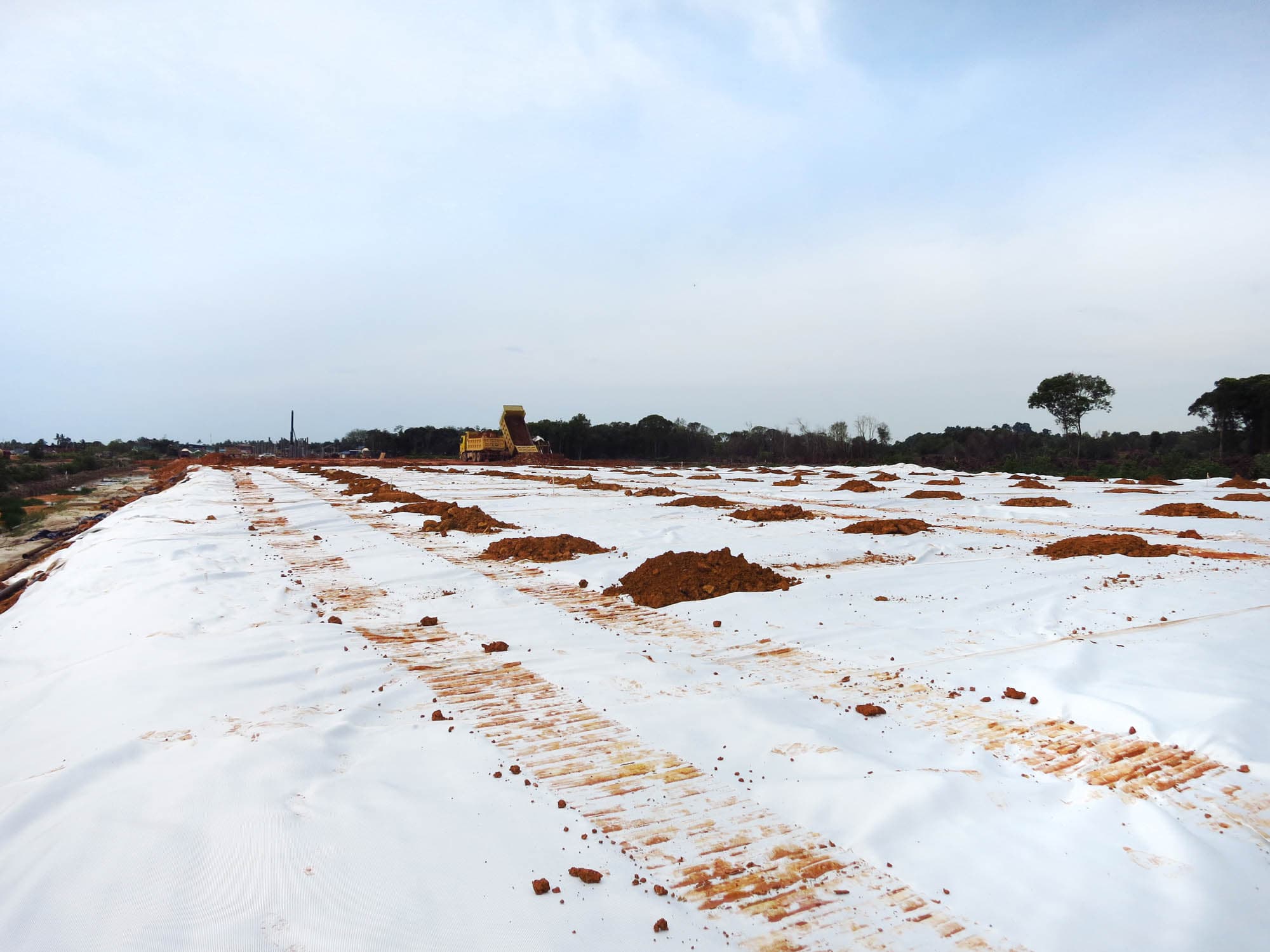
Pengerang Integrated Petroleum Complex: Basal reinforced embankment solution
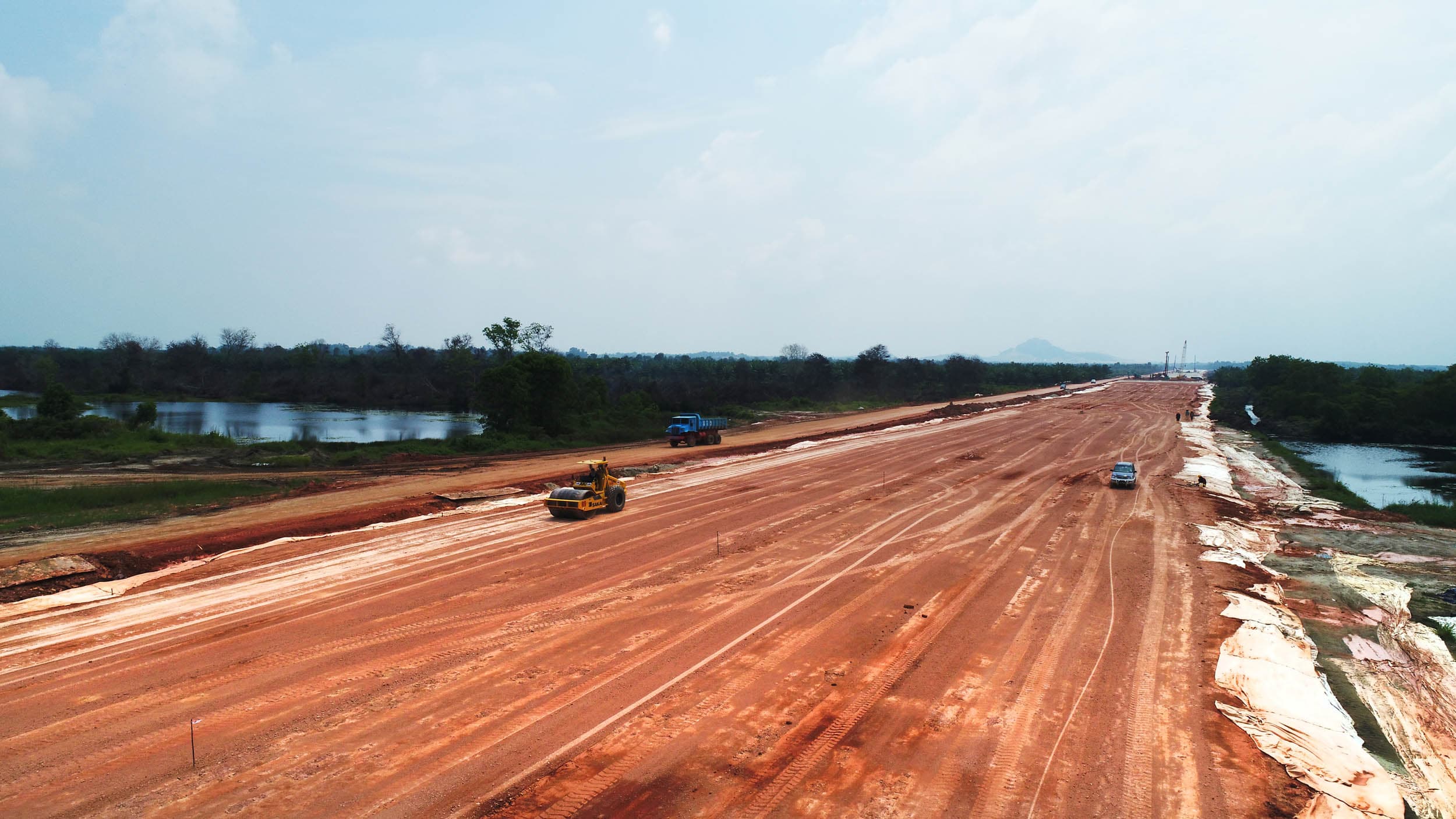
Pengerang Integrated Petroleum Complex: Basal reinforced embankment solution
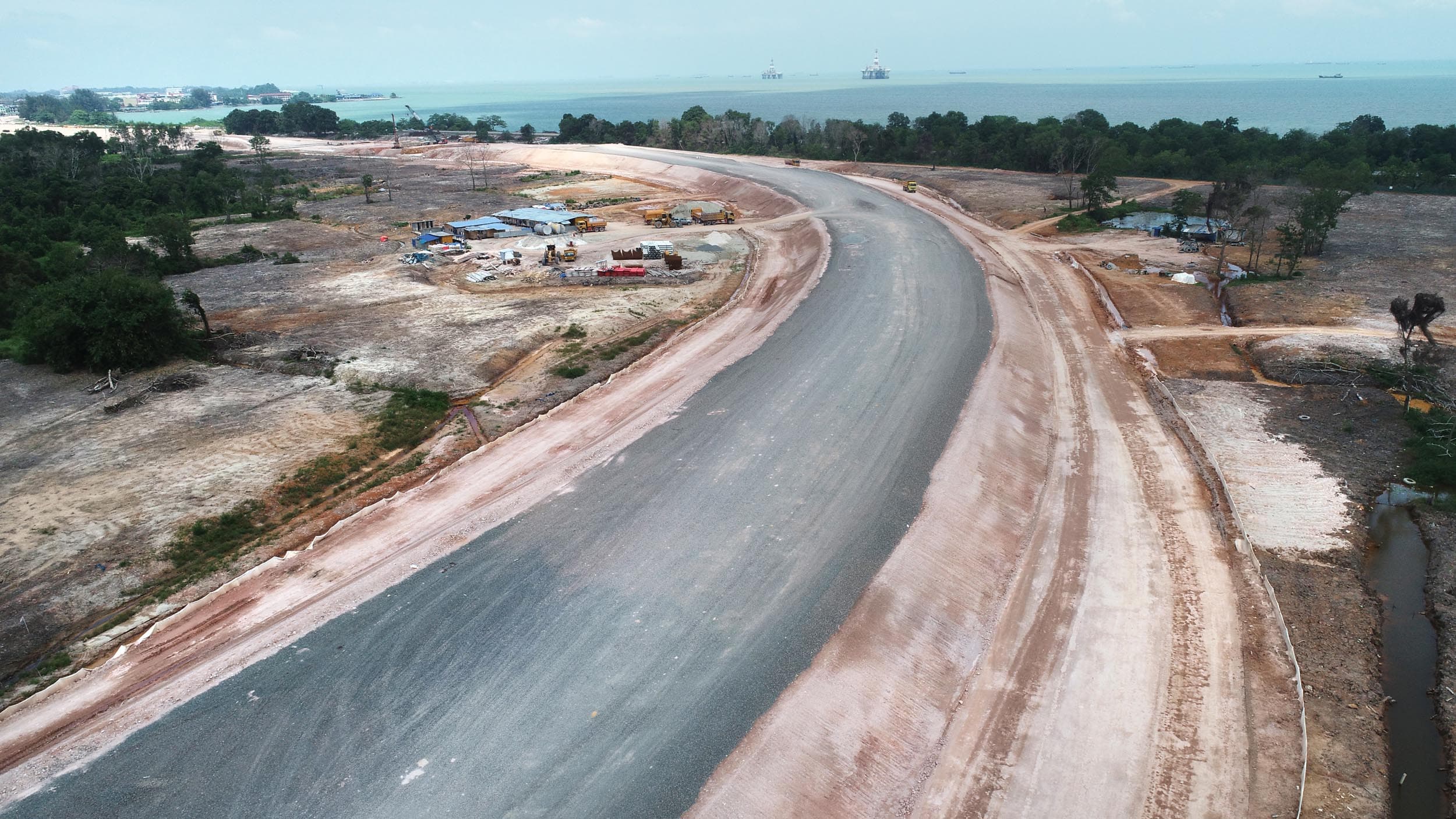
Pengerang Integrated Petroleum Complex: Basal reinforced embankment solution
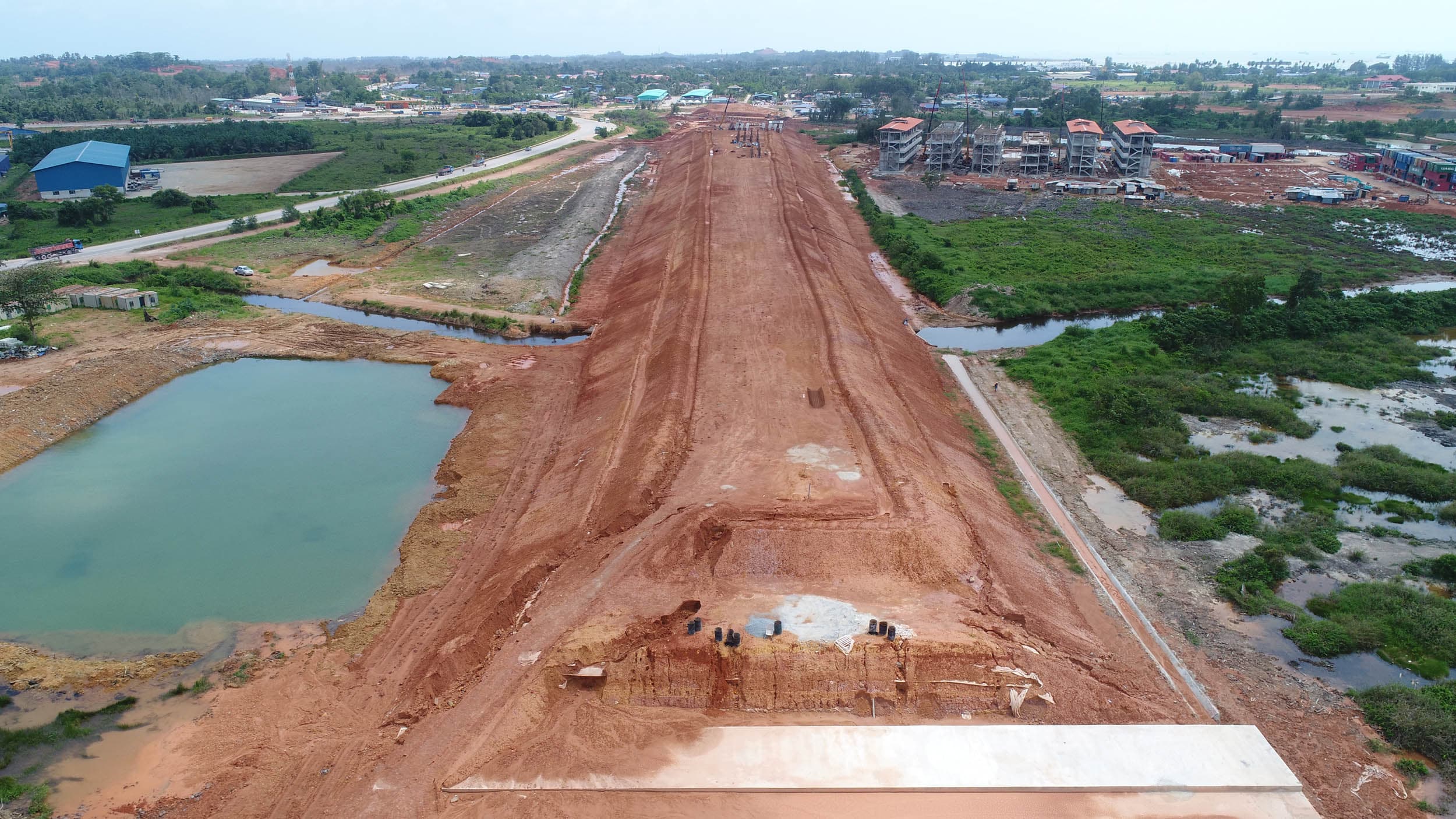
Pengerang Integrated Petroleum Complex: Basal reinforced embankment solution

Pengerang Integrated Petroleum Complex: Basal reinforced embankment solution
Explore more case studies
View all
Innovative application of new GEOTUBE technology incorporating moisture draining yarns for enhanced dewatering performance of gold tailings slurry
A gold mine in Victoria, Australia, used Solmax GEOTUBE units with moisture-absorbing wicking yarns to improve water release, efficiently managing increased slurry waste in its limited-capacity tailings storage.
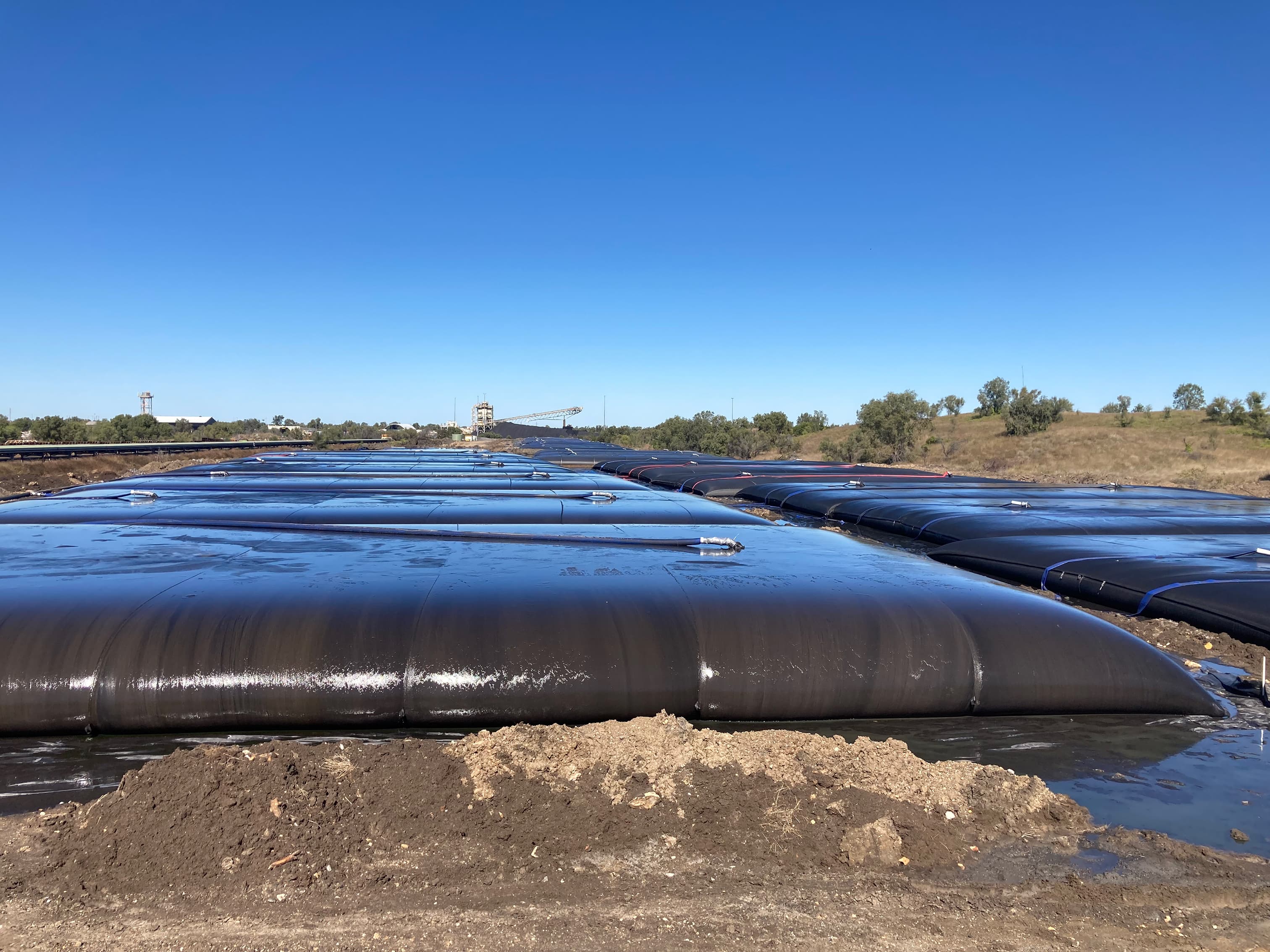
Silt trap dewatering for Kestrel Coal Mine
Kestrel Coal Resources restored silt trap capacity by dredging and dewatering 40,000m³ of silt using GEOTUBE units. The project preserved coal fines for sale.
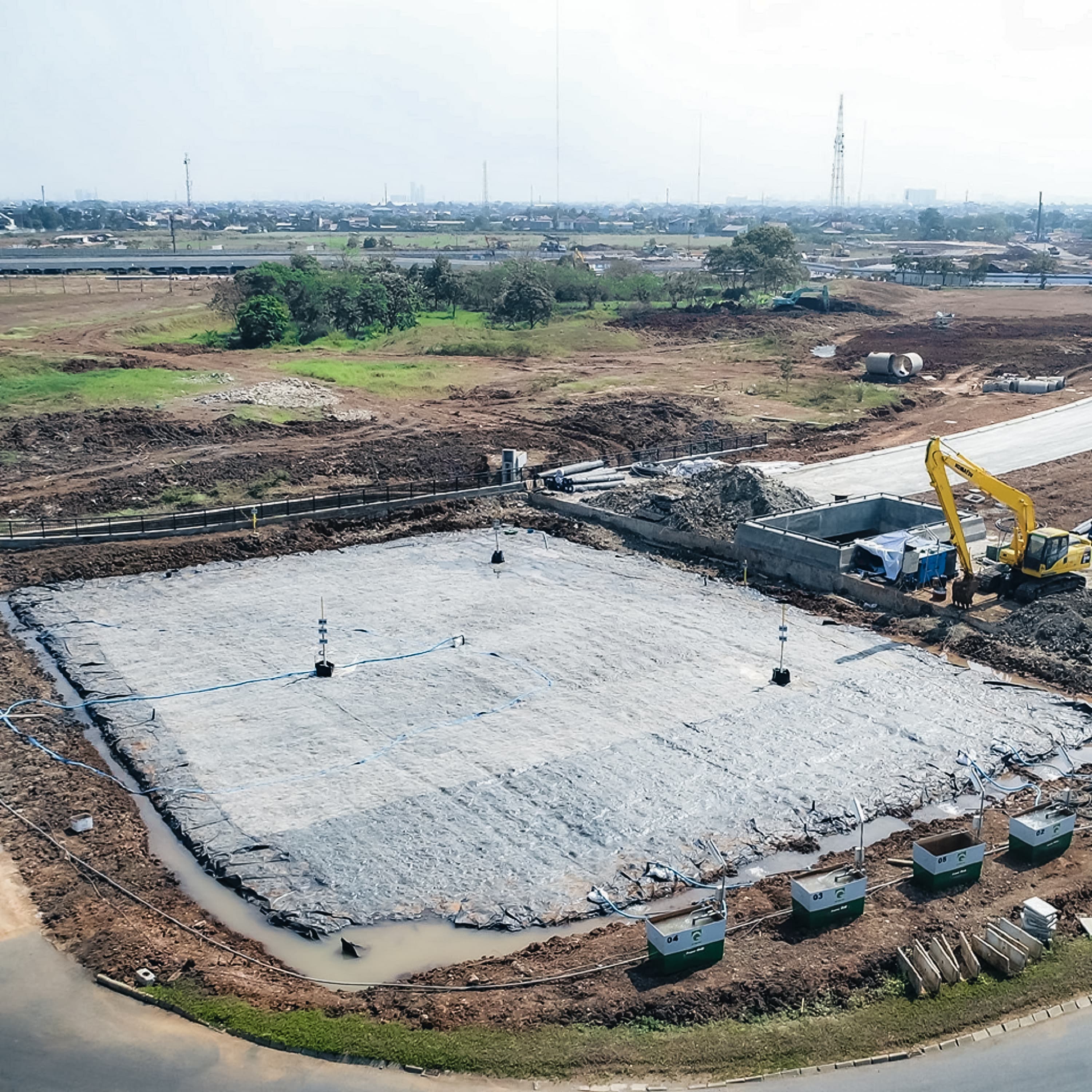
Soft-soil consolidation improvements ensure new housing development launches on time
Solmax provided a custom GSE HD geomembrane solution for the Summarecon Housing Estate in Bandung, enabling full soil consolidation in four months and ensuring the project launched on time.